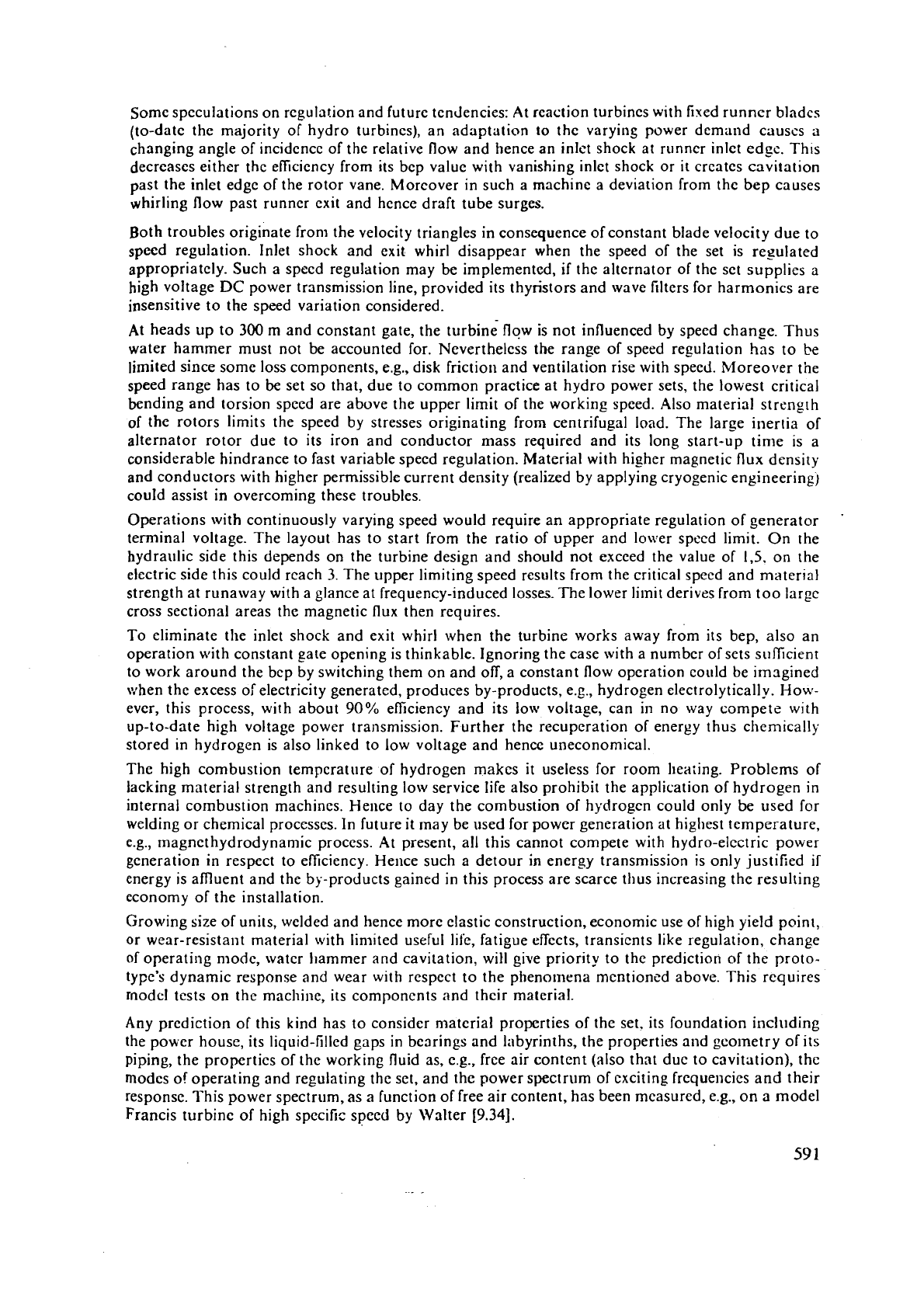
Some speculations on regulation and future tendencies: At reaction turbines with fixed runner blades
(to-date the majority of hydro turbines), an adaptation to the varying power demand causcs
a
changing angle of incidence of the relative flow and hence an inlct shock at runner inlet edgc. Th~s
decreases either the eficiency from its bep value with vanishing inlct shock or
it
creates cavitation
past the inlet edgc of the rotor vane. Moreover in such a machine a deviation from the bep causes
whirling flow past runner exit and hence draft tube surges.
