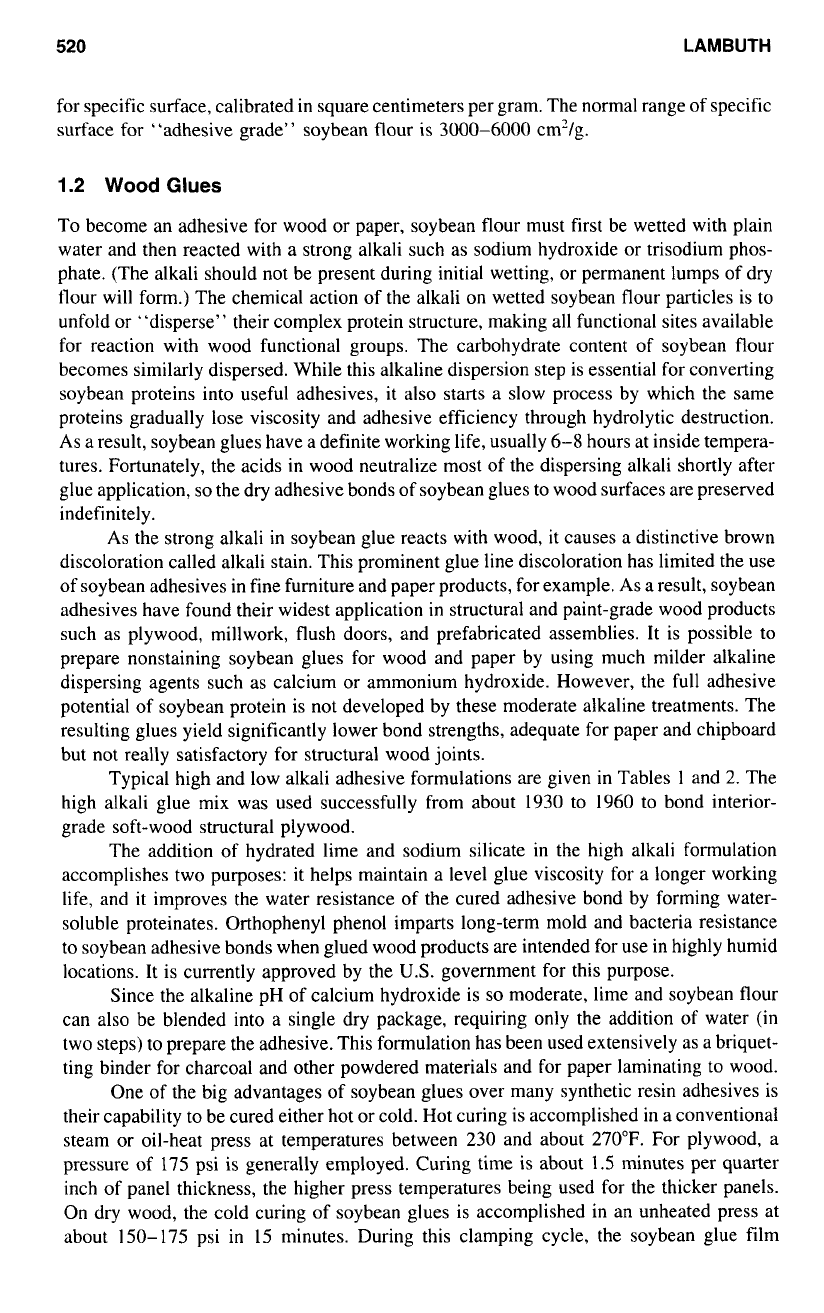
520
LAMBUTH
for specific surface, calibrated in square centimeters per gram. The normal range
of
specific
surface
for
“adhesive grade” soybean flour is 3000-6000 cm’lg.
1.2
Wood
Glues
To become an adhesive for wood or paper, soybean flour must first be wetted with plain
water and then reacted with
a
strong alkali such
as
sodium hydroxide or trisodium phos-
phate. (The alkali should not be present during initial wetting, or permanent lumps of dry
flour will form.) The chemical action of the alkali
on
wetted soybean flour particles is to
unfold or “disperse” their complex protein structure, making
all
functional sites available
for reaction with wood functional groups. The carbohydrate content
of
soybean flour
becomes similarly dispersed. While this alkaline dispersion step is essential for converting
soybean proteins into useful adhesives, it
also
starts
a
slow process by which the same
proteins gradually lose viscosity and adhesive efficiency through hydrolytic destruction.
As
a
result, soybean glues have
a
definite working life, usually 6-8 hours at inside tempera-
tures. Fortunately, the acids in wood neutralize most of the dispersing alkali shortly after
glue application,
so
the dry adhesive bonds of soybean glues to wood surfaces are preserved
indefinitely.
As
the strong alkali
in
soybean glue reacts with wood,
it
causes
a
distinctive brown
discoloration called alkali stain. This prominent glue line discoloration has limited the use
of
soybean adhesives in fine furniture and paper products, for example.
As
a
result, soybean
adhesives have found their widest application in structural and paint-grade wood products
such
as
plywood, millwork, flush doors, and prefabricated assemblies. It is possible to
prepare nonstaining soybean glues for wood and paper by using much milder alkaline
dispersing agents such
as
calcium or ammonium hydroxide. However, the
full
adhesive
potential of soybean protein is not developed by these moderate alkaline treatments. The
resulting glues yield significantly lower bond strengths, adequate for paper and chipboard
but not really satisfactory for structural wood joints.
Typical high and low alkali adhesive formulations are given in Tables
1
and 2. The
high alkali glue mix was used successfully from about 1930 to
1960
to bond interior-
grade soft-wood structural plywood.
The addition
of
hydrated lime and sodium silicate in the high alkali formulation
accomplishes two purposes: it helps maintain
a
level glue viscosity for
a
longer working
life, and it improves the water resistance
of
the cured adhesive bond by forming water-
soluble proteinates. Orthophenyl phenol imparts long-term mold and bacteria resistance
to soybean adhesive bonds when glued wood products are intended for use in highly humid
locations. It is currently approved by the
U.S.
government for this purpose.
Since the alkaline pH of calcium hydroxide is
so
moderate, lime and soybean flour
can
also
be blended into
a
single dry package, requiring only the addition
of
water (in
two steps) to prepare the adhesive. This formulation
has
been used extensively
as
a briquet-
ting binder for charcoal and other powdered materials and for paper laminating to wood.
One of the big advantages of soybean glues over many synthetic resin adhesives is
their capability to be cured either hot or cold. Hot curing is accomplished in
a
conventional
steam or oil-heat press at temperatures between 230 and about 270°F. For plywood,
a
pressure
of
175 psi is generally employed. Curing time is about
1.5
minutes per quarter
inch of panel thickness, the higher press temperatures being used for the thicker panels.
On dry wood, the cold curing of soybean glues is accomplished in an unheated press at
about 150-175 psi
in
15 minutes. During this clamping cycle, the soybean glue film