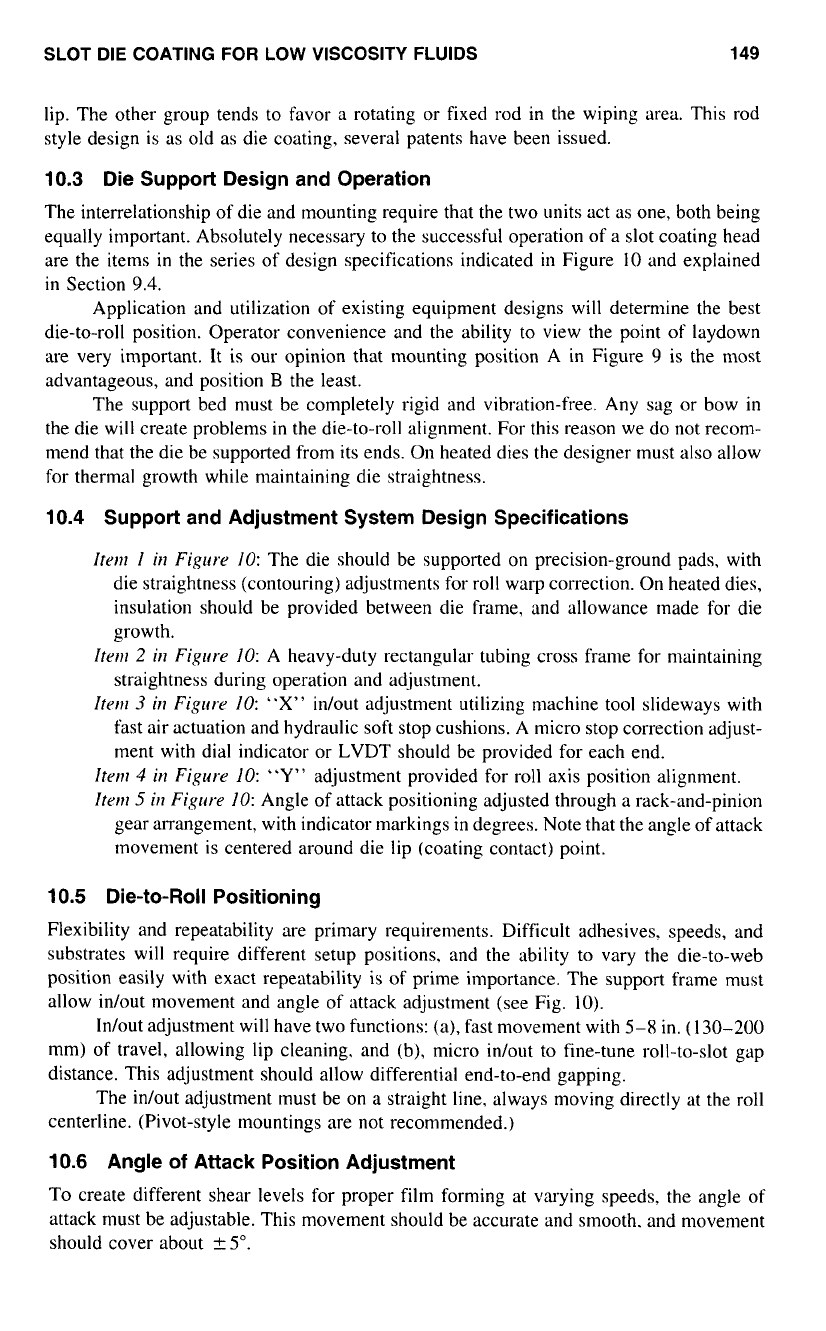
SLOT DIE
COATING FOR
LOW
VISCOSITY
FLUIDS
149
lip. The other group tends to favor a rotating or fixed rod in the wiping area. This rod
style design is as old as die coating, several patents have been issued.
10.3
Die Support Design and Operation
The interrelationship of die and mounting require that the two units act as one, both being
equally important. Absolutely necessary to the successful operation of a slot coating head
are the items
in
the series of design specifications indicated
in
Figure
10
and explained
in
Section
9.4.
Application and utilization of existing equipment designs will determine the best
die-to-roll position. Operator convenience and the ability
to
view the point
of
laydown
are very important. It is our opinion that mounting position A in Figure
9
is the most
advantageous, and position
B
the least.
The support bed must be completely rigid and vibration-free. Any sag or bow in
the die will create problems
in
the die-to-roll alignment. For this reason we do not recom-
mend that the die be supported from its ends.
On
heated dies the designer must also allow
for thermal growth while maintaining die straightness.
10.4
Support and Adjustment System Design Specifications
Iter11
I
in Figure
10:
The die should be supported on precision-ground pads, with
die straightness (contouring) adjustments for roll warp correction. On heated dies,
insulation should be provided between die frame, and allowance made for die
growth.
Iten1
2
in
Figure
10:
A heavy-duty rectangular tubing cross frame for maintaining
straightness during operation and adjustment.
Itel71
3
in
Figure
IO:
“X”
in/out adjustment utilizing machine tool slideways with
fast air actuation and hydraulic soft stop cushions. A micro stop correction adjust-
ment with dial indicator or LVDT should be provided for each end.
Iter71
4
irz
Figure
IO:
“Y”
adjustment provided for roll axis position alignment.
Iter11
5
it1
Fi,qure
10:
Angle of attack positioning adjusted through a rack-and-pinion
gear arrangement, with indicator markings
in
degrees. Note that the angle of attack
movement is centered around die lip (coating contact) point.
10.5
Die-to-Roll Positioning
Flexibility and repeatability are primary requirements. Difficult adhesives. speeds, and
substrates will require different setup positions, and the ability to vary the die-to-web
position easily with exact repeatability is
of
prime importance. The support frame must
allow in/out movement and angle of attack adjustment (see Fig.
10).
In/out adjustment will have two functions: (a), fast movement with
5-8
in.
(130-200
mm) of travel, allowing lip cleaning, and (b), micro in/out to fine-tune roll-to-slot gap
distance. This adjustment should allow differential end-to-end gapping.
The in/out adjustment must be on a straight line, always moving directly at the roll
centerline. (Pivot-style mountings are not recommended.)
10.6
Angle of Attack Position Adjustment
To
create different shear levels for proper film forming at varying speeds, the angle of
attack must be adjustable. This movement should be accurate and smooth. and movement
should cover about
+-
5”.