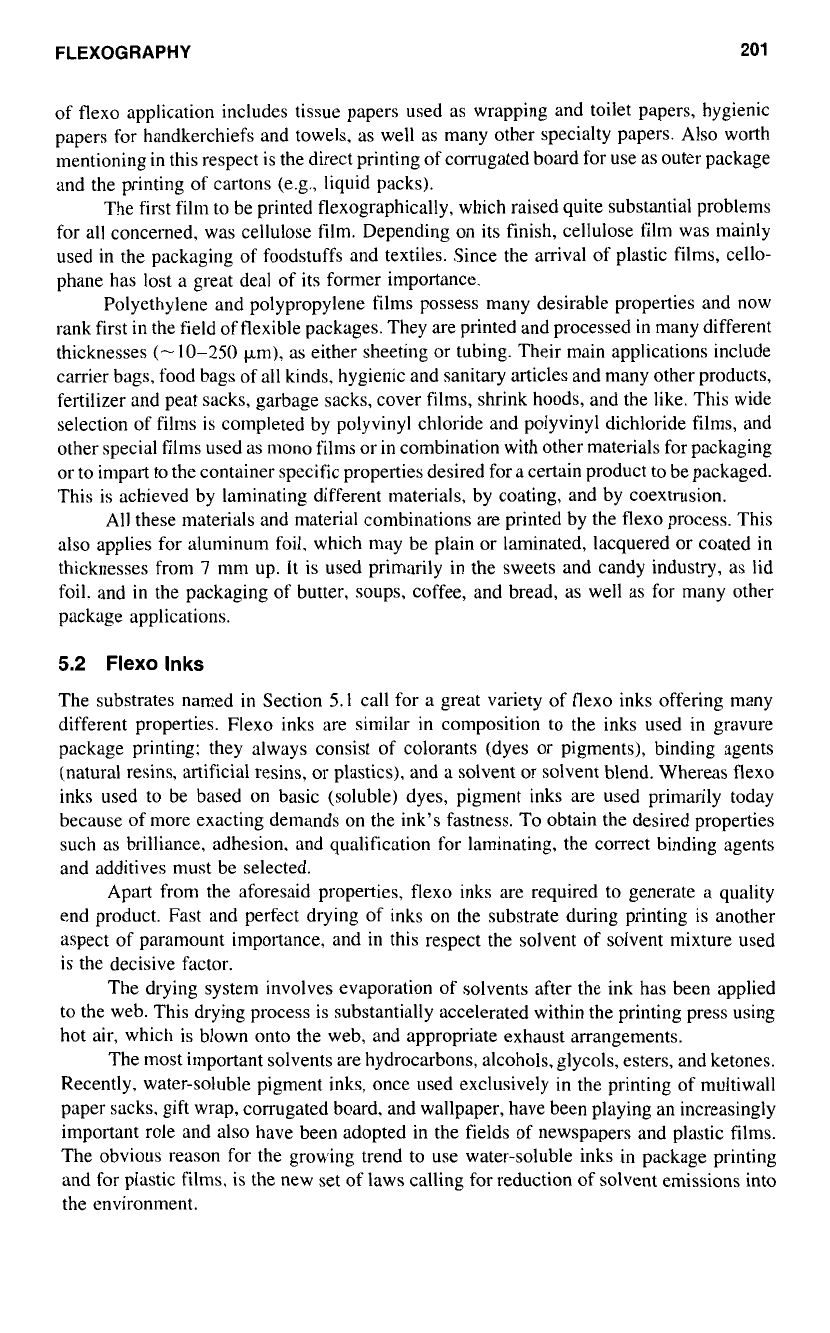
FLEXOGRAPHY
201
of
flexo application includes tissue papers used as wrapping and toilet papers, hygienic
papers for handkerchiefs and towels. as well as many other specialty papers. Also worth
mentioning in this respect is the direct printing
of
corrugated board for use as outer package
and the printing
of
cartons (e.g., liquid packs).
The first film
to
be printed flexographically, which raised quite substantial problems
for all concerned, was cellulose film. Depending on its finish, cellulose film was mainly
used in the packaging
of
foodstuffs and textiles. Since the arrival
of
plastic films, cello-
phane has lost a great deal of its former importance.
Polyethylene and polypropylene films possess many desirable properties and now
rank first in the field of flexible packages. They are printed and processed
in
many different
thicknesses
(-
10-250
km), as either sheeting or tubing. Their main applications include
carrier bags, food bags of all kinds, hygienic and sanitary articles and many other products,
fertilizer and peat sacks, garbage sacks, cover films, shrink hoods, and the like. This wide
selection of films is completed by polyvinyl chloride and polyvinyl dichloride films, and
other special films used as mono films or in combination with other materials for packaging
or
to
impart to the container specific properties desired for a certain product to be packaged.
This is achieved by laminating different materials, by coating, and by coextrusion.
All these materials and material combinations are printed by the flexo process. This
also applies for aluminum foil. which may be plain or laminated, lacquered or coated in
thicknesses from
7
mm up. It is used primarily in the sweets and candy industry, as lid
foil, and
in
the packaging
of
butter, soups, coffee, and bread, as well as for many other
package applications.
5.2
Flexo
Inks
The substrates named
in
Section
5.1
call for a great variety of flexo inks offering many
different properties. Flexo inks are similar
in
composition to the inks used in gravure
package printing; they always consist of colorants (dyes or pigments), binding agents
(natural resins, artificial resins, or plastics), and
a
solvent or solvent blend. Whereas flexo
inks used to be based on basic (soluble) dyes, pigment inks are used primarily today
because of more exacting demands on the ink’s fastness. To obtain the desired properties
such as brilliance, adhesion. and qualification for laminating, the correct binding agents
and additives must be selected.
Apart from the aforesaid properties, flexo inks are required to generate a quality
end product. Fast and perfect drying of inks on the substrate during printing is another
aspect of paramount importance, and in this respect the solvent of solvent mixture used
is the decisive factor.
The drying system involves evaporation of solvents after the ink has been applied
to the web. This drying process is substantially accelerated within the printing press using
hot air, which is blown onto the web, and appropriate exhaust arrangements.
The most important solvents are hydrocarbons, alcohols, glycols, esters, and ketones.
Recently, water-soluble pigment inks, once used exclusively in the printing of multiwall
paper sacks, gift wrap, corrugated board, and wallpaper, have been playing an increasingly
important role and also have been adopted in the fields of newspapers and plastic films.
The obvious reason for the growing trend to use water-soluble inks in package printing
and for plastic films, is the new set of laws calling for reduction
of
solvent emissions into
the environment.