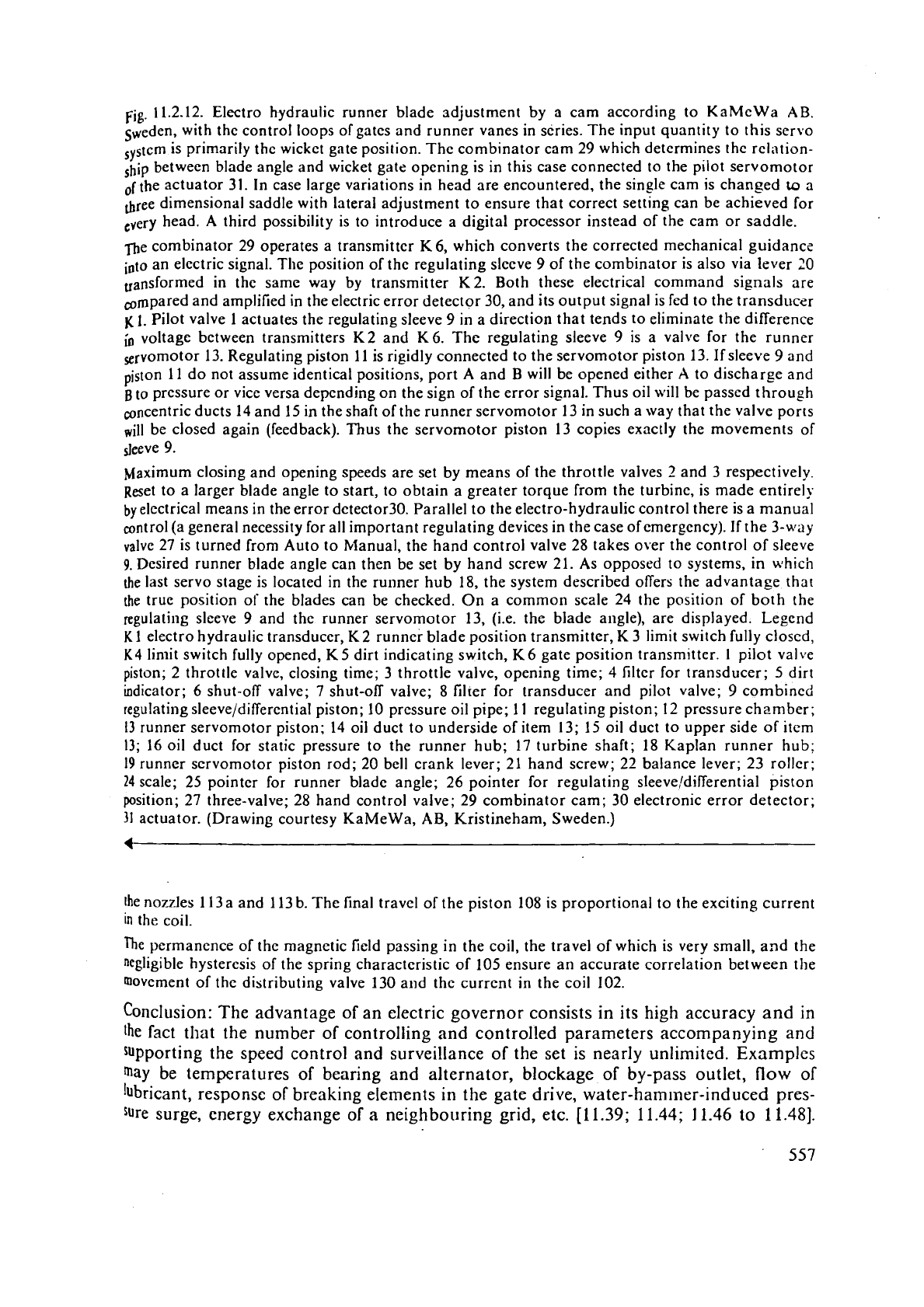
Fig. 11.2.12. Electro hydraulic runner blade adjustment by a cam according to KaMeWa
AB.
sWeden, with the control loops of gates and runner vanes in series. The input quantity to this servo
is primarily the wicket gate position. The combinator cam 29 which determines
thc relation-
ship
between blade angle and wicket gate opening is in this case connected to the pilot servomotor
*fthe actuator 31. In case large variations in head are encountered, the single cam is changed
to
a
dimensional saddle with lateral adjustment to ensure that correct setting can be achieved for
head. A third possibility is to introduce a digital processor instead of the cam or saddle.
