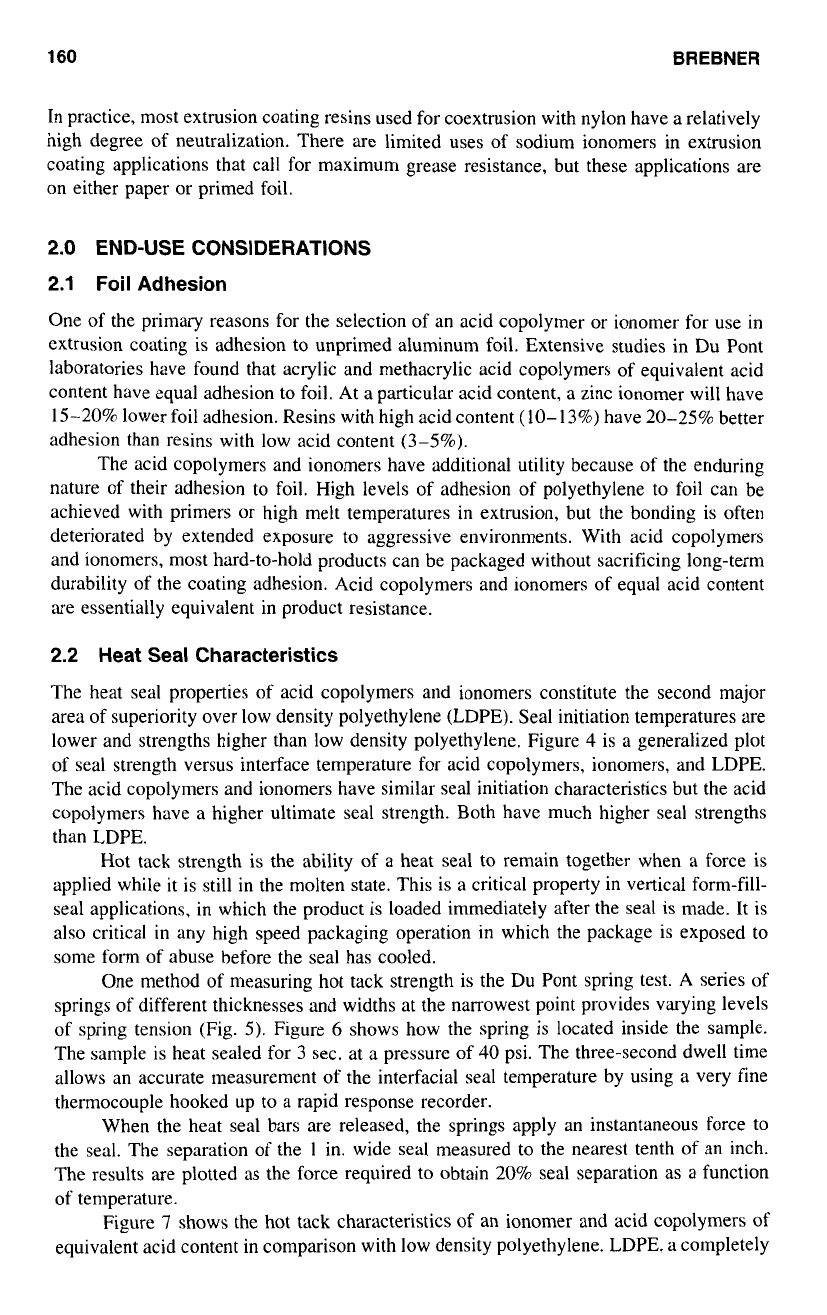
160
BREBNER
In practice, most extrusion coating resins used for coextrusion with nylon have a relatively
high degree
of
neutralization. There are limited uses of sodium ionomers in extrusion
coating applications that call for maximum grease resistance, but these applications are
on either paper or primed foil.
2.0
END-USE CONSIDERATIONS
2.1
Foil Adhesion
One
of
the primary reasons for the selection of an acid copolymer or ionomer for use in
extrusion coating is adhesion to unprimed aluminum foil. Extensive studies in Du Pont
laboratories have found that aclylic and methacrylic acid copolymers of equivalent acid
content have equal adhesion to foil. At a particular acid content,
a
zinc ionomer will have
15-20% lower foil adhesion. Resins with high acid content
(10-
13%)
have
20-25%
better
adhesion than resins with low acid content
(3-5%).
The acid copolymers and ionomers have additional utility because of the enduring
nature of their adhesion to foil. High levels of adhesion of polyethylene to foil can be
achieved with primers or high melt temperatures in extrusion, but the bonding is often
deteriorated by extended exposure
to
aggressive environments. With acid copolymers
and ionomers, most hard-to-hold products can be packaged without sacrificing long-term
durability of the coating adhesion. Acid copolymers and ionomers of equal acid content
are essentially equivalent in product resistance.
2.2 Heat Seal Characteristics
The heat seal properties of acid copolymers and ionomers constitute the second major
area of superiority over low density polyethylene (LDPE). Seal initiation temperatures are
lower and strengths higher than low density polyethylene. Figure 4 is a generalized plot
of seal strength versus interface temperature for acid copolymers, ionomers, and LDPE.
The acid copolymers and ionomers have similar seal initiation characteristics but the acid
copolymers have a higher ultimate seal strength. Both have much higher seal strengths
than LDPE.
Hot tack strength is the ability of a heat seal to remain together when a force is
applied while it is still in the molten state. This is
a
critical property in vertical form-fill-
seal applications, in which the product is loaded immediately after the seal is made. It is
also
critical
in
any high speed packaging operation in which the package is exposed to
some form of abuse before the seal has cooled.
One method of measuring hot tack strength
is
the Du Pont spring test. A series
of
springs of different thicknesses and widths at the narrowest point provides varying levels
of spring tension (Fig.
5).
Figure
6
shows how the spring is located inside the sample.
The sample is heat sealed for
3
sec. at a pressure of 40 psi. The three-second dwell time
allows an accurate measurement of the interfacial seal temperature by using a very fine
thermocouple hooked up
to
a rapid response recorder.
When the heat seal bars are released, the springs apply an instantaneous force to
the seal. The separation of the
1
in. wide seal measured to the nearest tenth of an inch.
The results are plotted as the force required to obtain 20% seal separation
as
a function
of temperature.
Figure
7
shows the hot tack characteristics
of
an ionomer and acid copolymers
of
equivalent acid content in comparison with low density polyethylene. LDPE, a completely