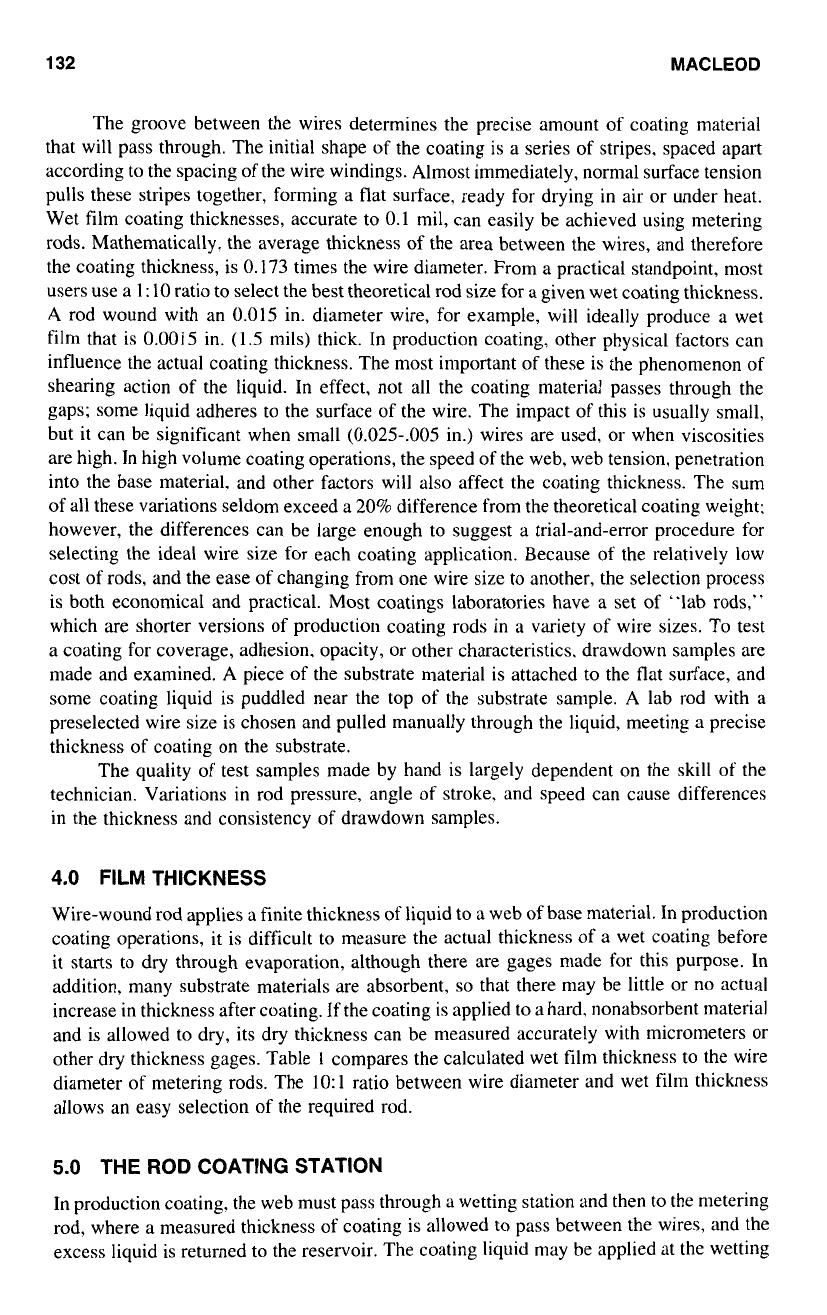
132
MACLEOD
The groove between the wires determines the precise amount of coating material
that will pass through. The initial shape of the coating is a series of stripes, spaced apart
according to the spacing of the wire windings. Almost immediately, normal surface tension
pulls these stripes together, forming
a
flat surface, ready for drying in air or under heat.
Wet film coating thicknesses, accurate to 0.1 mil, can easily be achieved using metering
rods. Mathematically, the average thickness of the area between the wires, and therefore
the coating thickness, is
0.173
times the wire diameter. From a practical standpoint, most
users use a
1
:
10
ratio to select the best theoretical rod size for
a
given wet coating thickness.
A rod wound with an
0.015
in. diameter wire, for example, will ideally produce a wet
film that is
0.0015
in. (1.5 mils) thick.
In
production coating, other physical factors can
influence the actual coating thickness. The most important of these is the phenomenon of
shearing action
of
the liquid. In effect, not all the coating material passes through the
gaps; some liquid adheres to the surface of the wire. The impact of this is usually small,
but it can be significant when small (0.025-.005 in.) wires are used, or when viscosities
are high. In high volume coating operations, the speed of the web, web tension, penetration
into the base material. and other factors will also affect the coating thickness. The sum
of
all these variations seldom exceed
a
20%
difference from the theoretical coating weight;
however, the differences can be large enough to suggest a trial-and-error procedure for
selecting the ideal wire size for each coating application. Because of the relatively low
cost of rods, and the ease
of
changing from one wire size to another, the selection process
is both economical and practical. Most coatings laboratories have a set
of
“lab rods,”
which are shorter versions of production coating rods in a variety
of
wire sizes. To test
a coating for coverage, adhesion. opacity, or other characteristics. drawdown samples are
made and examined.
A
piece of the substrate material is attached to the flat surface, and
some coating liquid is puddled near the top of the substrate sample. A lab rod with a
preselected wire size is chosen and pulled manually through the liquid, meeting a precise
thickness of coating on the substrate.
The quality of test samples made by hand is largely dependent on the skill of the
technician. Variations in rod pressure, angle of stroke, and speed can cause differences
in the thickness and consistency of drawdown samples.
4.0
FILM
THICKNESS
Wire-wound rod applies a finite thickness of liquid to
a
web of base material. In production
coating operations, it is difficult
to
measure the actual thickness of a wet coating before
it starts to dry through evaporation, although there are gages made for this purpose. In
addition, many substrate materials are absorbent,
so
that there may be little or no actual
increase in thickness after coating. If the coating is applied
to
a
hard, nonabsorbent material
and is allowed
to
dry, its dry thickness can be measured accurately with micrometers or
other dry thickness gages. Table
1
compares the calculated wet film thickness to the wire
diameter of metering rods. The
1O:l
ratio between wire diameter and wet film thickness
allows an easy selection of the required rod.
5.0
THE
ROD
COATING STATION
In production coating. the web must pass through a wetting station and then
to
the metering
rod, where a measured thickness
of
coating is allowed to pass between the wires, and the
excess liquid is returned to the reservoir. The coating liquid may be applied at the wetting