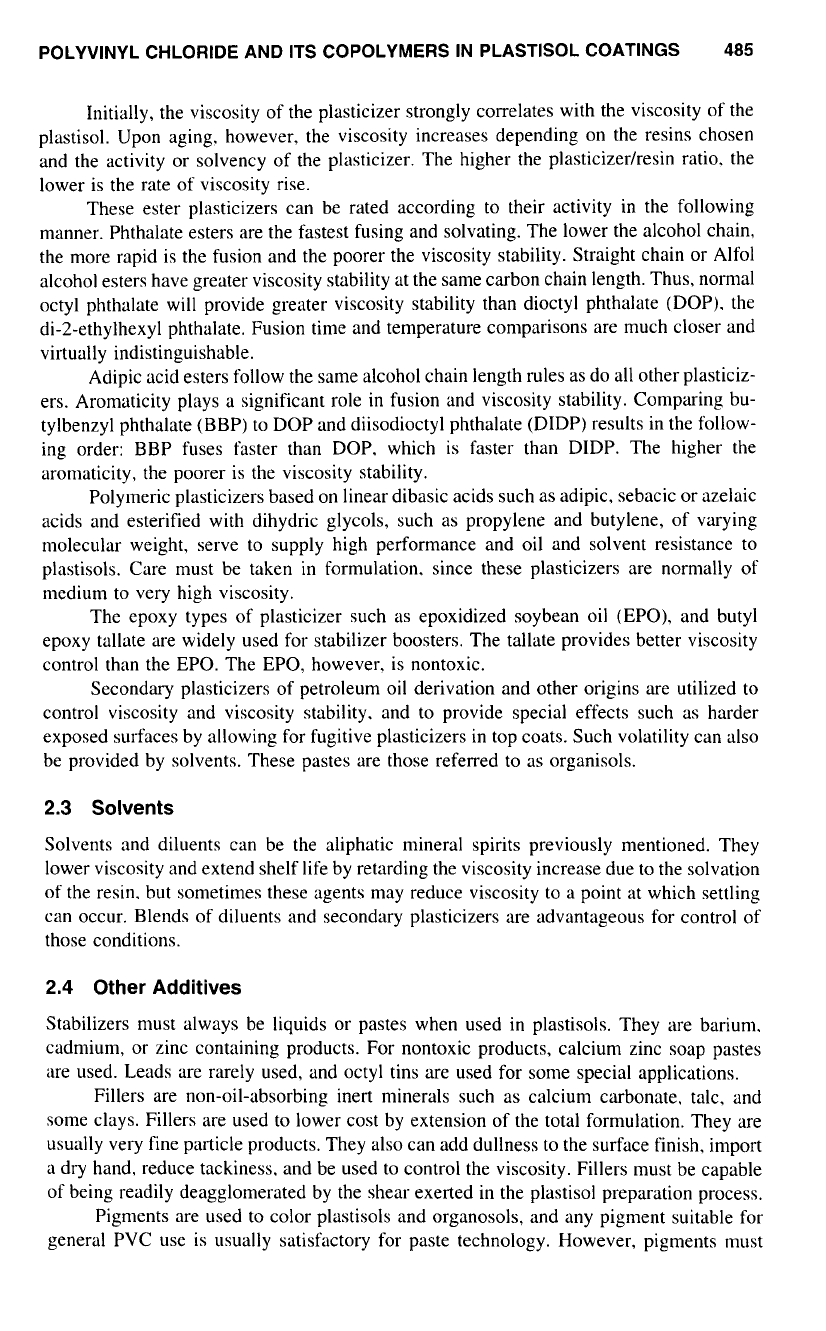
POLYVINYL CHLORIDE AND ITS COPOLYMERS IN PLASTISOL COATINGS
485
Initially, the viscosity of the plasticizer strongly correlates with the viscosity of the
plastisol. Upon aging. however, the viscosity increases depending
on
the resins chosen
and the activity or solvency of the plasticizer. The higher the plasticizer/resin ratio, the
lower is the rate
of
viscosity rise.
These ester plasticizers can be rated according
to
their activity in the following
manner. Phthalate esters are the fastest fusing and solvating. The lower the alcohol chain,
the more rapid is the fusion and the poorer the viscosity stability. Straight chain or Alfol
alcohol esters have greater viscosity stability at the same carbon chain length. Thus, normal
octyl phthalate will provide greater viscosity stability than dioctyl phthalate (DOP). the
di-2-ethylhexyl phthalate. Fusion time and temperature comparisons are much closer and
virtually indistinguishable.
Adipic acid esters follow the same alcohol chain length rules as do all other plasticiz-
ers. Aromaticity plays a significant role in fusion and viscosity stability. Comparing bu-
tylbenzyl phthalate (BBP) to DOP and diisodioctyl phthalate (DIDP) results in the follow-
ing order: BBP fuses faster than DOP, which is faster than DIDP. The higher the
aromaticity, the poorer is the viscosity stability.
Polymeric plasticizers based on linear dibasic acids such as adipic, sebacic or azelaic
acids and esterified with dihydric glycols, such as propylene and butylene,
of
varying
molecular weight, serve to supply high performance and
oil
and solvent resistance to
plastisols. Care must be taken
in
formulation. since these plasticizers are normally
of
medium to very high viscosity.
The epoxy types
of
plasticizer such as epoxidized soybean oil (EPO), and butyl
epoxy tallate are widely used for stabilizer boosters. The tallate provides better viscosity
control than the EPO. The EPO, however. is nontoxic.
Secondary plasticizers of petroleum oil derivation and other origins are utilized
to
control viscosity and viscosity stability. and to provide special effects such as harder
exposed surfaces by allowing for fugitive plasticizers in top coats. Such volatility can also
be provided by solvents. These pastes are those referred to as organisols.
2.3
Solvents
Solvents and diluents can be the aliphatic mineral spirits previously mentioned. They
lower viscosity and extend shelf life by retarding the viscosity increase due to the solvation
of
the resin. but sometimes these agents may reduce viscosity to a point at which settling
can occur. Blends of diluents and secondary plasticizers are advantageous for control of
those conditions.
2.4
Other Additives
Stabilizers must always be liquids or pastes when used in plastisols. They are barium.
cadmium, or zinc containing products. For nontoxic products, calcium zinc soap pastes
are used. Leads are rarely used, and octyl tins are used for some special applications.
Fillers are non-oil-absorbing inert minerals such as calcium carbonate. talc, and
some clays. Fillers are used
to
lower cost by extension of the total formulation. They are
usually very fine particle products. They also can add dullness to the surface finish, import
a dry hand, reduce tackiness. and be used to control the viscosity. Fillers must be capable
of being readily deagglomerated by the shear exerted in the plastisol preparation process.
Pigments are used
to
color plastisols and organosols, and any pigment suitable for
general PVC use is usually satisfactory for paste technology. However, pigments must