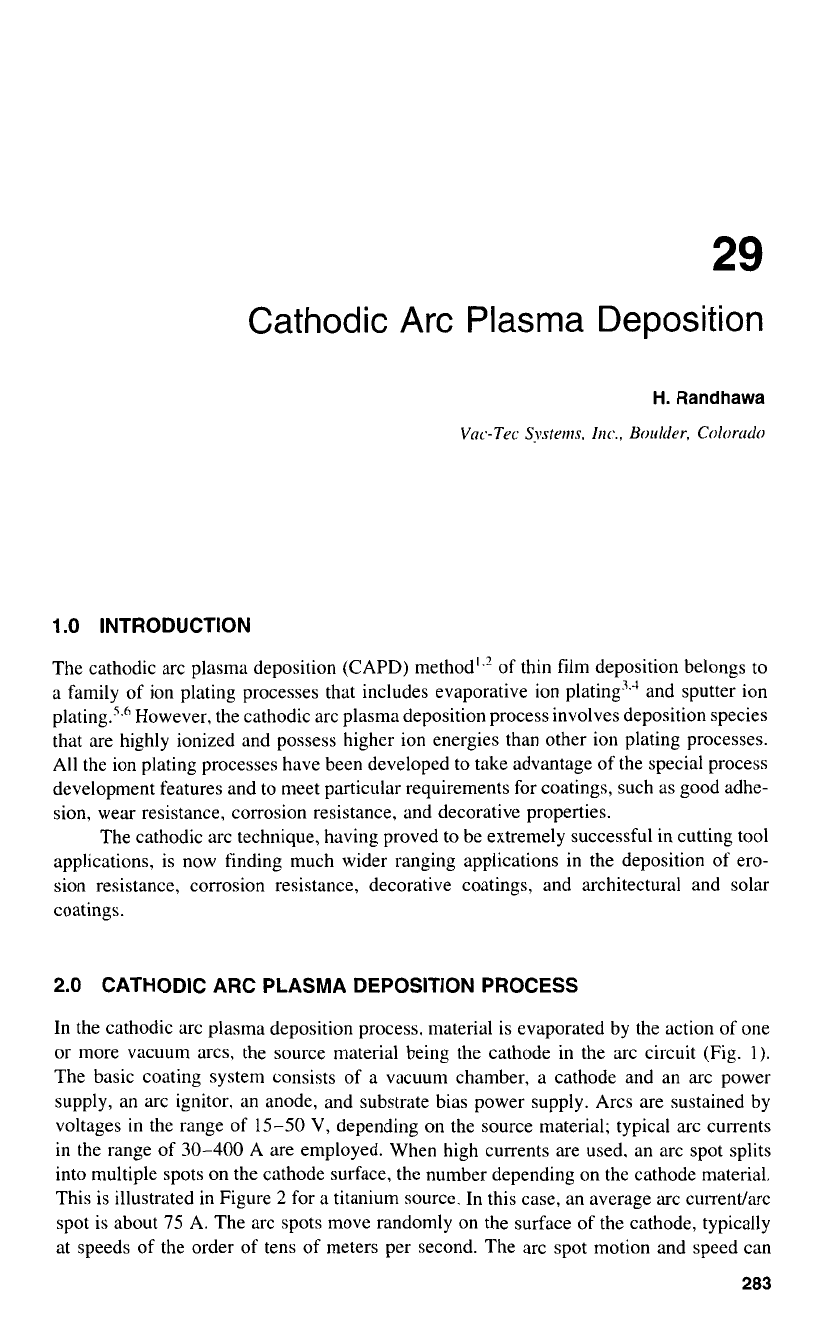
Cathodic Arc Plasma Deposition
1
.O
INTRODUCTION
The cathodic arc plasma deposition (CAPD) method'.' of thin film deposition belongs to
a family
of
ion plating processes that includes evaporative ion plating',4 and sputter ion
plating.5." However, the cathodic arc plasma deposition process involves deposition species
that are highly ionized and possess higher ion energies than other ion plating processes.
All the ion plating processes have been developed
to
take advantage of the special process
development features and to meet particular requirements for coatings, such as good adhe-
sion, wear resistance, corrosion resistance, and decorative properties.
The cathodic arc technique, having proved to be extremely successful in cutting tool
applications, is now finding much wider ranging applications in the deposition
of
ero-
sion resistance, corrosion resistance, decorative coatings, and architectural and solar
coatings.
2.0
CATHODIC ARC PLASMA DEPOSITION PROCESS
In the cathodic arc plasma deposition process, material is evaporated by the action of
one
or more vacuum arcs, the source material being the cathode in the arc circuit (Fig.
1).
The basic coating system consists of a vacuum chamber, a cathode and an arc power
supply, an arc ignitor, an anode, and substrate bias power supply. Arcs are sustained by
voltages
in
the range of
15-50
V,
depending on the source material; typical arc currents
in the range
of
30-400
A are employed. When high currents are used, an arc spot splits
into multiple spots on the cathode surface, the number depending on the cathode material.
This is illustrated in Figure
2
for a titanium source. In this case, an average arc currentkc
spot is about
75
A. The arc spots move randomly
on
the surface of the cathode, typically
at speeds
of
the order of tens
of
meters per second. The arc spot motion and speed can
283