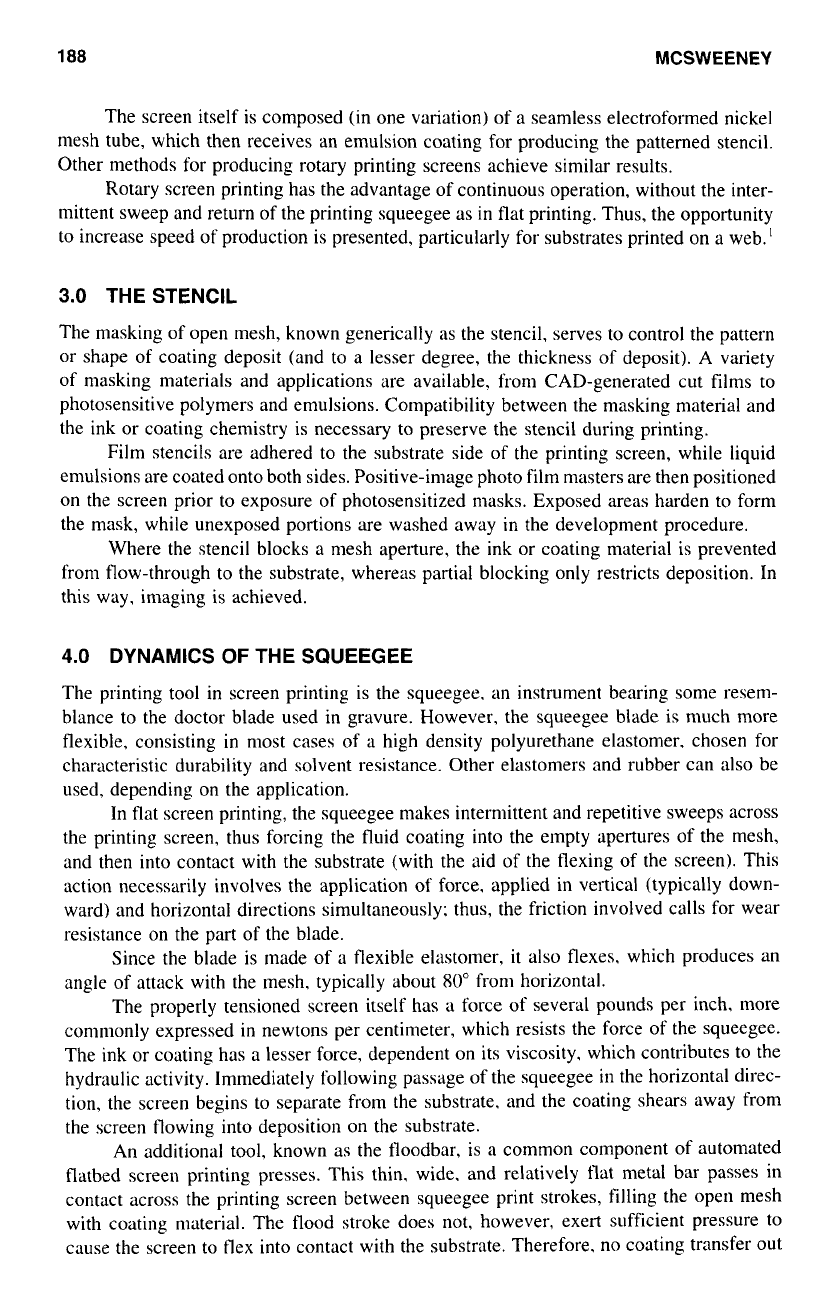
188
MCSWEENEY
The screen itself is composed (in one variation) of a seamless electroformed nickel
mesh tube, which then receives an emulsion coating for producing the patterned stencil.
Other methods for producing rotary printing screens achieve similar results.
Rotary screen printing has the advantage of continuous operation, without the inter-
mittent sweep and return of the printing squeegee as
in
flat printing. Thus, the opportunity
to
increase speed of production is presented, particularly for substrates printed on a web.'
3.0
THE STENCIL
The masking of open mesh, known generically
as
the stencil, serves to control the pattern
or shape
of
coating deposit (and
to
a lesser degree, the thickness of deposit). A variety
of masking materials and applications are available. from CAD-generated cut films to
photosensitive polymers and emulsions. Compatibility between the masking material and
the ink or coating chemistry is necessary to preserve the stencil during printing.
Film stencils are adhered to the substrate side of the printing screen, while liquid
emulsions are coated onto both sides. Positive-image photo
film
masters are then positioned
on
the screen prior
to
exposure of photosensitized masks. Exposed areas harden to form
the mask, while unexposed portions are washed away in the development procedure.
Where the stencil blocks a mesh aperture, the ink or coating material is prevented
from tlow-through
to
the substrate, whereas partial blocking only restricts deposition. In
this way, imaging is achieved.
4.0
DYNAMICS
OF
THE SQUEEGEE
The printing tool in screen printing is the squeegee. an instrument bearing some resem-
blance to the doctor blade used in gravure. However, the squeegee blade is much more
flexible, consisting
in
most cases
of
a
high density polyurethane elastomer, chosen for
characteristic durability and solvent resistance. Other elastomers and rubber can
also
be
used, depending on the application.
In flat screen printing, the squeegee makes intermittent and repetitive sweeps across
the printing screen, thus forcing the fluid coating into the empty apertures of the mesh,
and then into contact with the substrate (with the aid of the flexing
of
the screen). This
action necessarily involves the application
of
force. applied in vertical (typically down-
ward) and horizontal directions simultaneously; thus, the friction involved calls for wear
resistance on the part
of
the blade.
Since the blade is made of a flexible elastomer,
it
also flexes. which produces an
angle of attack with the mesh, typically about
80"
from horizontal.
The properly tensioned screen itself has
a
force of several pounds per inch, more
commonly expressed in newtons per centimeter, which resists the force of the squeegee.
The ink or coating has a lesser force, dependent
on
its viscosity, which contributes to the
hydraulic activity. Immediately following passage of the squeegee
in
the horizontal direc-
tion. the screen begins to separate from the substrate. and the coating shears away from
the screen flowing into deposition on the substrate.
An additional tool, known as the tloodbar, is a common component of automated
flatbed screen printing presses. This thin, wide. and relatively flat metal bar passes in
contact across the printing screen between squeegee print strokes, filling the open mesh
with coating material. The flood stroke does not, however, exert sufficient pressure to
cause the screen to flex
into
contact with the substrate. Therefore, no coating transfer out