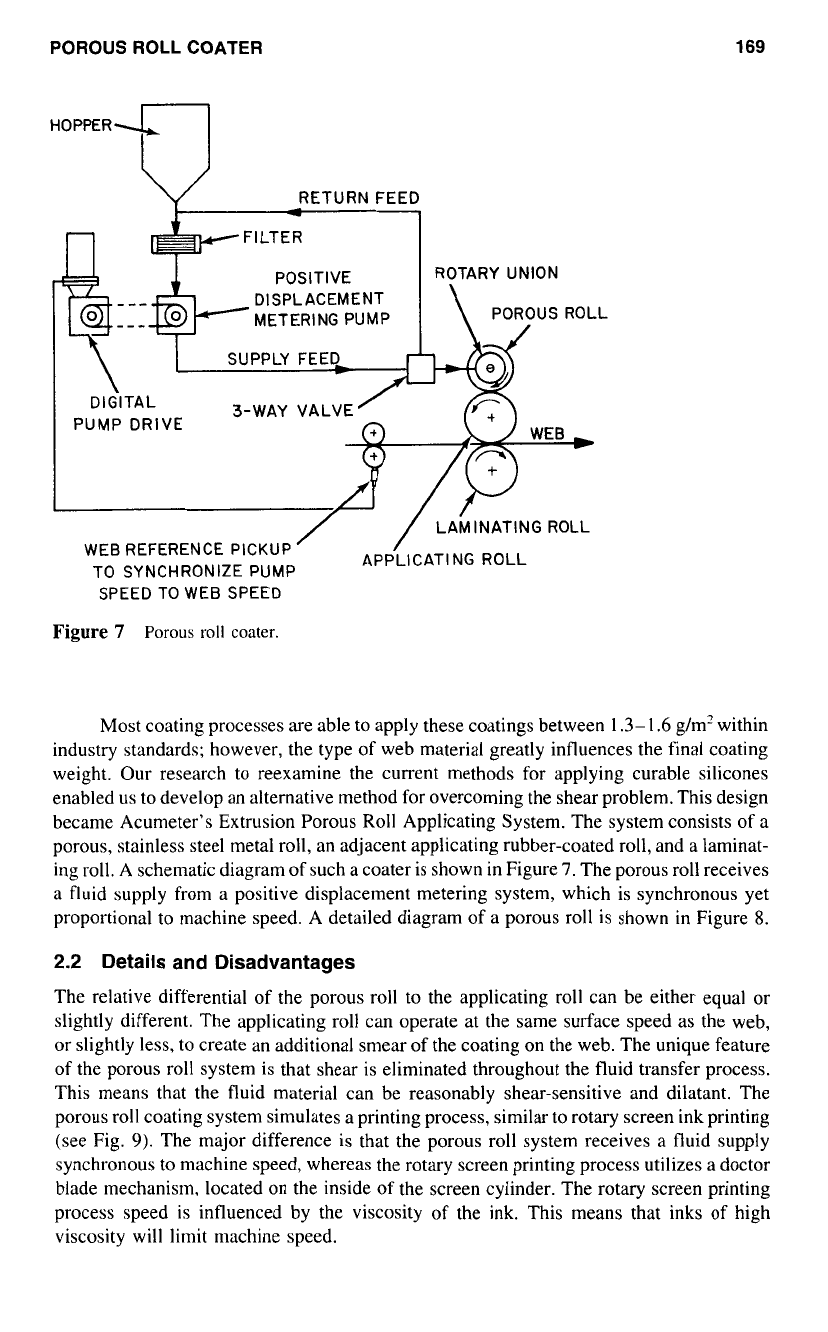
POROUS
ROLL COATER
169
RETURNFEED
l
POSITIVE ROTARY UNION
DISPLACEMENT
METERING PUMP
DIGITAL
PUMP DRIVE
3-WAY VALVE
/
/
LAMINATING
ROLL
WEB REFERENCE PICKUP
TO SYNCHRONIZE PUMP
APPLlCATl NG ROLL
SPEED TO WEB SPEED
Figure
7
Porous
roll
coater.
Most coating processes are able to apply these coatings between
1.3-1.6
g/m’ within
industry standards; however, the type
of
web material greatly influences the final coating
weight. Our research to reexamine the current methods for applying curable silicones
enabled us to develop an alternative method for overcoming the shear problem. This design
became Acumeter’s Extrusion Porous
Roll
Applicating System. The system consists of a
porous, stainless steel metal roll, an adjacent applicating rubber-coated roll, and
a
laminat-
ing roll. A schematic diagram of such
a
coater is shown in Figure
7.
The porous roll receives
a
fluid supply from
a
positive displacement metering system, which is synchronous yet
proportional to machine speed. A detailed diagram of a porous roll is shown in Figure
8.
2.2
Details and Disadvantages
The relative differential of the porous roll to the applicating roll can be either equal or
slightly different. The applicating roll can operate at the same surface speed
as
the web,
or
slightly less, to create an additional smear of the coating on the web. The unique feature
of the porous roll system is that shear is eliminated throughout the fluid transfer process.
This means that the fluid material can be reasonably shear-sensitive and dilatant. The
porous roll coating system simulates
a
printing process, similar to rotary screen ink printing
(see Fig.
9).
The major difference is that the porous roll system receives
a
fluid supply
synchronous to machine speed, whereas the rotary screen printing process utilizes
a
doctor
blade mechanism, located on the inside of the screen cylinder. The rotary screen printing
process speed is influenced by the viscosity
of
the ink. This means that inks of high
viscosity will limit machine speed.