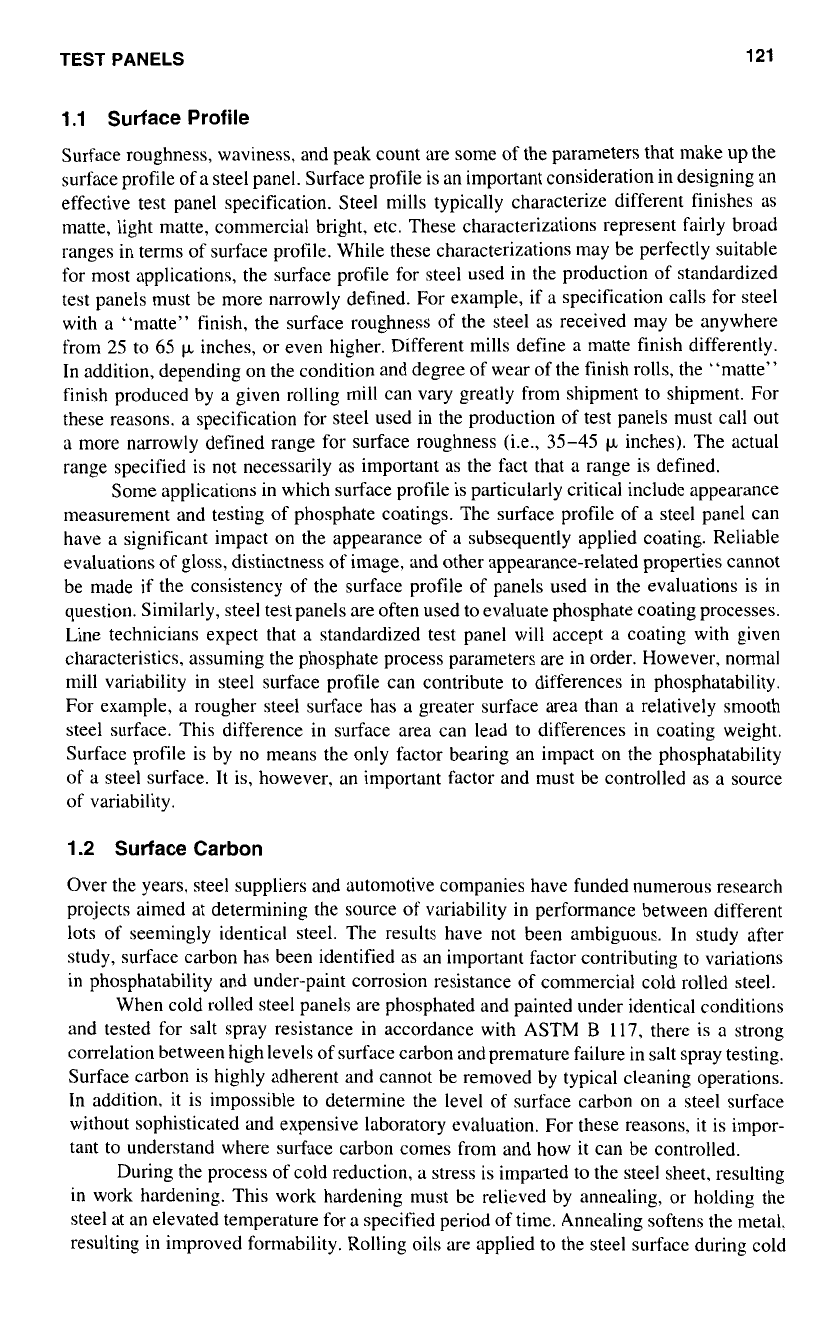
TEST PANELS
121
1.1
Surface Profile
Surface roughness, waviness, and peak count are some of the parameters that make up the
surface profile of a steel panel. Surface profile is an important consideration in designing an
effective test panel specification. Steel mills typically characterize different finishes as
matte, light matte, commercial bright, etc. These characterizations represent fairly broad
ranges in terms of surface protjle. While these characterizations may be perfectly suitable
for most applications, the surface profile for steel used in the production of standardized
test panels must be more narrowly defined.
For
example, if a specification calls for steel
with a “matte” finish, the surface roughness of the steel as received may be anywhere
from
25
to
65
p.
inches, or even higher. Different mills define a matte finish differently.
In addition, depending on the condition and degree of wear of the finish rolls, the “matte”
finish produced by a given rolling mill can vary greatly from shipment to shipment. For
these reasons, a specification for steel used in the production of test panels must call out
a more narrowly defined range for surface roughness (i.e.,
35-45
inches). The actual
range specified is not necessarily as important as the fact that a range is defined.
Some applications in which surface profile is particularly critical include appearance
measurement and testing of phosphate coatings. The surface profile of a steel panel can
have a significant impact on the appearance of a subsequently applied coating. Reliable
evaluations
of
gloss, distinctness
of
image, and other appearance-related properties cannot
be made if the consistency of the surface profile
of
panels used in the evaluations is in
question. Similarly, steel test panels are often used to evaluate phosphate coating processes.
Line technicians expect that a standardized test panel will accept a coating with given
characteristics, assuming the phosphate process parameters are in order. However, normal
mill variability in steel surface profile can contribute to differences in phosphatability.
For example, a rougher steel surface has a greater surface area than a relatively smooth
steel surface. This difference in surface area can lead to differences in coating weight.
Surface profile is by no means the only factor bearing an impact on the phosphatability
of a steel surface. It is, however, an important factor and must be controlled as a Source
of variability.
1.2
Surface Carbon
Over the years, steel suppliers and automotive companies have funded numerous research
projects aimed at determining the source
of
variability in performance between different
lots of seemingly identical steel. The results have
not
been ambiguous. In study after
study, surface carbon has been identified as an important factor contributing
to
variations
in phosphatability and under-paint corrosion resistance
of
commercial cold rolled steel.
When cold rolled steel panels are phosphated and painted under identical conditions
and tested for salt spray resistance
in
accordance with ASTM
B
117, there is a strong
correlation between high levels
of
surface carbon and premature failure in salt spray testing.
Surface carbon is highly adherent and cannot be removed by typical cleaning operations.
In addition. it is impossible to determine the level
of
surface carbon on a steel surface
without sophisticated and expensive laboratory evaluation. For these reasons, it is impor-
tant
to
understand where surface carbon comes from and how it can be controlled.
During the process of cold reduction, a stress is imparted to the steel sheet. resulting
in work hardening. This work hardening must be relieved by annealing, or holding the
steel at an elevated temperature for a specified period of time. Annealing softens the metal,
resulting
in
improved formability. Rolling oils are applied to the steel surface during cold