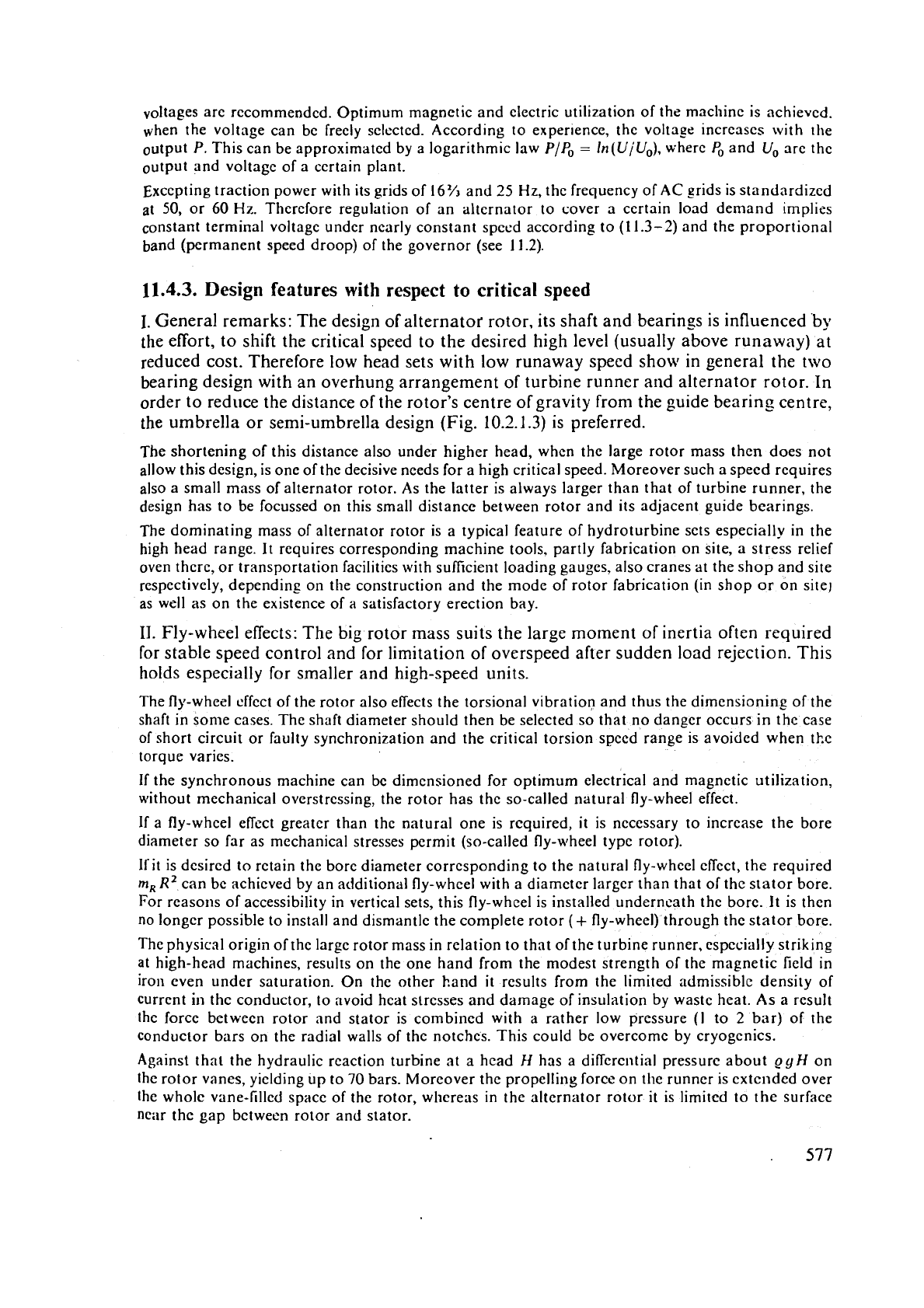
voltages are recommended. Optimum magnetic and electric utilization of the machine is achieved.
when the voltage can be freely
selcctcd. According to experrence, the voltage increases with the
output
P.
This can be approximated by a logarithmic law
PIPo
=
In(UiU,),
where
P,
and
Uo
are the
output and
voltagc of a certain plant.
Excepting traction power with its grids of 16% and
25
Hz,
the frequency of AC grids is standardizcd
at 50, or 60
Hz.
Therefore regulation of an alternator to cover a certain load demand implies
constant terminal voltage under nearly constant speed according to
(1
1.3-2) and the proportional
band (permanent speed droop) of the governor (see
11.2).
11.4.3.
Design features with respect
to
critical speed
I.
General remarks: The design of alternator rotor, its shaft and bearings is influenced by
the effort, to shift the critical speed to the desired high level (usually above runaway) at
reduced cost. Therefore low head sets with low runaway speed show in general the two
bearing design with an overhung arrangement of turbine runner
and alternator rotor. In
order to reduce the distance of the rotor's centre of gravity from the guide bearing centre,
the umbrella or semi-umbrella design (Fig.
10.2.1.3)
is preferred.
The shortening of this distance also under higher head, when the large rotor mass then does not
allow this design, is one of the decisive needs for a high critical speed. Moreover such a speed requires
also a small mass of alternator rotor. As the latter is always larger than that of turbine runner, the
design has to be focussed on this small distance between rotor and its adjacent guide bearings.
The dominating mass of alternator rotor is a typical feature of hydroturbine sets especially in the
high head range. It requires corresponding machine tools. partly fabrication on site, a stress relief
oven there, or transportation facilities with sufficient loading gauges, also cranes at the shop and site
respectively, depending on the construction and the mode of rotor fabrication (in shop or on site)
as well as on the existence of a satisfactory erection bay.
11. Fly-wheel effects: The big rotor mass suits the large moment of inertia often required
for stable speed control and for limitation of overspeed after sudden load rejection. This
holds especially for smaller and high-speed units.
The fly-wheel effect of the rotor also effects the torsional vibration and thus the dimensioning of the
shaft in
some cases. The shaft diameter should then be selected so that no danger occurs in thccase
of short circuit or faulty synchronization and the critical torsion spccd range
IS
avoided when thc
torque varies.
If the synchronous machine can be dimensioned for optimum electrical and magnetic utilization,
without mechanical overstressing, the rotor has the so-called natural fly-wheel effect.
If a fly-wheel effect greater than
the natural one is required, it
is
necessary to increase the bore
diameter so far as mechanical stresses permit (so-called fly-wheel type rotor).
II'
it
is desired to retain the borc diameter corresponding to the natural fly-wheel effect, the required
m,
R2
can be achieved by an additional fly-whcel with a diametcr larger than that of the stator bore.
For reasons of accessibility in vertical sets, this fly-wheel is installed underneath the bore. It is then
no longer possible to install and
dismantlc the complete rotor
(+
fly-wheel) through the stator bore.
The physical origin of the
largc rotor mass in relation to that of the turbine runner, especially striking
at high-head machines, results on the one hand from the modest strength of the magnetic field in
iron even under saturation. On the other hand it results from the limited admissible density of
current in
the conductor, to avoid heat stresses and damage of insulation by waste heat. As a result
the force between rotor and stator is combined with a rather low pressure
(I
to
2
bar) of the
conductor bars on the radial walls of the notches. This could be overcome by cryogenics.
Against that the hydraulic reaction turbine at a
head
H
has a
differential
pressure about
g
y
H
on
the rotor vanes, yielding up to 70 bars. Moreover the propelling force on the
runner is extended over
the-whole
vane-fillcd space of the rotor, whereas in the alternator rotor it is limited to the surface
near thc gap between rotor and stator.