Both troubles originate
from the velocity triangles in consequence of constant blade velocity due to
speed regulation.
Inlet shock and exit whirl disappear when the speed of the set is regulated
appropriately. Such a specd regulation may be implemented, if the alternator of the set supplies a
high voltage
DC
power transmission line, provided its thyristors and wave filters for harmonics are
insensitive to the speed variation considered.
At heads up to
300
m
and constant gate, the turbind flow is not influenced by speed change. Thus
water hammer must not be accounted for. Nevertheless the range of speed regulation has to be
limited since some loss components,
e.g., disk friction and ventilation rise with speed. Moreover the
speed range has to
be
set so that, due to common practice at hydro power sets, the lowest critical
bending and torsion speed are above the upper limit of the working speed. Also material
strength
of the rotors limits the speed by stresses originating from centrifugal load. The large inertia of
alternator rotor due to its iron and conductor mass required and its long start-up
time is a
considerable hindrance to fast variable speed regulation. Material with higher magnetic
flux
density
and conductors with higher permissible current density (realized by applying cryogenic engineering)
could assist in overcoming these troubles.
Operations with continuously varying speed would require
an
appropriate regulation of generator
terminal voltage. The layout has to start from the ratio of upper and lower specd limit. On the
hydraulic side this depends on the turbine design and should not exceed the value of
1,5,
on the
electric side this could reach
3.
The upper limiting speed results from the critical speed and material
strength at runaway with a glance at frequency-induced losses. The lower limit derives from too
largc
cross sectional areas the magnetic flux then requires.
To eliminate the inlet shock and exit whirl when the turbine works away from its bep, also an
operation with constant gate opening is thinkable. Ignoring the case with a number of sets
suficient
to work around the bep by switching them on and off, a constant flow operation could be imagined
when the excess of electricity generated, produces by-products, e.g., hydrogen electrolytically. I-low-
ever, this process, with about
90%
efficiency and its low voltage, can in no way compete with
up-to-date high voltage power transmission. Further the recuperation of energy thus
cl~ernically
stored in hydrogen is also linked to low voltage and hence uneconomical.
The high combustion temperature of hydrogen makes it useless for room
heating. Problems of
lacking material strength and resulting low service life also prohibit the application of hydrogen in
internal combustion machines. Hence to day the combustion of hydrogen could only be used for
welding or chemical processes. In future it may be used for power generation at highest temperature,
e.g., magncthydrodynamic process. At present, all this cannot compete with hydro-elcctric power
generation in respect to efficiency. Hence such a detour in energy transmission is only justified
if
energy is amuent and the by-products gained in this process are scarce thus increasing the resulting
economy of the installation.
Growing size of units, welded and hence more elastic construction, economic use of high yield point,
or wear-resistant material with
limited useful life, fatigue effects, transients like regulation, change
of operating mode, water
liammer and cavitation, will give priority to the prediction of the proto-
type's dynamic response and wear with respect to the phenomena mentioned above. This requires
rnodcl tests on the maclline, its components and their material.
Any prediction of this kind has to consider material properties of the set. its foundation including
the power house, its liquid-filled gaps in bearings and labyrinths, the properties
and geometry of its
piping, the properties of the working fluid as,
c.g., free air content (also that due to cavitation), the
modes
ol operating and regulating the set, and the power spectrum of exciting frequetlcies and their
response. This power spectrum, as a function of free air content, has been
rncasured, e.g., on
s
model
Francis turbine of high specific speed by Walter
[9.34].