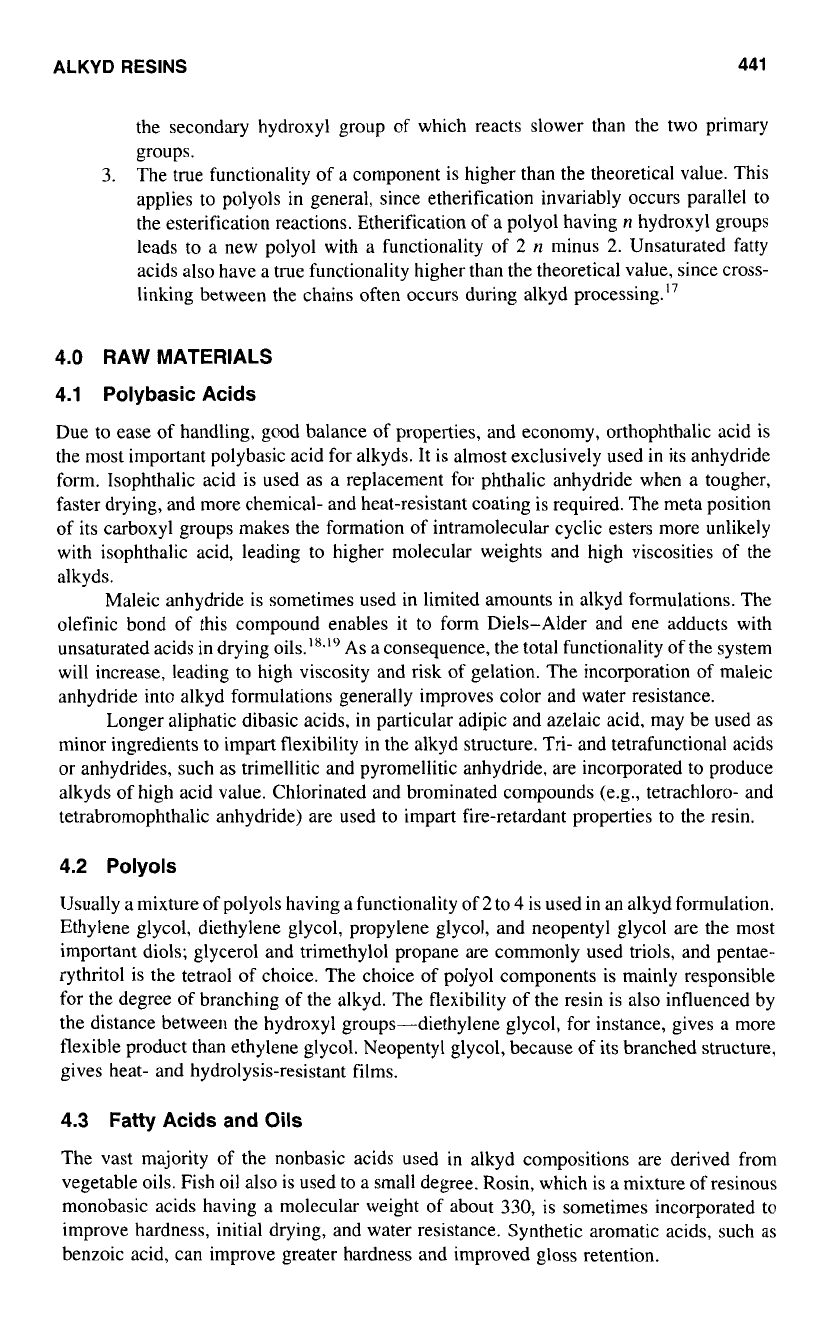
ALKYD
RESINS
441
the secondary hydroxyl group
of
which reacts slower than the two primary
groups.
3.
The true functionality of a component is higher than the theoretical value. This
applies to polyols in general, since etherification invariably occurs parallel to
the esterification reactions. Etherification of a poly01 having
n
hydroxyl groups
leads to a new poly01 with a functionality of
2
n
minus
2.
Unsaturated fatty
acids also have a true functionality higher than the theoretical value, since cross-
linking between the chains often occurs during alkyd processing."
4.0 RAW MATERIALS
4.1
Polybasic Acids
Due to ease of handling, good balance
of
properties, and economy, orthophthalic acid is
the most important polybasic acid for alkyds. It is almost exclusively used in its anhydride
form. Isophthalic acid is used as a replacement for phthalic anhydride when a tougher,
faster drying, and more chemical- and heat-resistant coating is required. The meta position
of
its carboxyl groups makes the formation of intramolecular cyclic esters more unlikely
with isophthalic acid, leading to higher molecular weights and high viscosities of the
alkyds.
Maleic anhydride is sometimes used in limited amounts in alkyd formulations. The
olefinic bond of this compound enables
it
to
form Diels-Alder and ene adducts with
unsaturated acids in drying oils.'8.'"
As
a consequence, the total functionality of the system
will increase, leading
to
high viscosity and risk
of
gelation. The incorporation of maleic
anhydride into alkyd formulations generally improves color and water resistance.
Longer aliphatic dibasic acids, in particular adipic and azelaic acid, may be used as
minor ingredients to impart flexibility in the alkyd structure. Tri- and tetrafunctional acids
or anhydrides, such as trimellitic and pyromellitic anhydride, are incorporated to produce
alkyds of high acid value. Chlorinated and brominated compounds (e.g., tetrachloro- and
tetrabromophthalic anhydride) are used to impart fire-retardant properties to the resin.
4.2
Polyols
Usually a mixture of polyols having a functionality of
2
to
4
is used in an alkyd formulation.
Ethylene glycol, diethylene glycol, propylene glycol, and neopentyl glycol
are
the most
important diols; glycerol and trimethylol propane are commonly used triols, and pentae-
rythritol is the tetraol of choice. The choice of poly01 components is mainly responsible
for the degree of branching of the alkyd. The flexibility of the resin is also influenced by
the distance between the hydroxyl groups-diethylene glycol, for instance, gives a more
flexible product than ethylene glycol. Neopentyl glycol, because
of
its branched structure,
gives heat- and hydrolysis-resistant films.
4.3
Fatty Acids and Oils
The vast majority
of
the nonbasic acids used
in
alkyd compositions are derived from
vegetable oils. Fish oil also is used to a small degree. Rosin, which is a mixture of resinous
monobasic acids having a molecular weight of about
330,
is sometimes incorporated to
improve hardness, initial drying, and water resistance. Synthetic aromatic acids, such as
benzoic acid, can improve greater hardness and improved gloss retention.