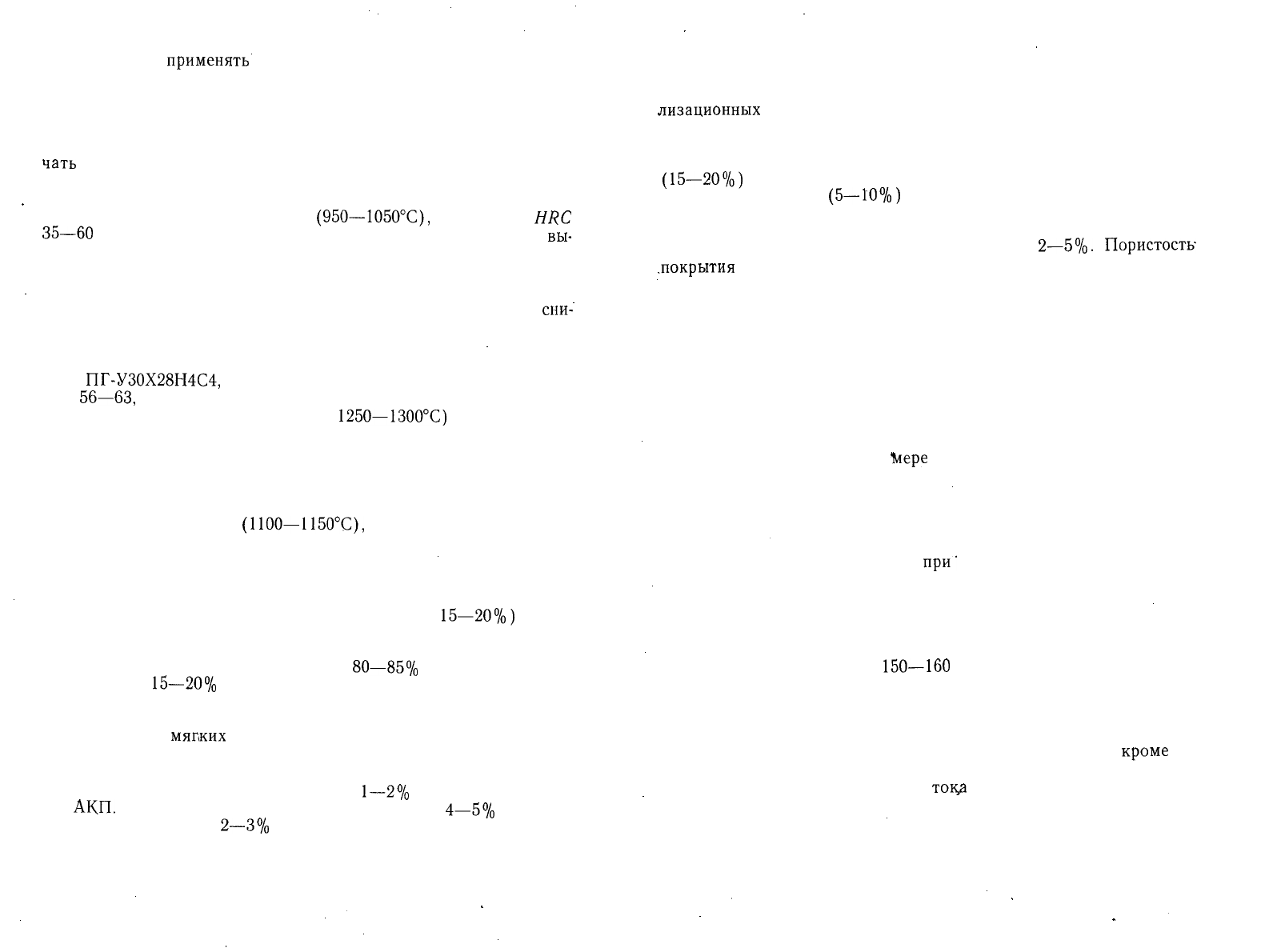
Для восстановления деталей, работающих в условиях трения,
рекомендуется
применять
износостойкие порошковые сплавы на
основе никеля или более дешевые сплавы на основе железа с
высоким содержанием углерода. Эти сплавы обладают высокими
технологическими и эксплуатационными свойствами. Наличие в
их структуре твердых составляющих (карбидов и боридов) и
сравнительно мягкой основы (твердого раствора) позволяет полу-
чать
покрытия с высокими служебными свойствами.
Порошковые сплавы на основе никеля марок ПГ-ХН80СР2,
ПГ-ХН80СРЗ и ПГ-ХН80СР4 обладают рядом ценных свойств:
низкой температурой плавления
(950—1050°С),
твердостью
HRC
35—60
в зависимости от содержания бора, жидкотекучестью,
вы-
сокой износостойкостью и свойством самофлюсования благодаря
наличию в составе бора (Р) и кремния (С), которые активно от-
нимают кислород от окислов.
