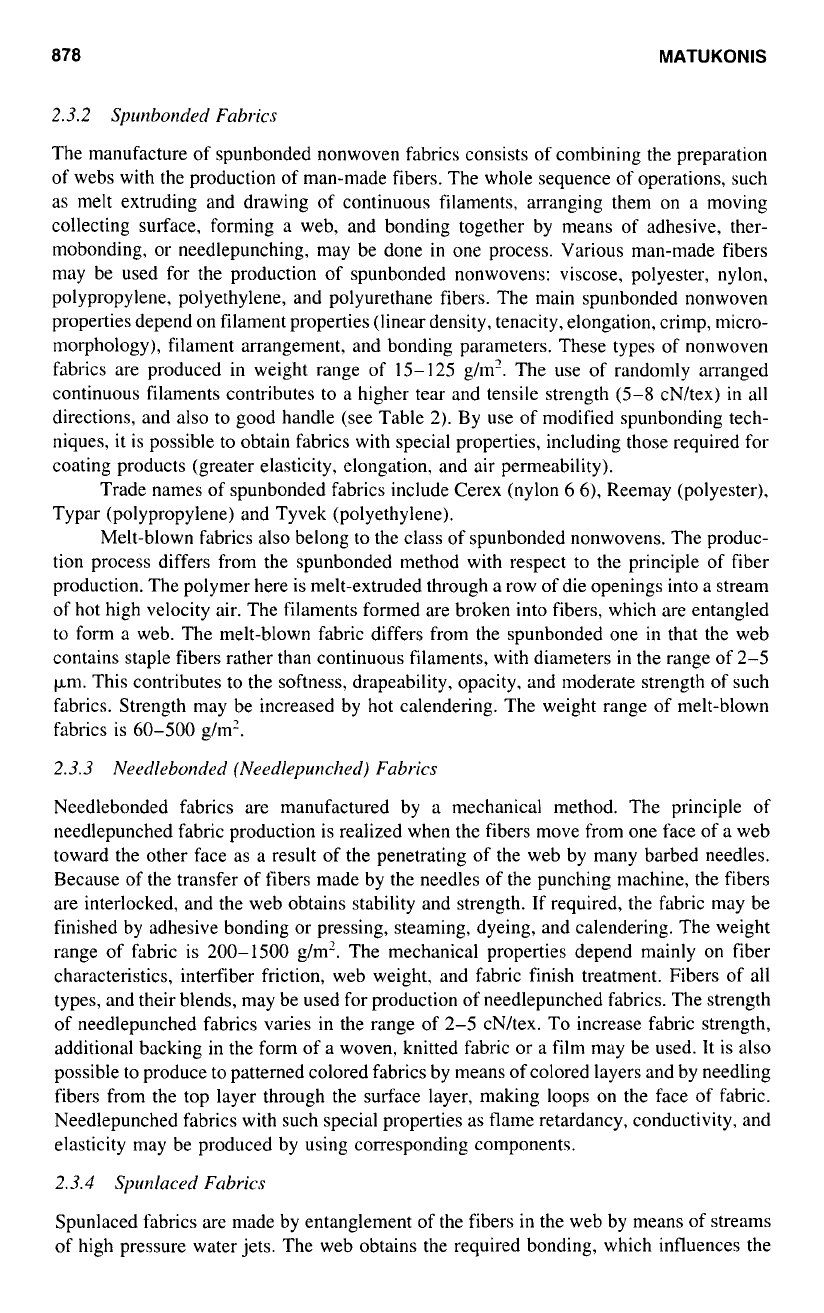
878
MATUKONIS
2.3.2
Sprnbonded Fabrics
The manufacture of spunbonded nonwoven fabrics consists of combining the preparation
of webs with the production of man-made fibers. The whole sequence of operations, such
as
melt extruding and drawing
of
continuous filaments, arranging them on a moving
collecting surface, forming
a
web, and bonding together by means of adhesive, ther-
mobonding, or needlepunching, may be done
in
one process. Various man-made fibers
may be used for the production of spunbonded nonwovens: viscose, polyester, nylon,
polypropylene, polyethylene, and polyurethane fibers. The main spunbonded nonwoven
properties depend on filament properties (linear density, tenacity, elongation, crimp, micro-
morphology), filament arrangement. and bonding parameters. These types of nonwoven
fabrics are produced in weight range of
15-125
gh'. The use of randomly arranged
continuous filaments contributes
to
a higher tear and tensile strength
(5-8
cN/tex) in all
directions, and
also
to good handle (see Table 2). By use of modified spunbonding tech-
niques,
it
is possible to obtain fabrics with special properties, including those required for
coating products (greater elasticity, elongation, and air permeability).
Trade names of spunbonded fabrics include Cerex (nylon 6
6),
Reemay (polyester),
Typar (polypropylene) and Tyvek (polyethylene).
Melt-blown fabrics
also
belong
to
the class of spunbonded nonwovens. The produc-
tion process differs from the spunbonded method with respect to the principle of fiber
production. The polymer here is melt-extruded through a row of die openings into
a
stream
of
hot high velocity air. The filaments formed are broken into fibers, which are entangled
to
form
a
web. The melt-blown fabric differs from the spunbonded one in that the web
contains staple fibers rather than continuous filaments, with diameters
in
the range of 2-5
km. This contributes to the softness, drapeability, opacity, and moderate strength
of
such
fabrics. Strength may be increased by hot calendering. The weight range of melt-blown
fabrics is 60-500 g/m'.
2.3.3
Needlebonded (Needlepuncketl) Fabrics
Needlebonded fabrics are manufactured by
a
mechanical method. The principle of
needlepunched fabric production is realized when the fibers move from one face of a web
toward the other face
as a
result of the penetrating of the web by many barbed needles.
Because of the transfer
of
fibers made by the needles of the punching machine, the fibers
are interlocked, and the web obtains stability and strength. If required, the fabric may be
finished by adhesive bonding or pressing, steaming, dyeing, and calendering. The weight
range of fabric is 200-1500 g/m'. The mechanical properties depend mainly on fiber
characteristics, interfiber friction, web weight, and fabric finish treatment. Fibers of all
types, and their blends, may be used for production of needlepunched fabrics. The strength
of needlepunched fabrics varies in the range
of
2-5 cN/tex. To increase fabric strength,
additional backing in the form of
a
woven, knitted fabric or a film may be used. It is also
possible to produce to patterned colored fabrics by means of colored layers and by needling
fibers from the top layer through the surface layer, making loops on the face of fabric.
Needlepunched fabrics with such special properties as flame retardancy, conductivity, and
elasticity may be produced by using corresponding components.
2.3.4
Sprnlaced Fabrics
Spunlaced fabrics are made by entanglement of the fibers in the web by means
of
streams
of
high pressure water jets. The web obtains the required bonding, which influences the