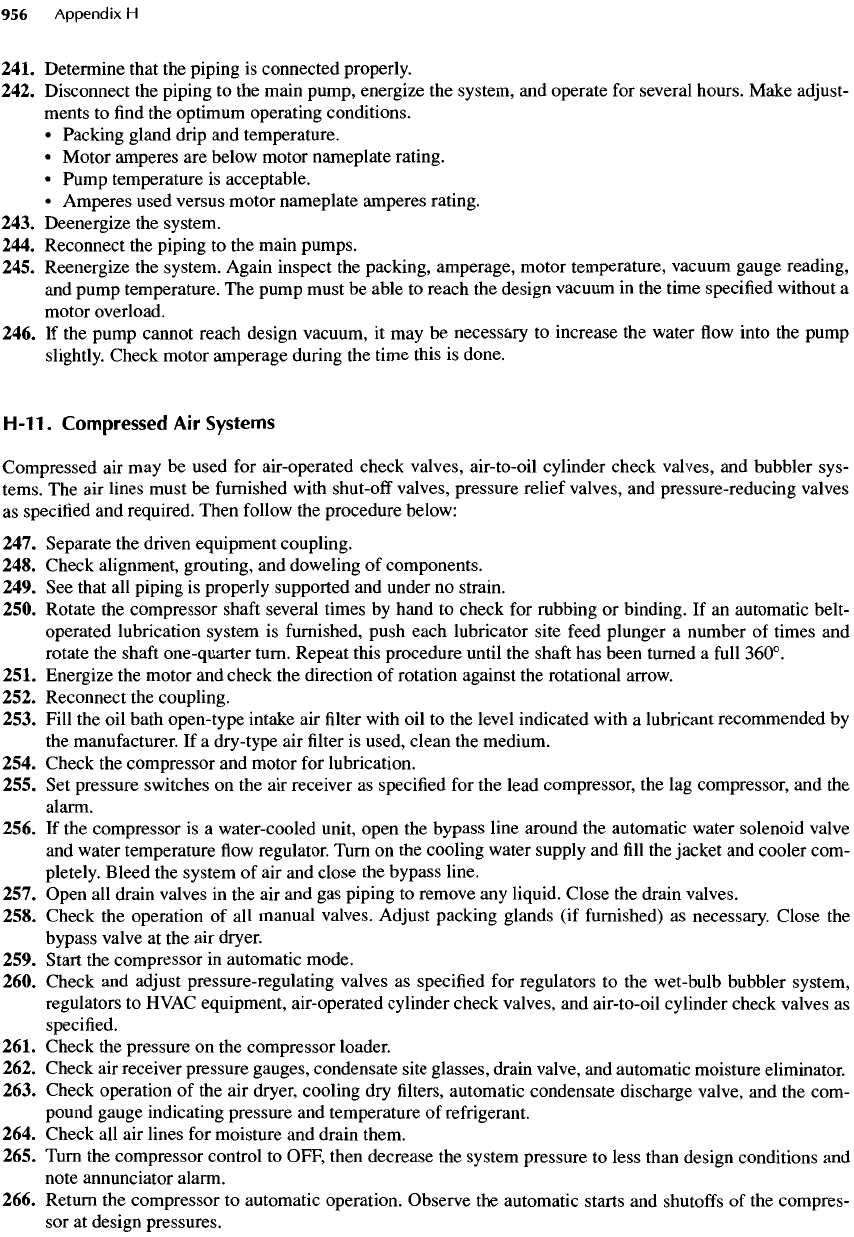
241. Determine that
the
piping
is
connected properly.
242. Disconnect
the
piping
to the
main pump, energize
the
system,
and
operate
for
several hours. Make adjust-
ments
to find the
optimum operating conditions.
•
Packing gland drip
and
temperature.
•
Motor amperes
are
below motor
nameplate
rating.
•
Pump temperature
is
acceptable.
•
Amperes used versus motor nameplate amperes rating.
243. Deenergize
the
system.
244. Reconnect
the
piping
to the
main pumps.
245. Reenergize
the
system. Again inspect
the
packing, amperage, motor temperature, vacuum gauge reading,
and
pump temperature.
The
pump must
be
able
to
reach
the
design vacuum
in the
time specified without
a
motor overload.
246.
If the
pump cannot reach design vacuum,
it may be
necessary
to
increase
the
water
flow
into
the
pump
slightly.
Check motor amperage during
the
time this
is
done.
H-11.
Compressed
Air
Systems
Compressed
air may be
used
for
air-operated check valves, air-to-oil cylinder check valves,
and
bubbler sys-
tems.
The air
lines must
be
furnished
with
shut-off
valves, pressure relief valves,
and
pressure-reducing valves
as
specified
and
required. Then
follow
the
procedure below:
247. Separate
the
driven equipment coupling.
248. Check alignment, grouting,
and
doweling
of
components.
249.
See
that
all
piping
is
properly supported
and
under
no
strain.
250. Rotate
the
compressor
shaft
several times
by
hand
to
check
for
rubbing
or
binding.
If an
automatic belt-
operated lubrication system
is
furnished,
push each lubricator site feed plunger
a
number
of
times
and
rotate
the
shaft
one-quarter turn. Repeat this procedure until
the
shaft
has
been turned
a
full
360°.
251. Energize
the
motor
and
check
the
direction
of
rotation against
the
rotational arrow.
252. Reconnect
the
coupling.
253. Fill
the oil
bath open-type intake
air filter
with
oil to the
level indicated with
a
lubricant recommended
by
the
manufacturer.
If a
dry-type
air filter is
used, clean
the
medium.
254. Check
the
compressor
and
motor
for
lubrication.
255.
Set
pressure switches
on the air
receiver
as
specified
for the
lead compressor,
the lag
compressor,
and the
alarm.
256.
If the
compressor
is a
water-cooled unit, open
the
bypass line around
the
automatic water solenoid valve
and
water temperature
flow
regulator. Turn
on the
cooling water supply
and fill the
jacket
and
cooler com-
pletely. Bleed
the
system
of air and
close
the
bypass line.
257. Open
all
drain valves
in the air and gas
piping
to
remove
any
liquid. Close
the
drain valves.
258. Check
the
operation
of all
manual valves.
Adjust
packing glands
(if
furnished)
as
necessary. Close
the
bypass
valve
at the air
dryer.
259. Start
the
compressor
in
automatic mode.
260. Check
and
adjust
pressure-regulating valves
as
specified
for
regulators
to the
wet-bulb bubbler system,
regulators
to
HVAC
equipment, air-operated cylinder check valves,
and
air-to-oil cylinder check valves
as
specified.
261. Check
the
pressure
on the
compressor loader.
262. Check
air
receiver pressure gauges, condensate site glasses, drain valve,
and
automatic moisture eliminator.
263. Check operation
of the air
dryer, cooling
dry filters,
automatic condensate discharge valve,
and the
com-
pound
gauge indicating pressure
and
temperature
of
refrigerant.
264. Check
all air
lines
for
moisture
and
drain them.
265. Turn
the
compressor control
to
OFF, then decrease
the
system pressure
to
less than design conditions
and
note
annunciator alarm.
266. Return
the
compressor
to
automatic operation. Observe
the
automatic starts
and
shutoffs
of the
compres-
sor at
design pressures.