The combinator 29 operates a transmitter K
6,
which converts the corrected mechanical guidancs
into an electric signal. The position of the regulating sleeve 9 of the combinator is also via lever 20
tIansformed in the same way by transmitter K2. Both these electrical command signals are
@mpared and amplified in the electric error detector 30, and its output signal is fed to the transducer
K
1. Pilot valve 1 actuates the regulating sleeve 9 in a direction that tends to eliminate the difference
voltage between transmitters K2 and K6. The regulating sleeve 9 is a valve for the runner
%rvomotor 13. Regulating piston 11 is rigidly connected to the servomotor piston 13. If sleeve 9 and
piston 11 do not assume identical positions, port A and
B
will be opened either
A
to discharge and
B
to pressure or vice versa depending on the sign of the error signal. Thus oil will be passed through
@ncentricducts 14 and 15 in the shaft of the runner servomotor 13 in such a way that the valve ports
will be closed again (feedback). Thus the servomotor piston 13 copies exactly the movements of
sleeve 9.
Maximum closing and opening speeds are set by means of the throttle valves
2
and 3 respectively.
Reset to a larger blade angle to start, to obtain a greater torque from the turbine, is made entirely
by
electrical means in the error detector30. Parallel to the electro-hydraulic control there is a manual
control (a general necessity for all important regulating devices in the case of emergency).
If
the 3-way
valve 27 is turned from Auto to Manual, the hand control valve 28 takes over the control of sleeve
9.
Desired runner blade angle can then be set by hand screw 21. As opposed to systems, in which
the last servo stage is located in the runner hub 18, the system described offers the advantage that
the true position of the blades can be checked. On a common
sczle 24 the position of both the
regulatiilg sleeve 9 and the runner servomotor 13, (i.e. the blade angle), are displayed. Legend
K
1
electro hydraulic transduccr,
K
2
runner blade position transmitter, K 3 limit switch fully closed,
K4
limit switch fully opened, K 5 dirt indicating switch,
K
6 gate position transmitter.
1
pilot valve
piston; 2 throttle valve, closing time; 3 throttle valve, opening time;
4
Iilter for transducer; 5 dirt
indicator;
6
shut-off valve; 7 shut-off valve;
8
filter for transducer and pilot valve; 9 combined
regulating
sleeve/difJerential piston; 10 pressure oil pipe;
I1
regulating piston;
12
pressure chamber;
13 runner servomotor piston; 14 oil duct to underside of item 13;
15 oil duct to upper side
of
item
13; 16 oil duct for static pressure to the runner hub; 17 turbine shaft; 18 Kaplan runner hub:
19
runner servomotor piston rod; 20 bell crank lever; 21 hand screw; 22 balance lever; 23 roller;
24
scale; 25 pointer for runner blade angle; 26 pointer for regulating sleeve/differential piston
position; 27 three-valve; 28 hand control valve; 29 combinator cam; 30 electronic error detector;
31
actuator. (Drawing courtesy KaMeWa, AB, Kristineham, Sweden.)
the nozzles 113a and 113 b. The final travel of the piston 108 is proportional to the exciting current
in
the coil.
The permanence of the magnetic field passing in the coil, the travel of which is very small, and the
negligible hysteresis of the spring characteristic of 105 ensure an accurate correlation between
the
movement of the distributing valve 130 alld the current in the coil 102.
Conclusion: The advantage of an electric governor consists in its high accuracy and in
lhe fact that the number of controlling and controlled parameters accompanying and
supporting the speed control and surveillance of the set is nearly unlimited. Examples
may be temperatures of bearing and alternator, blockage of by-pass outlet,
flow
of
lubricant, response of breaking elements in the gate drive, water-hammer-induced pres-
sure surge, energy exchange of a neighbouring grid, et~.
[11.39; 11.44; 11.46
to
11.481.