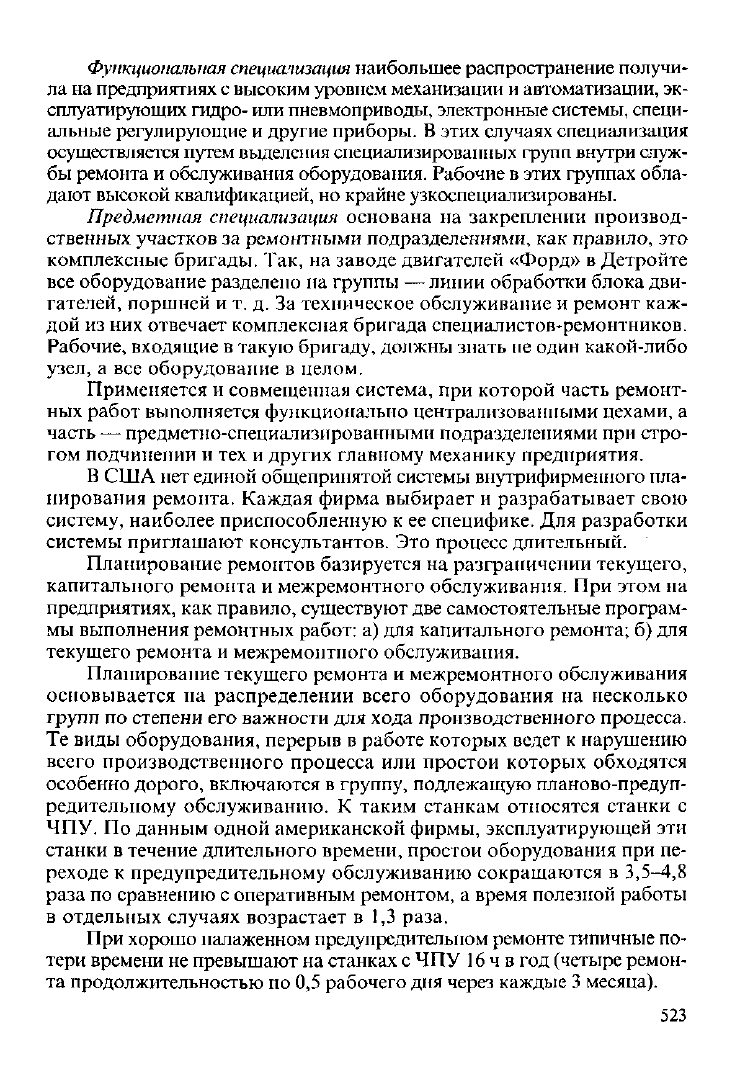
Функциональная специализация наибольшее распространение получи-
ла на предприятиях с высоким уровнем механизации и автоматизации, эк-
сплуатирующих гидро- или пневмоприводы, электронные системы, специ-
альные регулирующие и другие приборы. В этих случаях специализация
осуществляется путем выделения специализированных групп внутри служ-
бы ремонта и обслуживания оборудования. Рабочие в этих группах обла-
дают высокой квалификацией, но крайне узкоспециализированы.
Предметная специализация основана на закреплении производ-
ственных участков за ремонтными подразделениями, как правило, это
комплексные бригады. Так, на заводе двигателей «Форд» в Детройте
все оборудование разделено на группы — линии обработки блока дви-
гателей, поршней и т. д. За техническое обслуживание и ремонт каж-
дой из них отвечает комплексная бригада специалистов-ремонтников.
Рабочие, входящие в такую бригаду, должны знать не один какой-либо
узел, а все оборудование в целом.
Применяется и совмещенная система, при которой часть ремонт-
ных работ выполняется функционально централизованными цехами, а
часть — предметно-специализированными подразделениями при стро-
гом подчинении и тех и других главному механику предприятия.
В США нет единой общепринятой системы внутрифирменного пла-
нирования ремонта. Каждая фирма выбирает и разрабатывает свою
систему, наиболее приспособленную к ее специфике. Для разработки
системы приглашают консультантов. Это процесс длительный.
Планирование ремонтов базируется на разграничении текущего,
капитального ремонта и межремонтного обслуживания. При этом на
предприятиях, как правило, существуют две самостоятельные програм-
мы выполнения ремонтных работ: а) для капитального ремонта; б) для
текущего ремонта и межремонтного обслуживания.
Планирование текущего ремонта и межремонтного обслуживания
основывается на распределении всего оборудования на несколько
групп по степени его важности для хода производственного процесса.
Те виды оборудования, перерыв в работе которых ведет к нарушению
всего производственного процесса или простои которых обходятся
особенно дорого, включаются в группу, подлежащую планово-предуп-
редительному обслуживанию. К таким станкам относятся станки с
ЧПУ. По данным одной американской фирмы, эксплуатирующей эти
станки в течение длительного времени, простои оборудования при пе-
реходе к предупредительному обслуживанию сокращаются в 3,5-4,8
раза по сравнению с оперативным ремонтом, а время полезной работы
в отдельных случаях возрастает в 1,3 раза.
При хорошо налаженном предупредительном ремонте типичные по-
тери времени не превышают на станках с ЧПУ 16 ч в год (четыре ремон-
та продолжительностью по 0,5 рабочего дня через каждые 3 месяца).
523