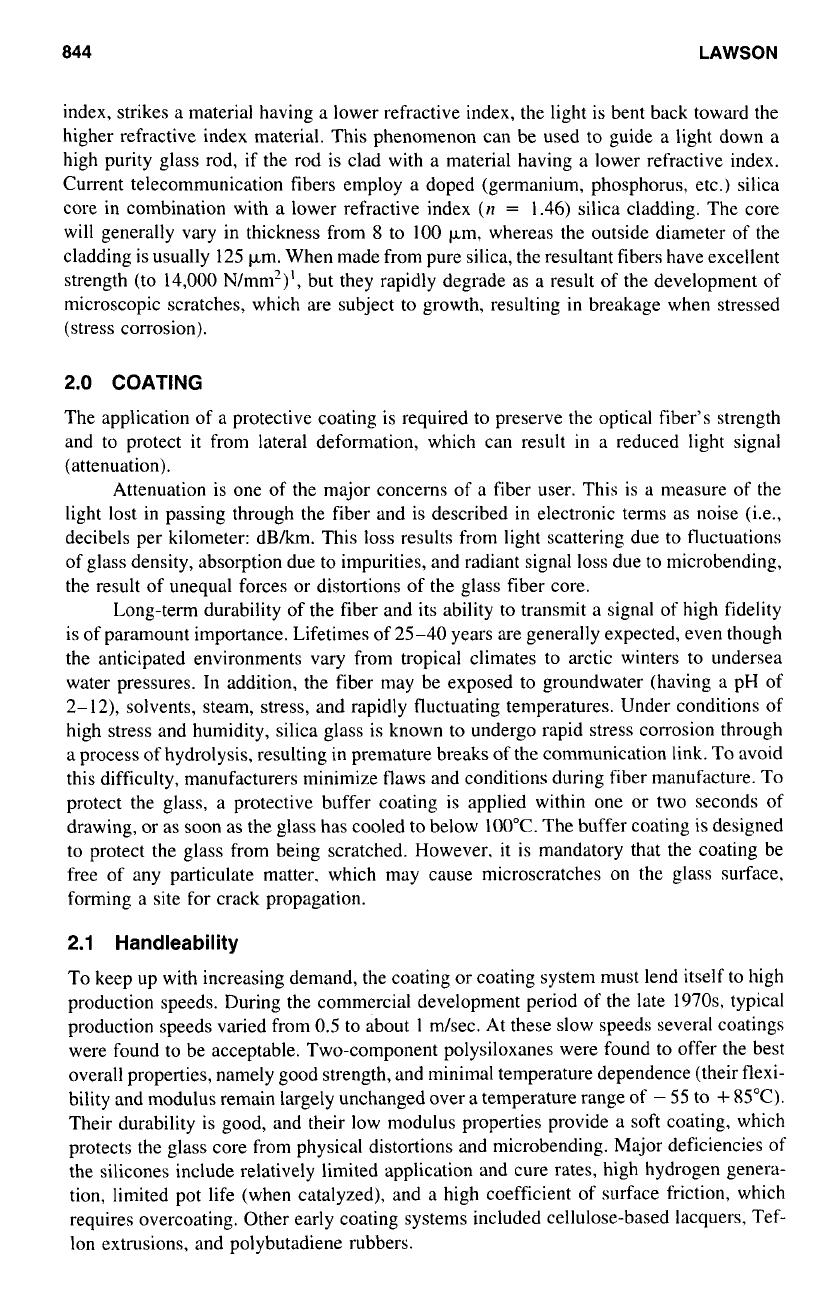
844
LAWSON
index, strikes a material having a lower refractive index, the light is bent back toward the
higher refractive index material. This phenomenon can be used
to
guide a light down a
high purity glass rod,
if
the rod is clad with a material having a lower refractive index.
Current telecommunication fibers employ a doped (germanium, phosphorus, etc.) silica
core in combination with a lower refractive index
(n
=
1.46)
silica cladding. The core
will generally vary in thickness from
8
to
100
pm, whereas the outside diameter of the
cladding is usually 125 km. When made from pure silica, the resultant fibers have excellent
strength (to
14,000
N/mm’)’, but they rapidly degrade as a result
of
the development
of
microscopic scratches, which are subject
to
growth, resulting in breakage when stressed
(stress corrosion).
2.0
COATING
The application of
a
protective coating is required
to
preserve the optical fiber’s strength
and to protect it from lateral deformation, which can result in a reduced light signal
(attenuation).
Attenuation is one of the major concerns of a fiber user. This is a measure of the
light lost in passing through the fiber and is described in electronic terms as noise (i.e.,
decibels per kilometer: dB/km. This
loss
results from light scattering due
to
fluctuations
of glass density, absorption due to impurities, and radiant signal
loss
due
to
microbending,
the result of unequal forces or distortions of the glass fiber core.
Long-term durability of the fiber and its ability
to
transmit a signal of high fidelity
is of paramount importance. Lifetimes
of
25-40 years are generally expected, even though
the anticipated environments vary from tropical climates to arctic winters to undersea
water pressures. In addition, the fiber may be exposed to groundwater (having a pH of
2- 12), solvents, steam, stress, and rapidly fluctuating temperatures. Under conditions
of
high stress and humidity, silica glass is known
to
undergo rapid stress corrosion through
a
process of hydrolysis, resulting in premature breaks of the communication link. To avoid
this difficulty, manufacturers minimize flaws and conditions during fiber manufacture. To
protect the glass, a protective buffer coating is applied within one or two seconds
of
drawing, or as soon as the glass has cooled to below 100°C. The buffer coating is designed
to protect the glass from being scratched. However, it is mandatory that the coating be
free of any particulate matter, which may cause microscratches on the glass surface,
forming a site for crack propagation.
2.1
Handleability
To keep up with increasing demand, the coating or coating system must lend itself to high
production speeds. During the commercial development period
of
the late 1970% typical
production speeds varied from
0.5
to about
1
m/sec. At these slow speeds several coatings
were found to be acceptable. Two-component polysiloxanes were found to offer the best
overall properties, namely good strength, and minimal temperature dependence (their flexi-
bility and modulus remain largely unchanged over a temperature range of
-
55
to
+
85°C).
Their durability is good, and their low modulus properties provide a soft coating, which
protects the glass core from physical distortions and microbending. Major deficiencies of
the silicones include relatively limited application and cure rates, high hydrogen genera-
tion, limited pot life (when catalyzed), and a high coefficient of surface friction, which
requires overcoating. Other early coating systems included cellulose-based lacquers, Tef-
lon extrusions, and polybutadiene rubbers.