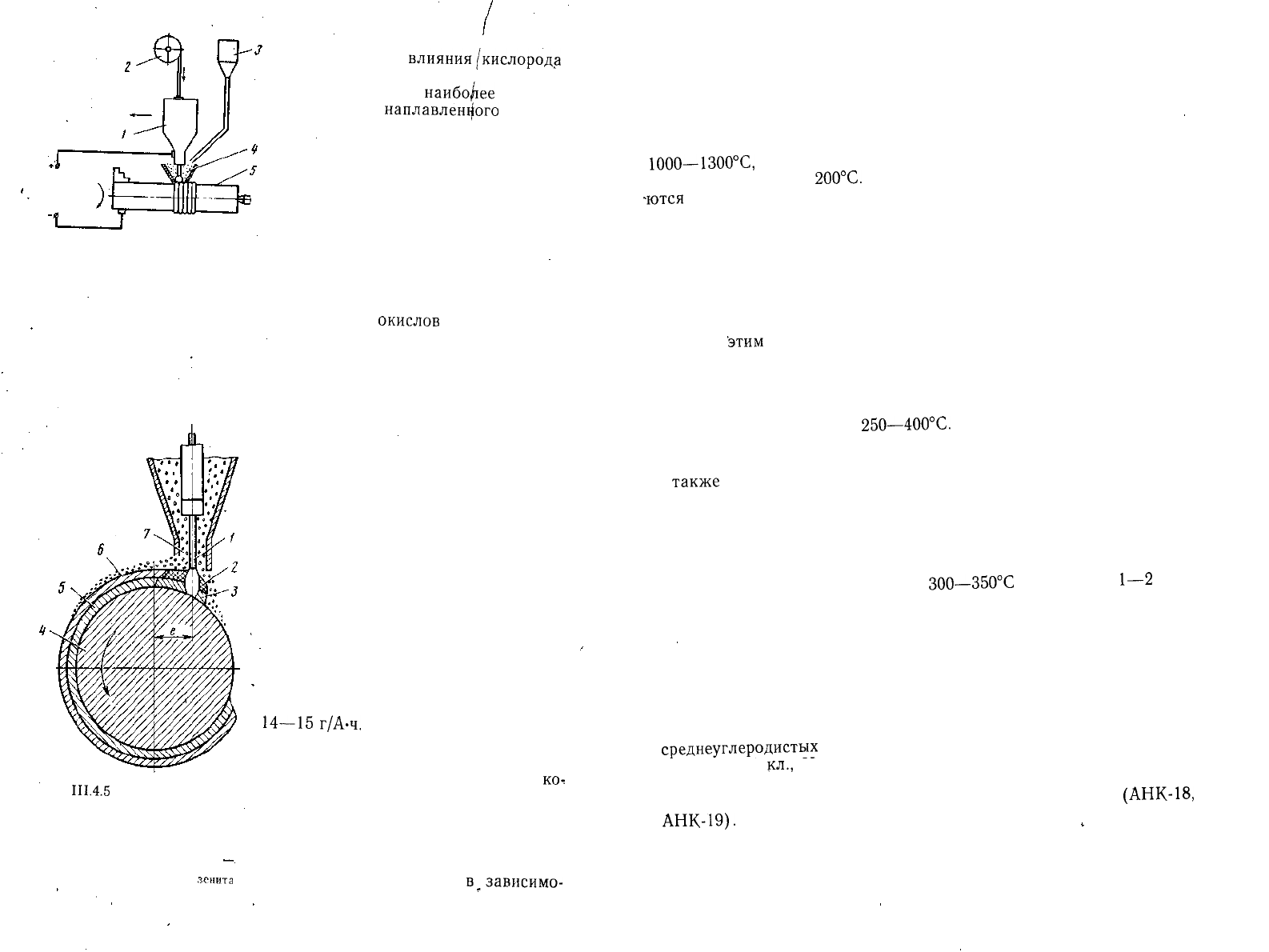
Рис. III.4.4. Принципиальная
схема автоматической электро-
дуговой наплавки деталей под
флюсом:
/ — наплавочный аппарат; 2 —
кассета с проволокой; 3 — бун-
кер с флюсом; 4 — электродная
проволока; 5 — наплавляемая де-
таль
Рис.