Основной их недостаток — высокая стоимость, которая
сни-
жает эффективность применения этих сплавов при восстановле-
нии деталей.
Сплавы на основе железа с высоким содержанием углерода
типа
ПГ-УЗОХ28Н4С4,
ФБХ-6-2, КБХ имеют высокую твердость
HRC
56—63,
высокую износостойкость, недефицитны, но более
тугоплавки (температура плавления
1250—1300°С)
и не обладают
свойством самофлюсования.
На практике получили применение композиционные смеси
этих порошков с порошками сплавов на основе никеля. Порошко-
вая смесь, состоящая из 50% ПГ-ХН80СРЗ и 50%
ПГ-УЗОХ28Н4С4, имеет высокую износостойкость, невысокую
температуру плавления
(1100—1150°С),
обладает свойством са-
мофлюсования и стоит в 2 раза дешевле порошковых сплавов на
основе никеля.
Порошковые сплавы на основе никеля и железа, а также их
смеси обеспечивают высокую износостойкость напыленных дета-
лей, но одновременно несколько повышают (на
15—20%)
износ
сопряженных деталей, изготовленных из мягких антифрикцион-
ных сплавов. Этот недостаток может быть устранен при примене-
нии порошковой смеси, состоящей из
80—85%
стального порош-
ка ПЖ-5М и
15—20%
порошка ПГ-ХН80СР4, которая при плаз-
менном напылении обеспечивает достаточно высокую износостой-
кость покрытия и в то же время не повышает износа сопряжен-
ных деталей из
мягких
антифрикционных сплавов.
При восстановлении посадочных поверхностей под подшипни-
ки качения в чугунных корпусных деталях следует применять
стальной порошок ПЖ-5М с добавкой
1—2%
порошка алюми-
ния
АКП.
Эта же порошковая смесь с добавкой
4—5%
медного
порошка ПМС-2 или
2—3%
никелевого порошка может быть
применена при восстановлении плазменным напылением опор под
вкладыши коренных подшипников в чугунных блоках цилиндров
дригателей.
174
3. Свойства напыленных покрытий
Напыленные покрытия по своим свойствам значительно отли-
чаются от литых металлов. Отличительной особенностью метал-
лизационных
покрытий, напыленных любым способом, является
их пористость. Пористость покрытия зависит от способа напыле-
ния, напыляемого материала, режима его нанесения и от других
факторов. При прочих равных условиях наибольшую пористость
(15—20%)
имеют покрытия, напыленные электродуговым спосо-
бом, а наименьшую
(5—10%)
— покрытия, полученные плазмен-
ным напылением. При плазменном напылении покрытия из по-
рошкового сплава на основе никеля (ПГ-ХН80СР2) было полу-
чено очень плотное покрытие с пористостью
2—5%.
Пористость-
.покрытия
при всех способах напыления возрастает с увеличением
дистанции напыления. Она будет тем ниже, чем более высокую
температуру нагрева и скорость полета будут иметь частицы ме-
талла при встрече с подложкой и чем меньше они будут окисле-
ны. Эти условия в наиболее благоприятном сочетании имеют ме-
сто при плазменном напылении. Пористость покрытия при жидко-
стном и граничном трении играет положительную роль, так как
поры хорошо удерживают смазку, что способствует повышению
износостойкости деталей. Однако пористое покрытие имеет пони-
женную механическую прочность.
Твердость покрытия является обобщенной характеристикой,
определяющей в известной
*мере
его износостойкость. Она зави-
сит от многих факторов и прежде всего от напыляемого материа-
ла и режима нанесения покрытия.
При газопламенном и электродуговом напылении твердость
покрытия увеличивается с увеличением содержания углерода в
стальной проволоке. При этом твердость покрытия при газопла-
менном напылении выше, чем
при'
электродуговом. Это можно
объяснить тем, что при электродуговом напылении имеет место
более интенсивное выгорание углерода.
Большое влияние на. твердость покрытия оказывает расстоя-
ние напыления (рис. III. 5.10). Наиболее твердое покрытие из
стали 40 получается при расстоянии напыления 120 мм для элек-
тродугового напыления и
150—160
мм для газопламенного. При
малом расстоянии напыления твердость покрытия снижается
вследствие повышенного нагрева покрытия, а при большом сни-
жается благодаря уменьшению скорости полета частичек метал-
ла и увеличению пористости покрытия.
При плазменном напылении на твердость покрытия,
кроме
со-
става напыляемого порошка, большое влияние оказывают пара-
метры режима и особенно сила
токд
дуги и р'асход плазмообра-
зующего газа (рис. III. 5.11).
Износостойкость напыленных покрытий в условиях трения со
смазкой значительно выше, чем износостойкость исходного мате-
риала. Это объясняется тем, что пористое покрытие хорошо удер-
живает смазку и поэтому снижает коэффициент трения.
175