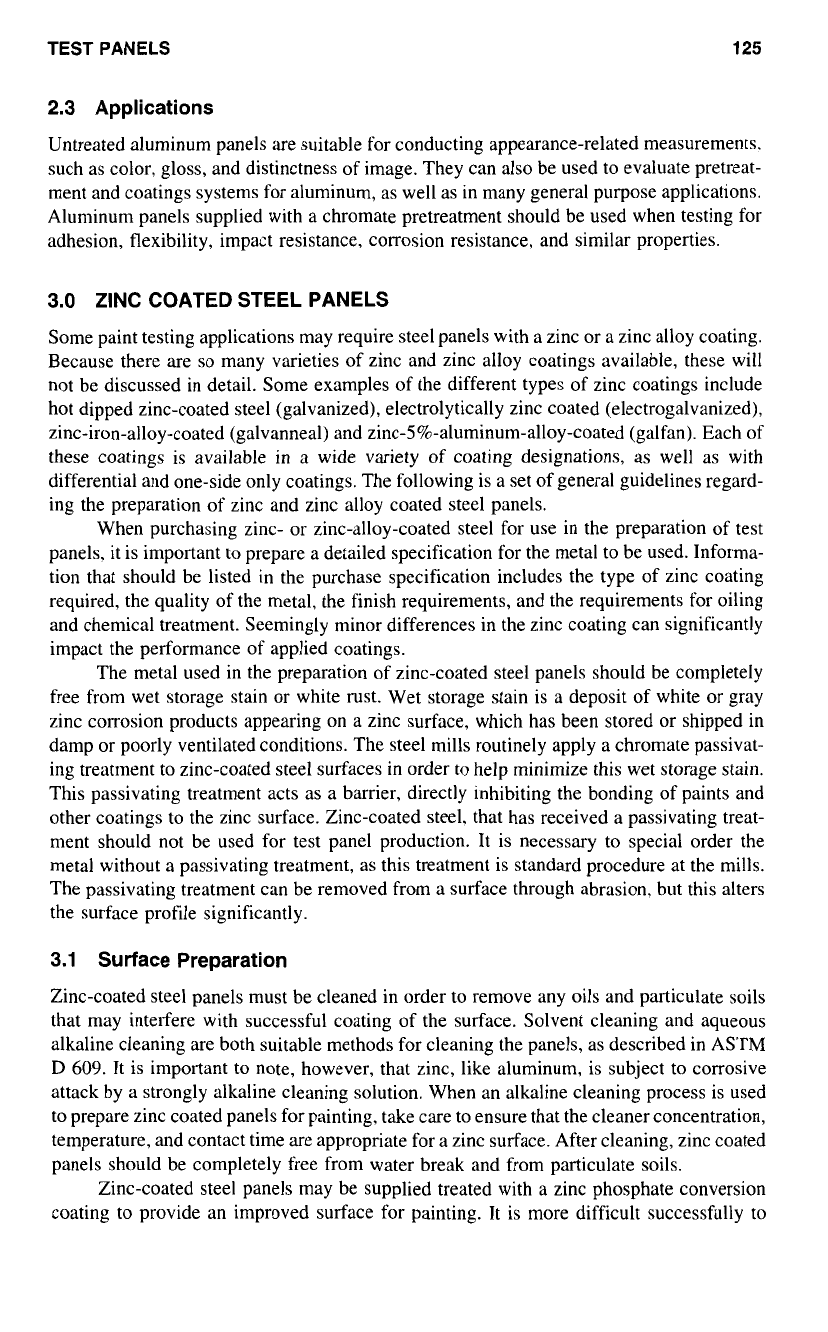
TEST
PANELS
125
2.3
Applications
Untreated aluminum panels are suitable for conducting appearance-related measurements.
such as color,
gloss,
and distinctness of image. They can also be used to evaluate pretreat-
ment and coatings systems for aluminum,
as
well as in many general purpose applications.
Aluminum panels supplied with a chromate pretreatment should be used when testing for
adhesion, flexibility, impact resistance, corrosion resistance, and similar properties.
3.0
ZINC COATED STEEL PANELS
Some paint testing applications may require steel panels with a zinc or a zinc alloy coating.
Because there are
so
many varieties of zinc and zinc alloy coatings available, these will
not be discussed
in
detail. Some examples
of
the different types of zinc coatings include
hot dipped zinc-coated steel (galvanized), electrolytically zinc coated (electrogalvanized),
zinc-iron-alloy-coated (galvanneal) and
zinc-5%-aluminum-alloy-coated
(galfan). Each of
these coatings is available
in
a wide variety
of
coating designations, as well as with
differential and one-side only coatings. The following is a set of general guidelines regard-
ing the preparation of zinc and zinc alloy coated steel panels.
When purchasing zinc- or zinc-alloy-coated steel for use in the preparation
of
test
panels. it is important
to
prepare a detailed specification for the metal to be used. Informa-
tion that should be listed
in
the purchase specification includes the type of zinc coating
required, the quality of the metal, the finish requirements, and the requirements for oiling
and chemical treatment. Seemingly minor differences in the zinc coating can significantly
impact the performance of applied coatings.
The metal used in the preparation of zinc-coated steel panels should be completely
free from wet storage stain or white rust. Wet storage stain is a deposit of white or gray
zinc corrosion products appearing on a zinc surface, which has been stored or shipped in
damp or poorly ventilated conditions. The steel mills routinely apply a chromate passivat-
ing treatment to zinc-coated steel surfaces
in
order
to
help minimize this wet storage stain.
This passivating treatment acts
as
a barrier, directly inhibiting the bonding of paints and
other coatings to the zinc surface. Zinc-coated steel. that has received a passivating treat-
ment should not be used for test panel production. It is necessary to special order the
metal without a passivating treatment, as this treatment is standard procedure at the mills.
The passivating treatment can be removed from a surface through abrasion, but this alters
the surface profile significantly.
3.1
Surface Preparation
Zinc-coated steel panels must be cleaned in order to remove any oils and particulate soils
that may interfere with successful coating of the surface. Solvent cleaning and aqueous
alkaline cleaning are both suitable methods for cleaning the panels, as described in ASTM
D
609.
It is important to note, however, that zinc, like aluminum, is subject to corrosive
attack by a strongly alkaline cleaning solution. When an alkaline cleaning process is used
to
prepare zinc coated panels for painting, take care to ensure that the cleaner concentration,
temperature, and contact time are appropriate for a zinc surface. After cleaning, zinc coated
panels should be completely free from water break and from particulate soils.
Zinc-coated steel panels may be supplied treated with a zinc phosphate conversion
coating
to
provide an improved surface for painting. It is more difficult successfully
to