III.4.5
Схема автомати-
ческой наплавки под флюсом:
/ — электрод; 2 — расплавлен-
ный флюс; 3 — расплавленный
металл; 4 — основной металл;
5. — наплавленный металл; 6
—
шлаковая корка; 7 — флюс;
е — смещение электрода с
зенита
146
жидкого металла полностью защище-
ны от вредного
влияния/кислорода
и
азота воздуха, а медленное охлажде-
ние способствует
наибо/iee
полному
удалению из
наплавленного
металла
газов и шлаковых включений. Мед-
ленное охлаждение наплавленного
металла обеспечивает также более
благоприятные условия для наиболее
полного протекания диффузионных
процессов и, следовательно, легиро-
вания металла через проволоку и
флюс. Полностью исключается воз-
можность разбрызгивания металла.
Причиной разбрызгивания металла,
как известно, является реакция вос-
становления
окислов
железа углеро-
дом с образованием углекислого газа.
Возможность протекания этой реак-
ции при наплавке под флюсом почти
полностью исключается, так как От-
сутствует окисление металла.
• При автоматической наплавке за-
данный режим почти не изменяется,
поэтому в каждый момент времени
расплавляется вполне определенное
количество электродного металла и
флюса. Это Обеспечивает получение
наплавленного металла, равномерно-
го по химическому составу и свой-
ствам. 1
Автоматическая наплавка под
флюсом отличается высокой произво-
дительностью процесса. Коэффициент
наплавки при автоматической на-
плавке под флюсом за счет более эф-
фективного использования тепловой
энергии в 1,5 раза выше, чем при
ручной наплавке, и составляет
14—15
г/А-ч.
В зависимости от величины сва-
рочного тока производительность про-
цесса автоматической наплавки
ко-:
леблется от 1,5 до 10 кг/ч. Наплав-
ленный слой металла получается рав-
номерным по толщине, что позволяет
уменьшить припуск на обработку де-
талей после наплавки. Толщина слоя
наплавленного металла
в_зависимо-
сти от режима может быть получена в пределах от 0,5 до 5 мм
и более.
При автоматической электродуговой наплавке, так же как и
при ручной, возможно возникновение трещин и образование пор
в наплавленном металле.
Возникающие при наплавке трещины бывают двух видов: кри-
сталлизационные (горячие), образующиеся при температуре
1000—1300°С,
и хрупкие (холодные), которые появляются при ох-
лаждении детали до
200°С.
Хрупкие (холодные) трещины образу-
ется
вследствие внутренних напряжений, возникающих
при на-
плавке деталей. Уменьшить возможность их возникновения можно
путем подогрева деталей перед наплавкой и медленным охлажде-
нием после наплавки.
Причинами образования кристаллизационных (горячих) трещин
являются растягивающие внутренние напряжения, возникающие в
металле при охлаждении и образование прослоек жидкой эвтекти-
ки, которые ослабляют межкристаллизационные связи. Меры
борьбы с
'этим
видом трещин определяются причинами их возник-
новения и должны быть направлены на уменьшение внутренних
напряжений и устранение эвтектических прослоек между кристал-
лами. Растягивающие внутренние напряжения в наплавленном
металле могут быть уменьшены за счет подогрева детали перед на-
плавкой до температуры
250—400°С.
Образование жидкой эвтек-
тики по границам зерен можно уменьшить путем применения сва-
рочной проволоки с минимальным содержанием углерода и серы,
а
также
введением в состав проволоки и флюса веществ, содержа-
щих марганец, алюминий и титан, которые связывают серу.
Основной причиной возникновения пор в наплавленном метал-
ле является проникновение в него водорода из влаги, содержащей-
ся в гигроскопичном флюсе. Поэтому для уменьшения пористости
наплавленного металла рекомендуется перед употреблением про-
каливать флюс при температуре
300—350°С
в течение
1—2
ч и
вводить в состав флюса вещества, содержащие фтор и кремний,
которые связывают водород.
Физико-механические свойства наплавленного металла при ав-
томатической наплавке под флюсом в значительной степени зави-
сят от выбора электродной проволоки и флюса. Наибольшее при-
менение в авторемонтном производстве нашли электродные прово-
локи следующих марок: для наплавки деталей из малоуглероди-
стых сталей — св. 08, св. 08ГС и др.; для наплавки деталей из
среднеуглеродистых
и низколегированных сталей — пружинная
проволока 2
кл.,
Нп-65, Нп-80, Нп-ЗОХГСА и др.
При автоматической наплавке применяют два вида флюсов:
плавленые (АН-348А, АН-20, АН-30) и керамические
(АНК-18,
АНК-19).
Для получения наплавленного металла требуемого химического
состава и свойств применяют следующие способы легирования:
легирование через электродную проволоку, легирование через
147