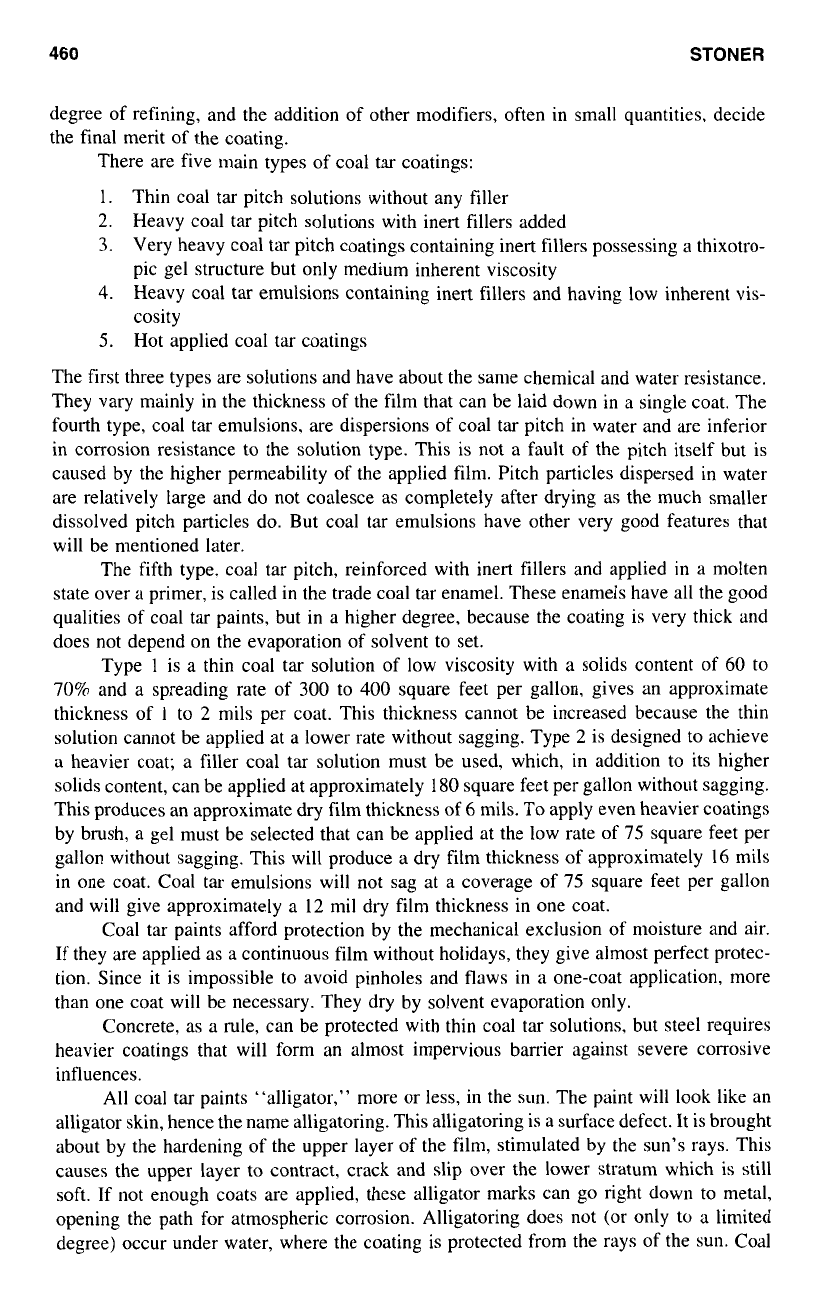
460
STONER
degree of refining, and the addition of other modifiers, often in small quantities, decide
the final merit of the coating.
There are five main types
of
coal tar coatings:
1.
Thin coal
tar
pitch solutions without any filler
2. Heavy coal tar pitch solutions with inert fillers added
3.
Very heavy coal tar pitch coatings containing inert fillers possessing a thixotro-
4.
Heavy coal tar emulsions containing inert fillers and having low inherent vis-
5.
Hot applied coal tar coatings
pic gel structure but only medium inherent viscosity
cosity
The first three types are solutions and have about the same chemical and water resistance.
They vary mainly in the thickness of the film that can be laid down in a single coat. The
fourth type, coal tar emulsions, are dispersions of coal tar pitch in water and are inferior
in corrosion resistance to the solution type. This is not
a
fault of the pitch itself but is
caused by the higher permeability
of
the applied film. Pitch particles dispersed in water
are relatively large and do not coalesce
as
completely after drying
as
the much smaller
dissolved pitch particles do. But coal tar emulsions have other very good features that
will be mentioned later.
The fifth type, coal tar pitch, reinforced with inert fillers and applied in a molten
state over
a
primer, is called in the trade coal tar enamel. These enamels have all the good
qualities of coal tar paints, but in a higher degree, because the coating is very thick and
does not depend on the evaporation
of
solvent to set.
Type
1
is a thin coal tar solution of low viscosity with
a
solids content of 60
to
70% and a spreading rate of 300 to 400 square feet per gallon, gives an approximate
thickness of
1
to
2 mils per coat. This thickness cannot be increased because the thin
solution cannot be applied at a lower rate without sagging. Type 2 is designed to achieve
a heavier coat;
a
filler coal tar solution must be used, which, in addition to its higher
solids content, can be applied at approximately 180 square feet per gallon without sagging.
This produces an approximate dry film thickness
of
6 mils. To apply even heavier coatings
by brush,
a
gel must be selected that can be applied at the low rate of 75 square feet per
gallon without sagging. This will produce
a
dry film thickness of approximately 16 mils
in one coat. Coal tar emulsions will not sag at
a
coverage of 75 square feet per gallon
and will give approximately a 12 mil dry film thickness in one coat.
Coal tar paints afford protection by the mechanical exclusion of moisture and air.
If they are applied as a continuous film without holidays, they give almost perfect protec-
tion. Since it is impossible
to
avoid pinholes and flaws
in
a
one-coat application, more
than one coat will be necessary. They dry by solvent evaporation only.
Concrete,
as
a
rule, can be protected with thin coal tar solutions, but steel requires
heavier coatings that will form
an
almost impervious barrier against severe corrosive
influences.
All coal tar paints “alligator,” more or less, in the sun. The paint will look like an
alligator skin, hence the name alligatoring. This alligatoring is
a
surface defect. It is brought
about by the hardening of the upper layer
of
the film, stimulated by the sun’s rays. This
causes the upper layer to contract. crack and slip over the lower stratum which is still
soft. If not enough coats are applied, these alligator marks can go right down to metal,
opening the path for atmospheric corrosion. Alligatoring does not
(or
only to a limited
degree) occur under water, where the coating is protected from the rays of the sun. Coal