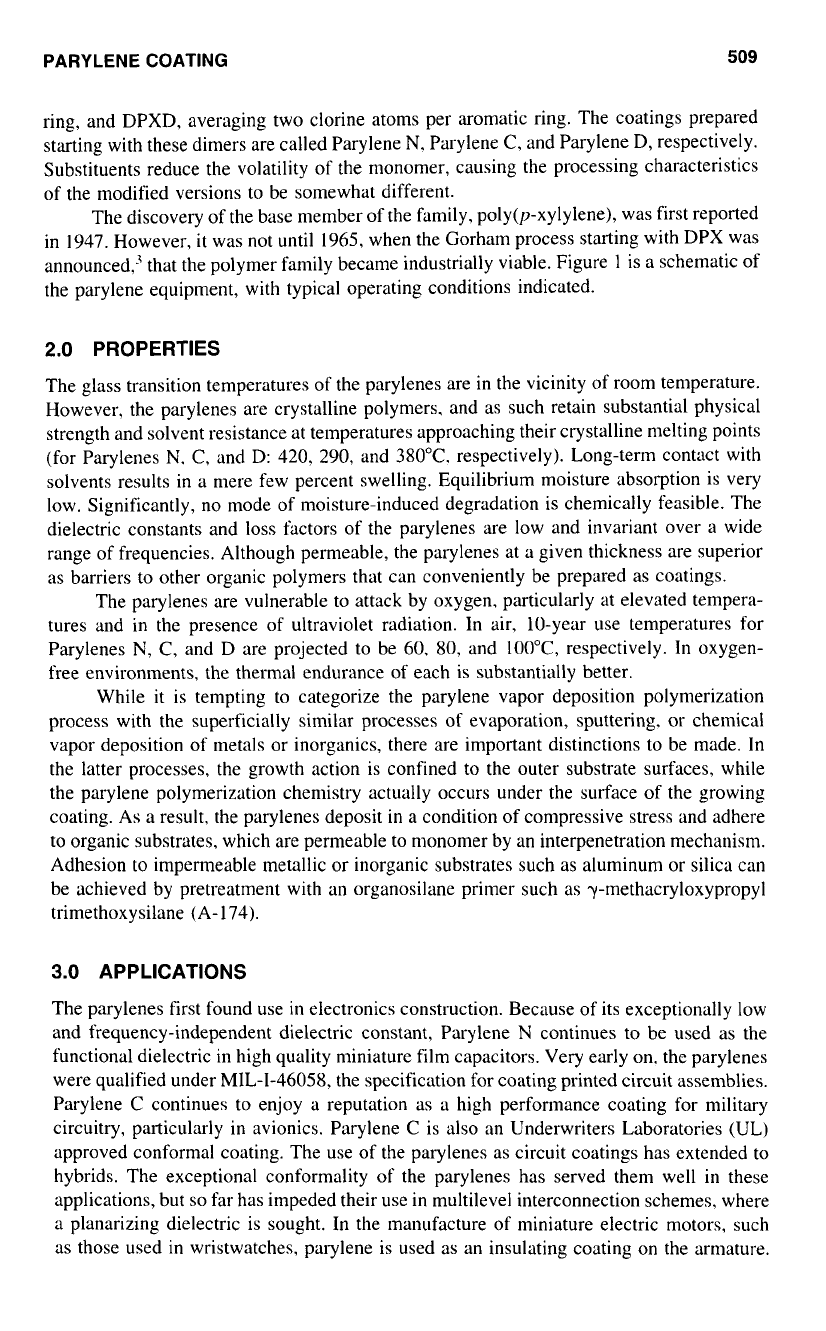
PARYLENE COATING
509
ring, and DPXD, averaging two clorine atoms per aromatic ring. The coatings prepared
starting with these dimers are called Parylene
N.
Parylene
C,
and Parylene D, respectively.
Substituents reduce the volatility
of
the monomer, causing the processing characteristics
of the modified versions to be somewhat different.
The discovery of the base member of the family, poly(p-xylylene), was first reported
in 1947. However,
it
was not until
1965,
when the Gorham process starting with DPX was
announced,3 that the polymer family became industrially viable. Figure
1
is a schematic
of
the parylene equipment, with typical operating conditions indicated.
2.0
PROPERTIES
The glass transition temperatures of the parylenes are
in
the vicinity of room tenlperature.
However, the parylenes are crystalline polymers, and as such retain substantial physical
strength and solvent resistance at temperatures approaching their crystalline melting points
(for Parylenes
N.
C,
and D:
420, 290,
and
380°C.
respectively). Long-term contact with
solvents results in a mere few percent swelling. Equilibrium moisture absorption is very
low. Significantly, no mode of moisture-induced degradation is chemically feasible. The
dielectric constants and
loss
factors of the parylenes are low and invariant over a wide
range
of
frequencies. Although permeable, the parylenes at a given thickness are superior
as barriers to other organic polymers that can conveniently be prepared as coatings.
The parylenes are vulnerable to attack by oxygen, particularly at elevated tempera-
tures and in the presence
of
ultraviolet radiation. In air, 10-year use temperatures for
Parylenes
N,
C,
and D are projected to be
60, 80,
and
100"C,
respectively.
In
oxygen-
free environments, the thermal endurance of each is substantially better.
While it is tempting to categorize the parylene vapor deposition polymerization
process with the superficially similar processes of evaporation, sputtering. or chemical
vapor deposition of metals or inorganics, there are important distinctions to be made.
In
the latter processes, the growth action is confined to the outer substrate surfaces, while
the parylene polymerization chemistry actually occurs under the surface
of
the growing
coating.
As
a result, the parylenes deposit in a condition
of
compressive stress and adhere
to organic substrates, which are permeable to monomer by an interpenetration mechanism.
Adhesion
to
impermeable metallic
or
inorganic substrates such as aluminum or silica can
be achieved by pretreatment with an organosilane primer such as y-methacryloxypropyl
trimethoxysilane (A-174).
3.0
APPLICATIONS
The parylenes first found use
in
electronics construction. Because of its exceptionally low
and frequency-independent dielectric constant, Parylene
N
continues to be used as the
functional dielectric in high quality miniature film capacitors. Very early on. the parylenes
were qualified under
MIL-1-46058,
the specification for coating printed circuit assemblies.
Parylene
C
continues to enjoy a reputation as a high performance coating for military
circuitry, particularly in avionics. Parylene
C
is
also
an Underwriters Laboratories (UL)
approved conformal coating. The use of the parylenes as circuit coatings has extended
to
hybrids. The exceptional conformality
of
the parylenes has served them well in these
applications, but
so
far has impeded their use in multilevel interconnection schemes, where
a planarizing dielectric is sought. In the Inanufacture of miniature electric motors, such
as those used
in
wristwatches, palylene is used as an insulating coating on the armature.