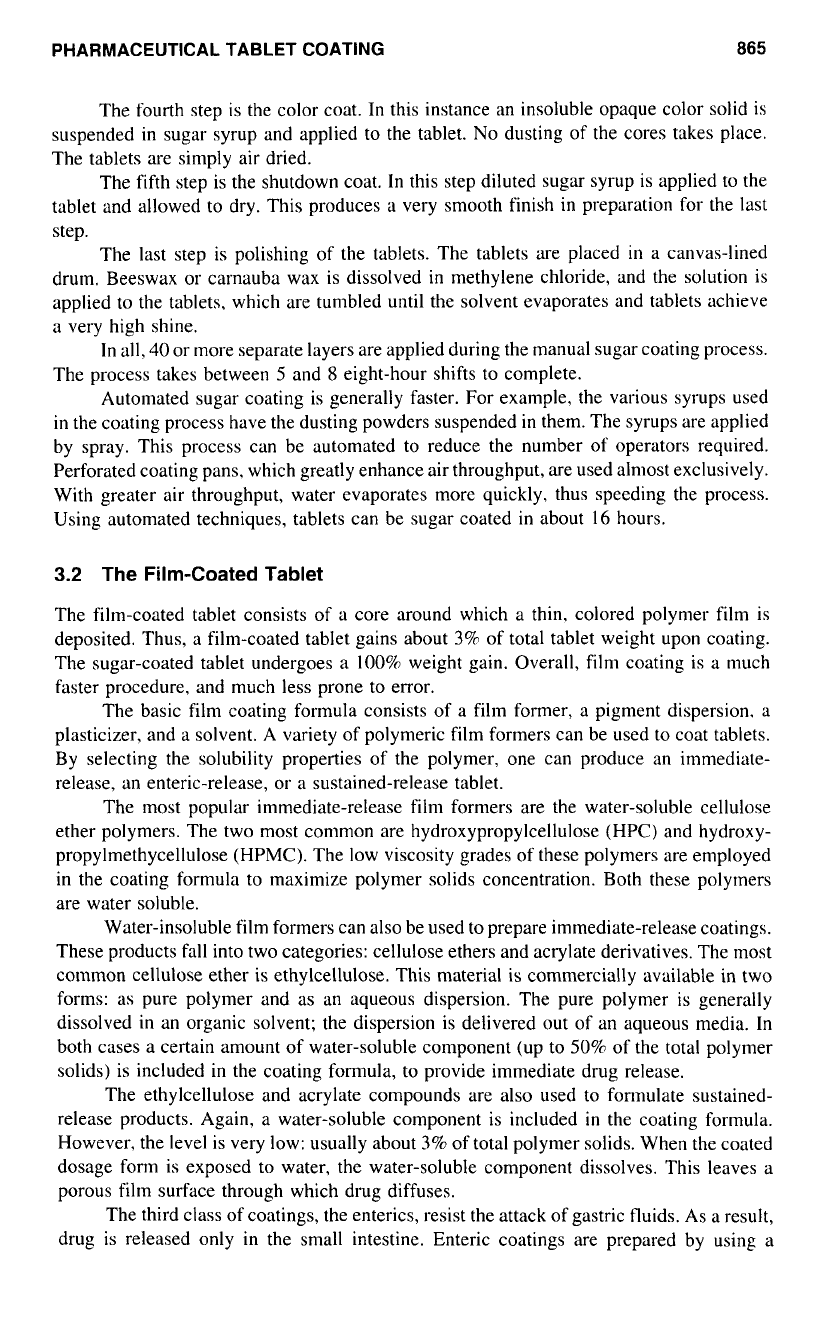
PHARMACEUTICAL TABLET COATING
865
The fourth step is the color coat. In this instance an insoluble opaque color solid is
suspended in sugar syrup and applied
to
the tablet.
No
dusting of the cores takes place.
The tablets are simply air dried.
The fifth step is the shutdown coat.
In
this step diluted sugar syrup is applied to the
tablet and allowed to dry. This produces a very smooth finish in preparation for the last
step.
The last step is polishing of
the
tablets. The tablets are placed
in
a canvas-lined
drum. Beeswax or carnauba wax is dissolved
in
methylene chloride, and the solution is
applied to the tablets, which are tumbled until the solvent evaporates and tablets achieve
a
very high shine.
In
all.
40
or more separate layers are applied during the manual sugar coating process.
The process takes between
5
and
8
eight-hour shifts to complete.
Automated sugar coating is generally faster. For example, the various syrups used
in the coating process have the dusting powders suspended
in
them. The syrups are applied
by spray. This process can be automated to reduce the number of operators required.
Perforated coating pans, which greatly enhance air throughput, are used almost exclusively.
With greater air throughput, water evaporates more quickly, thus speeding the process.
Using automated techniques, tablets can be sugar coated in about
16
hours.
3.2
The Film-Coated Tablet
The film-coated tablet consists of a core around which a thin, colored polymer film is
deposited. Thus, a film-coated tablet gains about
3%
of total tablet weight upon coating.
The sugar-coated tablet undergoes
a
100%
weight gain. Overall, film coating is a much
faster procedure, and much less prone to error.
The basic film coating formula consists of a film former, a pigment dispersion. a
plasticizer. and a solvent.
A
variety
of
polymeric film formers can be used
to
coat tablets.
By selecting the solubility properties of the polymer, one can produce an immediate-
release, an enteric-release, or
a
sustained-release tablet.
The most popular immediate-release film formers are the water-soluble cellulose
ether polymers. The two most common are hydroxypropylcellulose (HPC) and hydroxy-
propylmethycellulose (HPMC). The low viscosity grades of these polymers are employed
in the coating formula to maximize polymer solids concentration. Both these polymers
are water soluble.
Water-insoluble film formers can also be used
to
prepare immediate-release coatings.
These products fall into two categories: cellulose ethers and acrylate derivatives. The most
common cellulose ether is ethylcellulose. This material is commercially available in two
forms: as pure polymer and as an aqueous dispersion. The pure polymer is generally
dissolved in an organic solvent; the dispersion is delivered out of an aqueous media.
In
both cases
a
certain amount of water-soluble component (up to
50%
of the total polymer
solids) is included
in
the coating formula, to provide immediate drug release.
The ethylcellulose and acrylate compounds are
also
used
to
formulate sustained-
release products. Again,
a
water-soluble component is included
in
the coating formula.
However, the level is very low: usually about
3%
of
total polymer solids. When the coated
dosage form is exposed to water, the water-soluble component dissolves. This leaves
a
porous film surface through which drug diffuses.
The third class ofcoatings, the enterics, resist the attack of gastric tluids.
As
a result,
drug is released only in the small intestine. Enteric coatings are prepared by using a