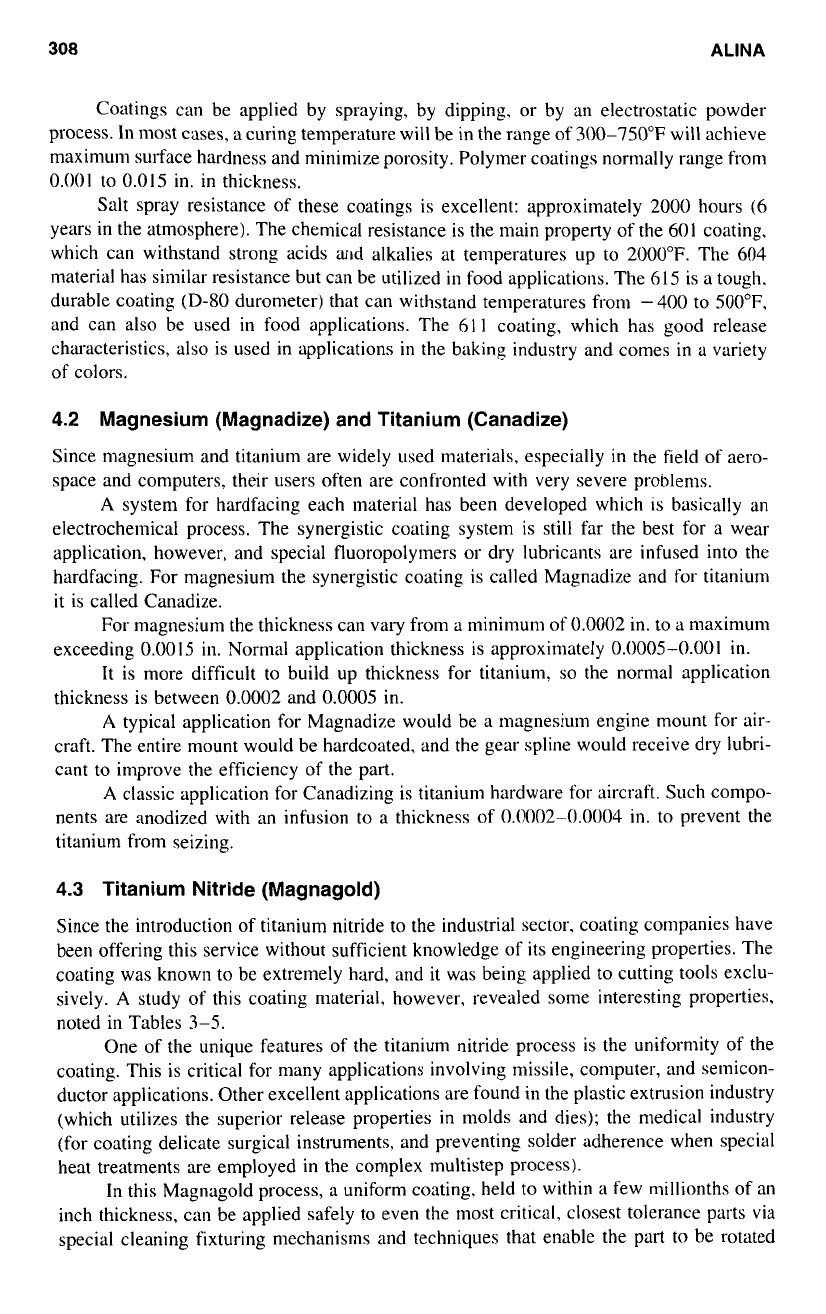
308
ALINA
Coatings can be applied by spraying, by dipping. or by an electrostatic powder
process.
In
most cases, a curing temperature will be in the range of 300-750°F will achieve
maximum surface hardness and minimize porosity. Polymer coatings normally range from
0.001
to
0.015 in.
in
thickness.
Salt spray resistance
of
these coatings is excellent: approximately 2000 hours (6
years in the atmosphere). The chemical resistance is the main property of the 60
1
coating.
which can withstand strong acids and alkalies at temperatures up
to
2000°F. The 604
material has similar resistance but can be utilized
in
food applications. The 615 is a tough.
durable coating
(D-80
durometer) that can withstand temperatures from -400 to 500°F.
and can also be used
in
food applications. The 61
1
coating, which has good release
characteristics, also is used in applications
in
the baking industry and comes in a variety
of
colors.
4.2
Magnesium (Magnadize) and Titanium (Canadize)
Since magnesium and titanium are widely used materials, especially in the field of aero-
space and computers, their users often are confronted with very severe problems.
A
system for hardfacing each material has been developed which is basically an
electrochemical process. The synergistic coating system is still far the best for a wear
application, however, and special fluoropolymers or dry lubricants are infused into the
hardfacing.
For
magnesium the synergistic coating is called Magnadize and for titanium
it is called Canadize.
For magnesium the thickness can vary from a minimum of 0.0002 in.
to
a maximum
exceeding
0.00
15
in. Normal application thickness is approximately 0.0005-0.00
I
in.
It
is more difficult to build up thickness for titanium,
so
the normal application
thickness is between 0.0002 and
0.0005
in.
A
typical application for Magnadize would be a magnesium engine mount for air-
craft. The entire mount would be hardcoated, and the gear spline would receive dry lubri-
cant to improve the efficiency of the part.
A
classic application for Canadizing is titanium hardware for aircraft. Such compo-
nents are anodized with an infusion
to
a thickness
of
0.0002-0.0004 in. to prevent the
titanium from seizing.
4.3
Titanium Nitride (Magnagold)
Since the introduction of titanium nitride to the industrial sector. coating companies have
been offering this service without sufficient knowledge of its engineering properties. The
coating was known
to
be extremely hard, and it was being applied to cutting
tools
exclu-
sively.
A
study of this coating material, however, revealed some interesting properties,
noted in Tables
3-5.
One of the unique features of the titanium nitride process is the uniformity
of
the
coating. This is critical for many applications involving missile, computer, and semicon-
ductor applications. Other excellent applications are found in the plastic extrusion industry
(which utilizes the superior release properties in molds and dies); the medical industry
(for coating delicate surgical instruments, and preventing solder adherence when special
heat treatments are employed in the complex multistep process).
In
this Magnagold process, a uniform coating. held
to
within a few millionths
of
an
inch thickness, can be applied safely to even the most critical, closest tolerance parts via
special cleaning fixturing mechanisms and techniques that enable the part
to
be rotated