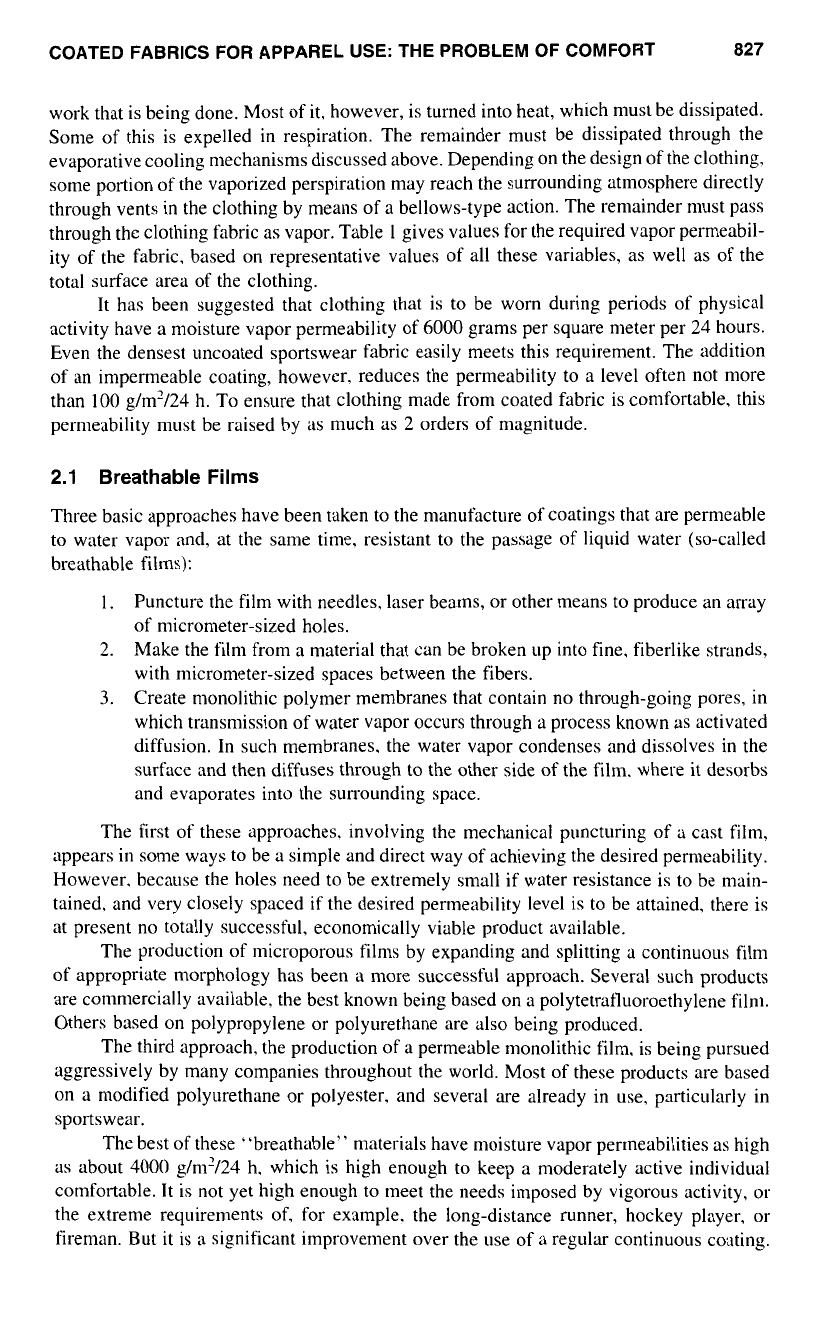
COATED FABRICS
FOR
APPAREL USE: THE PROBLEM OF COMFORT
827
work that is being done. Most of it, however, is turned into heat, which must be dissipated.
Some
of
this is expelled in respiration. The remainder must be dissipated through the
evaporative cooling nlechanisms discussed above. Depending on the design of the clothing.
some portion of the vaporized perspiration may reach the surrounding atmosphere directly
through vents
in
the clothing by means of a bellows-type action. The remainder must pass
through the clothing fabric as vapor. Table
1
gives values for the required vapor permeabil-
ity of the fabric, based on representative values of all these variables, as well as
of
the
total surface area of the clothing.
It has been suggested that clothing that is
to
be worn during periods of physical
activity have a moisture vapor permeability of 6000 grams per square meter per
24
hours.
Even the densest uncoated sportswear fabric easily meets this requirement. The addition
of an impermeable coating, however. reduces the permeability to a level often not more
than 100 g/m’/24 h. To ensure that clothing made from coated fabric is comfortable, this
permeability must be raised by
as
much as
2
orders of magnitude.
2.1
Breathable
Films
Three basic approaches have been taken to the manufacture of coatings that are permeable
to water vapor and, at the same time, resistant to the passage of liquid water (so-called
breathable films):
1.
Puncture the film with needles, laser beams, or other means to produce an array
of micrometer-sized holes.
2.
Make the film from a material that can be broken up into fine, fiberlike strands,
with micrometer-sized spaces between the fibers.
3.
Create monolithic polymer membranes that contain no through-going pores, in
which transmission
of
water vapor occurs through a process known as activated
diffusion. In such membranes. the water vapor condenses and dissolves
in
the
surface and then diffuses through to the other side
of
the film. where it desorbs
and evaporates into the surrounding space.
The first of these approaches. involving the mechanical puncturing
of
a cast film,
appears in some ways to be a simple and direct way of achieving the desired permeability.
However. because the holes need to be extremely small
if
water resistance is to be main-
tained, and very closely spaced
if
the desired permeability level is to be attained. there is
at present no totally successful, economically viable product available.
The production
of
microporous films by expanding and splitting a continuous film
of appropriate morphology has been a more successful approach. Several such products
are commercially available. the best known being based on a polytetrafluoroethylene film.
Others based
on
polypropylene
or
polyurethane are also being produced.
The third approach, the production of a permeable monolithic film. is being pursued
aggressively by many companies throughout the world. Most of these products are based
on a modified polyurethane or polyester. and several are already in use, particularly in
sportswear.
The best of these “breathable” materials have moisture vapor permeabilities as high
as about 4000 g/m’/24 h. which is high enough
to
keep a moderately active individual
comfortable.
It
is not yet high enough to meet the needs imposed by vigorous activity, or
the extreme requirements of. for example. the long-distance runner, hockey player, or
fireman. But
it
is
a
significant improvement over the use of a regular continuous coating.