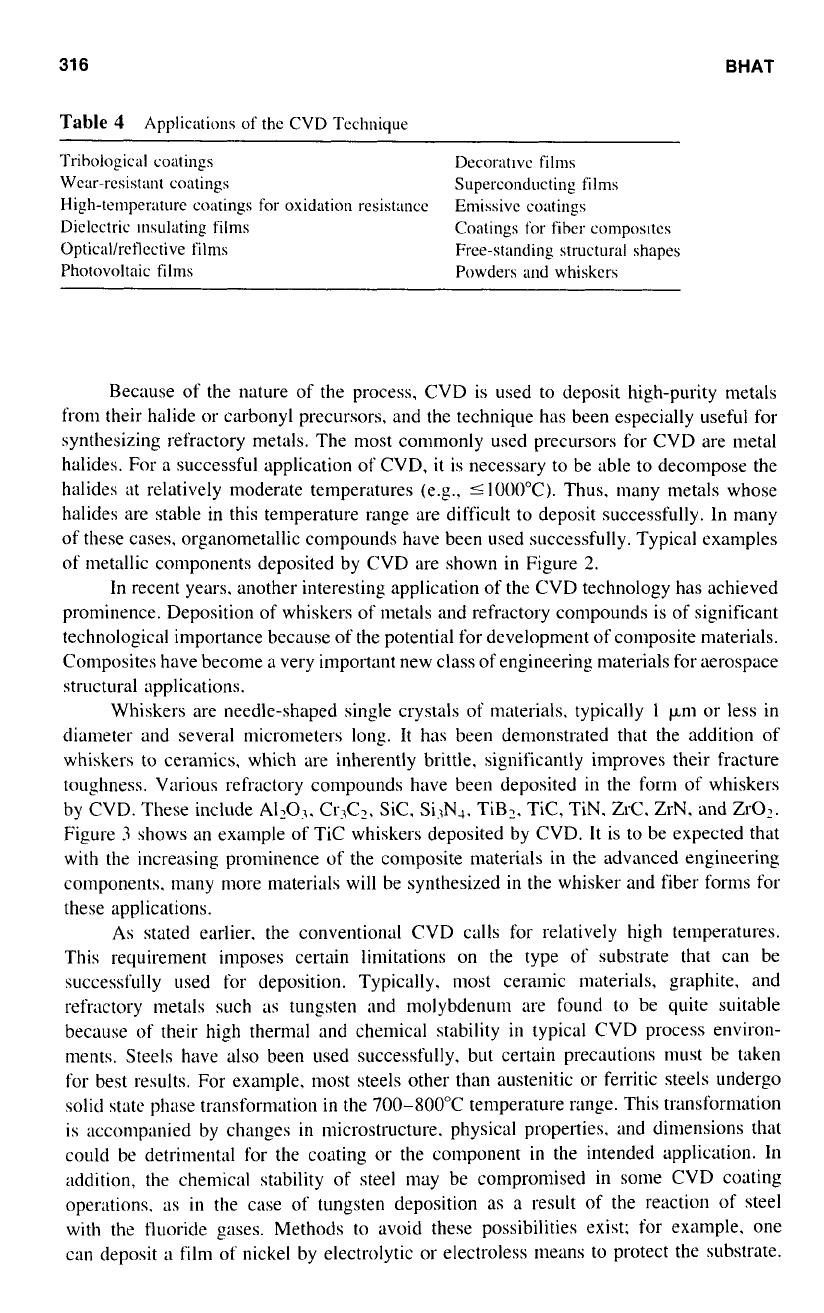
31
6
BHAT
Table
4
Applications of the CVD Technique
Tribological coatings
Decorative films
Wear-resistant coatings
Superconducting films
High-tempernture coatings for oxidation resistance
Emissive coatings
Dielectric tnsulnting films
Coatings for fiber composltcs
Opticnl/rcflective films
Free-standing structural shapes
Photovoltaic films
Powders
and
whiskers
Because of the nature of the process, CVD is used to deposit high-purity metals
from their halide or carbonyl precursors, and the technique has been especially useful for
synthesizing refractory metals. The most commonly used precursors for CVD are metal
halides. For a successful application
of
CVD,
it
is necessary to be able to decompose the
halides at relatively moderate temperatures (e.g.,
5
1000°C). Thus, many metals whose
halides are stable in this temperature range are difficult to deposit successfully. In many
of these cases. organometallic compounds have been used successfully. Typical examples
of metallic components deposited by CVD are shown in Figure
2.
In
recent years, another interesting application
of
the CVD technology has achieved
prominence. Deposition of whiskers of metals and refractory compounds is of significant
technological importance because of the potential for development
of
composite materials.
Composites have become a very inlportant new class
of
engineering materials for aerospace
structural applications.
Whiskers are needle-shaped single crystals of materials, typically
1
pm or less in
diameter and several micrometers long. It has been demonstrated that the addition of
whiskers to ceramics, which are inherently brittle. significantly improves their fracture
toughness. Various refractory compounds have been deposited in the form of whiskers
by CVD. These include
A1203.
Cr3C7. Sic. Si2N4. TiB?. TIC, TIN. ZrC. ZrN. and
Zr02.
Figure
3
shows an example of TIC whiskers deposited by CVD.
It
is to be expected that
with the increasing prominence of the composite materials in the advanced engineering
components. many more materials will be synthesized in the whisker and fiber forms for
these applications.
As
stated earlier. the conventional CVD calls for relatively high temperatures.
This requirement imposes certain limitations on the type of substrate that can be
successfully used for deposition. Typically. most ceramic materials, graphite. and
refractory metals such
as
tungsten and molybdenum are found to be quite suitable
because of their high thermal and chemical stability
in
typical CVD process environ-
ments. Steels have also been used successfully, but certain precautions must be taken
for best results. For example, most steels other than austenitic or ferritic steels undergo
soli(I stllte phase transformation
in
the 700-800°C temperature range. This transformation
is ;iccon1p;inied by changes
in
microstructure. physical properties. and dimensions
that
COLI^^
be detrimental for the coating or the component
in
the intended application.
h
addition, the chemical stability of steel may be compromised in some CVD coating
operations.
as
in
the case
of
tungsten deposition as a result of the reaction
of
steel
wit11 the tluoride gases. Methods to avoid these possibilities exist; for example. one
can deposit
a
film
of
nickel by electrolytic or electroless means to protect the substrate.