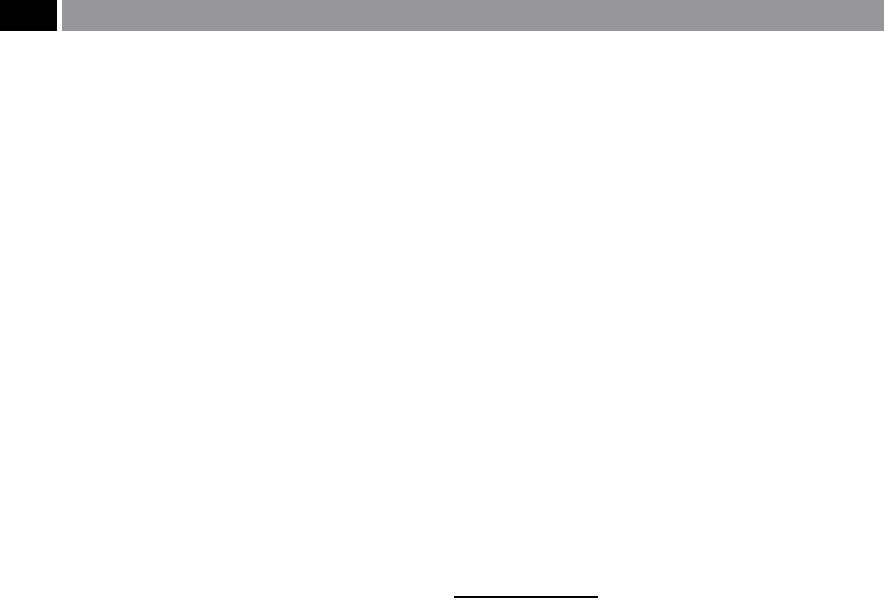
over 1°C. e hydraulic and electronic cabinets were
temperature – controlled to ± 1°C. e ‘refractive index
of the air’ had to be corrected – based upon a modi-
cation to the Edlen (1966) equation, as the laser path
positional monitoring system would otherwise be af-
fected, with a correction factor being entered into the
CNC controller.
e ‘T-shaped base’ of the Nanocentre was sup-
ported on three pneumatic mounts that were ‘tuned’ to
e
liminate oor-borne vibrations of ≥ 2.5 Hz. Two types
of vibrational sources occur, namely forced- and self-
excited, with the forced vibrations originating from
external sources – through the foundations, while the
self-excited vibrations normally being the result of in-
ternal sources. A ‘oor vibration audit’ on the vibra-
tional inuences was conducted, to establish whether
the overall enclosure was suciently vibration absor-
bent. e oor vibration spectra gave typical vibra-
t
ional readings of 1 nm (rms) at frequencies of 25 Hz,
during the tests, with the external air compressors
e
mitting a oor borne 25 Hz frequency component,
which had to be subsequently nullied. Further testing
procedures were undertaken, including ‘modal analy-
sis’ and ‘thermal imaging’ of the machine’s structure,
together with a full calibration of the machine tool’s
kinematics.
Once all of these tests and various others had been
completed and compensated for, then a machining
testing program could then be undertaken. A typi-
cal test piece is illustrated in Fig. 257b, where an al-
uminium 6061-T6 part was heat treated and then
stabilised, of φ2
50 mm copper-plated (200 µm depth
coating) part. ese testpieces were faced-o with a
monolithic diamond tool – taking very shallow D
OC
’s
of just a few micrometres, producing for example, a
f
ace-turned surface texture averaging ≈ 2.8 nm Ra.
Later, proling tests were also conducted, prior to -
nal operational acceptance by AWE, from the machine
tool builder.
Prior to completing this summation of the just
some of the rigorous testing procedures carried out to
ensure that the Nanocentre machine tool could oper-
ate within the nanometric range of ultra-high machin-
ing operation, it is worth making an unusual point
concerning human intervention at this exacting-level
of machining. It was found that when several person-
nel were within the machine tool enclosure while
machining took place, then the thermal output from
these people, inuenced the part’s dimensional size
– without actually contacting the machine, by simply
acting as a heat-emitting source
73
. Moreover, it was
also found that when diamond-turning
74
by facing-o
a very ductile testpiece similar to that depicted in Fig.
257b, when these people were in conversation during
the nanometric cutting of the part, their ‘voice signa-
tures’ – in the form of air-borne vibrations were ‘ma-
chined’ into the surface – in a similar manner to that of
an acrylic recording of a record in the past! erefore,
in order to ensure that both the human thermal eects
and the vibrational perturbations (i.e. by air-borne vi-
brations – talking), the personnel had to be removed
while any ultra-precision machining operations were
in progress.
Ultra-precision machining at these nano-metric
levels of operation, severely stretches today’s levels
of technological challenges for: machine tools, me-
trology, plant and equipment, as we approach that of
atomic-levels of precisional uncertainties
75
. It is not
just the case of purchasing an extremely accurate and
73 ‘Human body – as a heat source’. e average body – in a
‘sedentary state’ , will emit ≈100 W of heat. So, here in this
case, when there are two people present in the machine tool
enclosure, they will radiate ≈200 W of heat – inuencing
the machine’s and hence, the workpiece’s thermal expansion
– when machining at nanometric levels of accuracy and preci-
sion. (Internet source: Burruss, R.A.P., Virtual People, 2005)
74 ‘Monolithic diamond’ ,
has some of the following characteris-
tics: hardness of ≈8,000 Hv; Density (ρ) of 3,515 kg m
–3
; com-
pressive strength of 7,000 MPa; and a Young’s modulus (E) of
930 GPa.(Source: Cardarelli et al., 2000)
75 ‘Atomic radius’ ,
for example, for some typical elements, ranges
from that of: carbon, having an atomic radius of ≈0.071 nm
(i.e. its atomic ≈φ0.142 nm)*, iron’s atomic radius is ≈0.124 nm
(i.e. ≈φ0.248 nm, or ≈¼ nm)*, Aluminium’s atomic radius is
≈0.143 nm (i.e ≈φ0.286 nm, or >¼ nm), Cesium’s atomic radius
is ≈0.265 nm (i.e ≈φ0.530 nm, or >½ nm).(Source: Callister, Jr.
et al., 2003)*Slight digression here, may help explain why these
atomic radii are important, when certain elements are alloyed
together, such as iron and carbon, these being the main con-
stituents of plain carbon steel.When an allotropic change oc-
curs to the iron’s atomic lattice structure (i.e. BCC→FCC @
≈910°C), then the carbon being somewhat smaller, can t into
these (now) larger interstitial sites – voids – within the FCC
iron lattice – distorting the adjacent iron atoms. Upon rapid
cooling (e.g. by water quenching), some of the carbon is
‘trapped’ and severely distorts the structure as it attempts to
transform back to the original BCC form. Hence, this dis-
torted structure of iron-carbon – termed martensite, is both
a very hard, but brittle structure, requiring tempering: if it is
to act as a hardened and tempered workpiece material. is is
the basis (i.e. somewhat simplied), behind this iron-carbon
heat-treatment process.