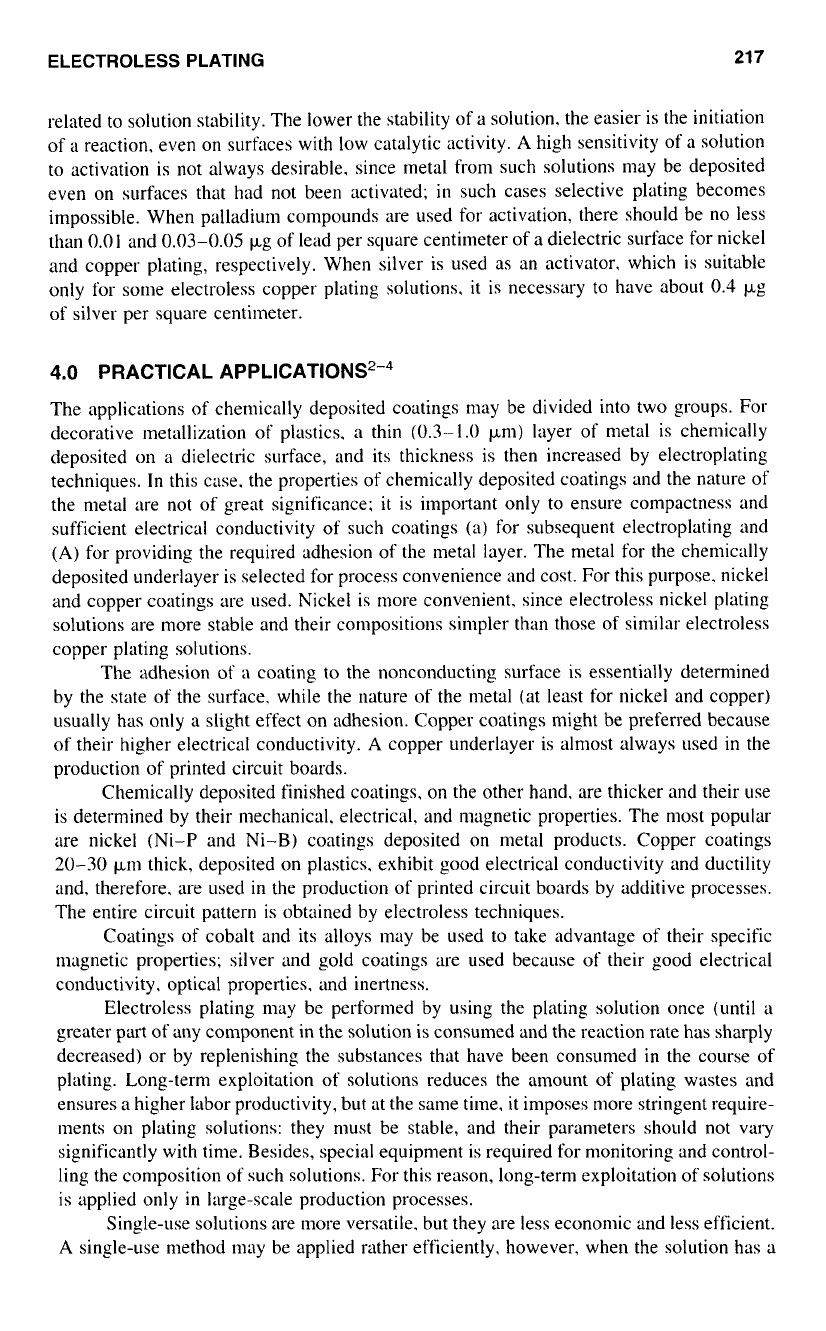
ELECTROLESS PLATING
21
7
related to solution stability. The lower the stability of a solution. the easier is the initiation
of a reaction, even on surfaces with low catalytic activity.
A
high sensitivity of a solution
to activation is not always desirable. since metal from such solutions may be deposited
even on surfaces that had not been activated;
in
such cases selective plating becomes
impossible. When palladium compounds are used for activation, there should be
no
less
than
0.01
and 0.03-0.05 Kg of lead per square centimeter of a dielectric surface for nickel
and copper plating, respectively. When silver is used as an activator, which is suitable
only
for some electroless copper plating solutions.
it
is necessary to have about
0.4
pg
of silver per square centimeter.
4.0
PRACTICAL
The applications of chemically deposited coatings may be divided into two groups. For
decorative metallization of plastics, a thin
(0.3-1
.O
km) layer of metal is chemically
deposited
on
a
dielectric surface, and its thickness is then increased by electroplating
techniques.
In
this case. the properties of chemically deposited coatings and the nature of
the metal are not of great significance;
it
is important
only
to ensure compactness and
sufficient electrical conductivity
of
such coatings
(a)
for subsequent electroplating and
(A)
for providing the required adhesion of the metal layer. The metal for the chemically
deposited underlayer is selected for process convenience and cost. For this purpose. nickel
and copper coatings are used. Nickel is more convenient. since electroless nickel plating
solutions are more stable and their compositions simpler than those
of
similar electroless
copper plating solutions.
The adhesion
of
a
coating to the nonconducting surface is essentially determined
by the state of the surface. while the nature of the metal (at least for nickel and copper)
usually has only a slight effect on adhesion. Copper coatings might be preferred because
of
their higher electrical conductivity.
A
copper underlayer is almost always used in the
production of printed circuit boards.
Chemically deposited finished coatings, on the other hand, are thicker and their use
is determined by their mechanical. electrical. and magnetic properties. The most popular
are nickel (NI-P and Ni-B) coatings deposited on metal products. Copper coatings
20-30
pm
thick, deposited on plastics. exhibit good electrical conductivity and ductility
and, therefore. are used
in
the production
of
printed circuit boards by additive processes.
The entire circuit pattern is obtained by electroless techniques.
Coatings of cobalt and its alloys may be used
to
take advantage of their specific
magnetic properties; silver and gold coatings are used because
of
their
good
electrical
conductivity, optical properties, and inertness.
Electroless plating may be performed by using the plating solution once
(until
a
greater part of any component in the solution is consumed and the reaction rate has sharply
decreased) or by replenishing the substances that have been consumed in the course of
plating. Long-term exploitation
of
solutions reduces the amount of plating wastes and
ensures a higher labor productivity, but at the same time.
it
imposes more stringent require-
ments
on
plating solutions: they must be stable, and their parameters should
not
vary
significantly with time. Besides, special equipment is required for monitoring and control-
ling the composition of such solutions. For this reason, long-term exploitation of solutions
is applied
only
in
large-scale production processes.
Single-use solutions are more versatile. but they are less economic and less efficient.
A
single-use method may be applied rather efficiently. however, when the solution has a