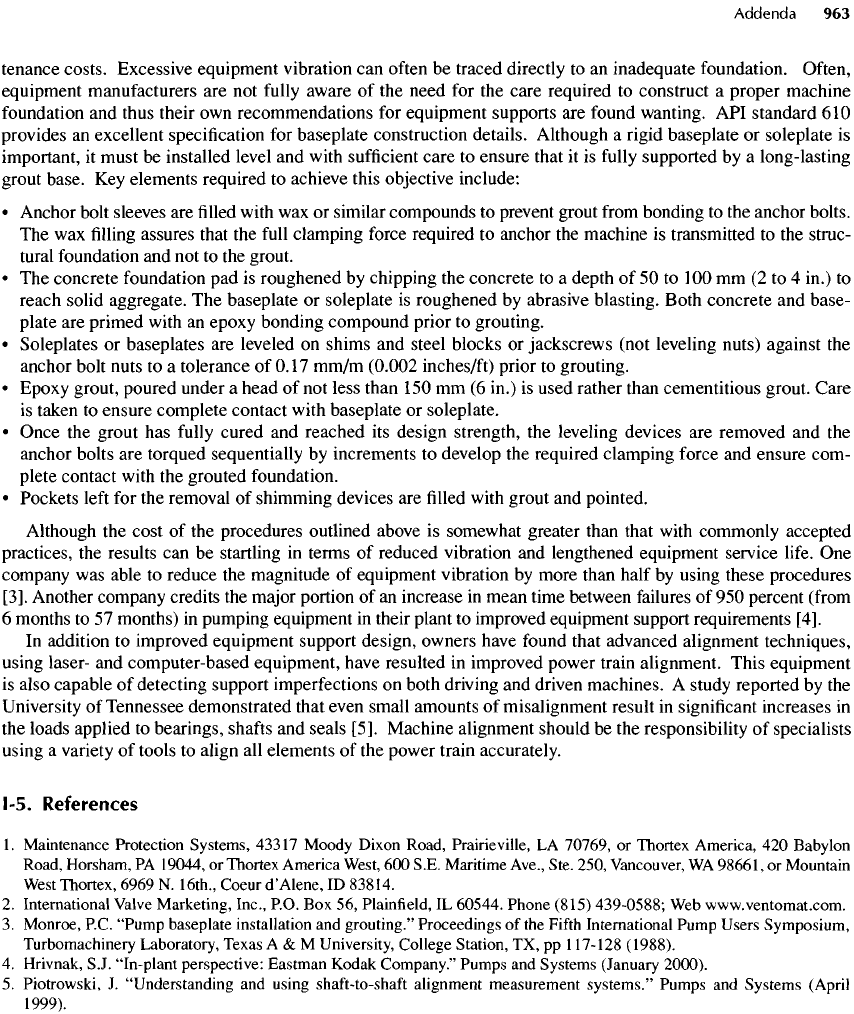
tenance
costs.
Excessive equipment vibration
can
often
be
traced directly
to an
inadequate foundation.
Often,
equipment
manufacturers
are not
fully
aware
of the
need
for the
care required
to
construct
a
proper machine
foundation
and
thus their
own
recommendations
for
equipment supports
are
found
wanting.
API
standard
610
provides
an
excellent specification
for
baseplate construction details. Although
a
rigid baseplate
or
soleplate
is
important,
it
must
be
installed level
and
with
sufficient
care
to
ensure that
it is
fully
supported
by a
long-lasting
grout base.
Key
elements required
to
achieve this objective include:
•
Anchor bolt sleeves
are
filled
with
wax or
similar compounds
to
prevent grout
from
bonding
to the
anchor
bolts.
The wax filling
assures
that
the
full
clamping force required
to
anchor
the
machine
is
transmitted
to the
struc-
tural
foundation
and not to the
grout.
• The
concrete foundation
pad is
roughened
by
chipping
the
concrete
to a
depth
of 50 to
100
mm (2 to 4
in.)
to
reach solid aggregate.
The
baseplate
or
soleplate
is
roughened
by
abrasive blasting. Both concrete
and
base-
plate
are
primed
with
an
epoxy bonding compound prior
to
grouting.
•
Soleplates
or
baseplates
are
leveled
on
shims
and
steel blocks
or
jackscrews (not leveling nuts) against
the
anchor
bolt
nuts
to a
tolerance
of
0.17
mm/m
(0.002
inches/ft) prior
to
grouting.
•
Epoxy grout, poured under
a
head
of not
less
than
150
mm (6
in.)
is
used rather than cementitious grout. Care
is
taken
to
ensure complete contact with baseplate
or
soleplate.
•
Once
the
grout
has
fully
cured
and
reached
its
design strength,
the
leveling devices
are
removed
and the
anchor bolts
are
torqued sequentially
by
increments
to
develop
the
required clamping force
and
ensure com-
plete contact
with
the
grouted foundation.
•
Pockets
left
for the
removal
of
shimming devices
are
filled
with grout
and
pointed.
Although
the
cost
of the
procedures outlined above
is
somewhat greater than that with commonly accepted
practices,
the
results
can be
startling
in
terms
of
reduced vibration
and
lengthened equipment service
life.
One
company
was
able
to
reduce
the
magnitude
of
equipment vibration
by
more than half
by
using these procedures
[3].
Another company credits
the
major
portion
of an
increase
in
mean time between
failures
of 950
percent
(from
6
months
to 57
months)
in
pumping equipment
in
their plant
to
improved equipment support requirements
[4].
In
addition
to
improved equipment support design, owners have
found
that advanced alignment techniques,
using
laser-
and
computer-based equipment, have resulted
in
improved power train alignment. This equipment
is
also capable
of
detecting support imperfections
on
both driving
and
driven machines.
A
study reported
by the
University
of
Tennessee demonstrated that even small amounts
of
misalignment result
in
significant
increases
in
the
loads applied
to
bearings,
shafts
and
seals
[5].
Machine alignment should
be the
responsibility
of
specialists
using
a
variety
of
tools
to
align
all
elements
of the
power train accurately.
1-5.
References
1.
Maintenance Protection Systems, 43317 Moody Dixon Road,
Prairieville,
LA
70769,
or
Thortex
America,
420
Babylon
Road,
Horsham,
PA
19044,
or
Thortex America West,
600
S.E. Maritime Ave.,
Ste.
250, Vancouver,
WA
98661,
or
Mountain
West
Thortex,
6969
N.
16th.,
Coeur d'Alene,
ID
83814.
2.
International Valve Marketing, Inc., P.O.
Box 56,
Plainfield,
IL
60544.
Phone (815)
439-0588;
Web
www.ventomat.com.
3.
Monroe,
PC.
"Pump baseplate installation
and
grouting." Proceedings
of the
Fifth
International Pump Users Symposium,
Turbomachinery
Laboratory, Texas
A & M
University, College Station,
TX, pp
117-128
(1988).
4.
Hrivnak,
SJ.
"In-plant
perspective: Eastman Kodak Company." Pumps
and
Systems (January
2000).
5.
Piotrowski,
J.
"Understanding
and
using
shaft-to-shaft
alignment measurement systems." Pumps
and
Systems (April
1999).