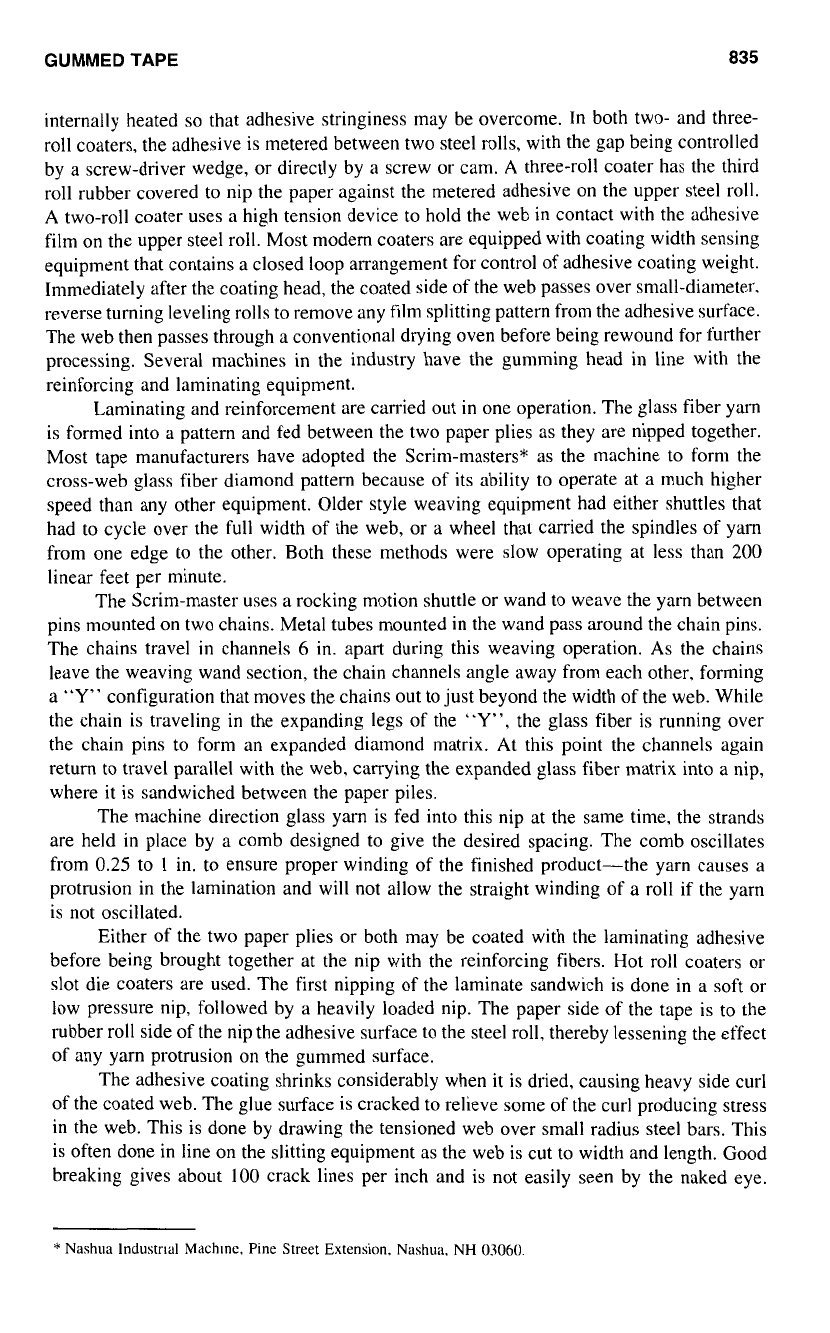
GUMMED TAPE
835
internally heated
so
that adhesive stringiness may be overcome. In both two- and three-
roll coaters, the adhesive is metered between two steel rolls, with the gap being controlled
by
a
screw-driver wedge, or directly by
a
screw or cam.
A
three-roll coater has the third
roll rubber covered
to
nip the paper against the metered adhesive on the upper steel roll.
A
two-roll coater uses
a
high tension device to hold the web in contact with the adhesive
film
on
the upper steel roll. Most modem coaters are equipped with coating width sensing
equipment that contains
a
closed loop arrangement for control of adhesive coating weight.
Immediately after the coating head, the coated side of the web passes over small-diameter.
reverse turning leveling rolls to remove any film splitting pattern from the adhesive surface.
The web then passes through
a
conventional drying oven before being rewound for further
processing. Several machines in the industry have the gumming head in line with the
reinforcing and laminating equipment.
Laminating and reinforcement are carried out
in
one operation. The glass fiber yarn
is formed into
a
pattern and fed between the two paper plies
as
they are nipped together.
Most tape manufacturers have adopted the Scrim-masters*
as
the machine to form the
cross-web glass fiber diamond pattern because
of
its ability
to
operate at
a
much higher
speed than any other equipment. Older style weaving equipment had either shuttles that
had
to
cycle over the
full
width of the web, or a wheel that carried the spindles
of
yarn
from one edge to the other. Both these methods were slow operating at less than
200
linear feet per minute.
The Scrim-master uses
a
rocking motion shuttle or wand to weave the yarn between
pins mounted
on
two chains. Metal tubes mounted
in
the wand pass around the chain pins.
The chains travel
in
channels
6
in. apart during this weaving operation.
As
the chains
leave the weaving wand section, the chain channels angle away from each other, forming
a
“Y”
configuration that moves the chains out to just beyond the width of the web. While
the chain is traveling
in
the expanding legs of the
“Y”,
the glass fiber is running over
the chain pins to form an expanded diamond matrix. At this point the channels again
return to travel parallel with the web, carrying the expanded glass fiber matrix into
a
nip,
where it is sandwiched between the paper piles.
The machine direction glass yarn is fed into this nip at the same time, the strands
are held in place by a comb designed to give the desired spacing. The comb oscillates
from
0.25
to
1
in.
to
ensure proper winding
of
the finished product-the yarn causes
a
protrusion in the lamination and will not allow the straight winding of
a
roll if the yarn
is not oscillated.
Either of the two paper plies or both may be coated with the laminating adhesive
before being brought together at the nip with the reinforcing fibers. Hot roll maters or
slot
die coaters are used. The first nipping of the laminate sandwich is done in
a
soft or
IOW
pressure nip, followed by
a
heavily loaded nip. The paper side
of
the tape is to the
rubber roll side of the nip the adhesive surface to the steel roll, thereby lessening the effect
of any yarn protrusion on the gummed surface.
The adhesive coating shrinks considerably when
it
is dried, causing heavy side curl
of the coated web. The glue surface is cracked
to
relieve some of the curl producing Stress
in
the web. This is done by drawing the tensioned web over small radius steel bars. This
is often done
in
line on the slitting equipment
as
the web is Cut to width and length. Good
breaking gives about
100
crack lines per inch and is not easily seen by the naked eye.
*
Nashua
lndustrlal Machlnc. Pine Street Extension.
Nashua.
NH
03060