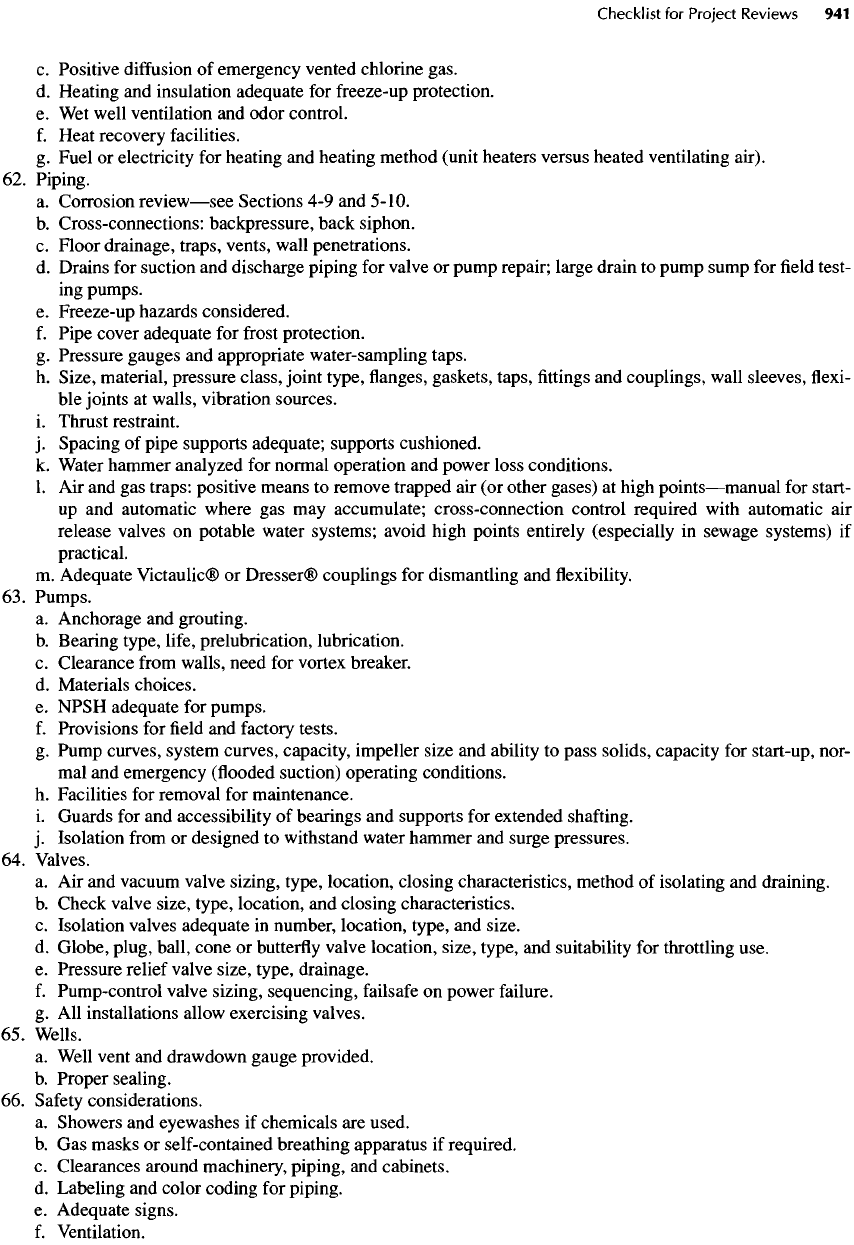
c.
Positive
diffusion
of
emergency vented chlorine gas.
d.
Heating
and
insulation adequate
for
freeze-up
protection.
e. Wet
well ventilation
and
odor control.
f.
Heat recovery facilities.
g.
Fuel
or
electricity
for
heating
and
heating method (unit heaters versus heated ventilating air).
62.
Piping.
a.
Corrosion
review—see
Sections
4-9 and
5-10.
b.
Cross-connections: backpressure, back siphon.
c.
Floor
drainage, traps, vents, wall penetrations.
d.
Drains
for
suction
and
discharge piping
for
valve
or
pump repair; large drain
to
pump sump
for field
test-
ing
pumps.
e.
Freeze-up hazards considered.
f.
Pipe
cover adequate
for
frost
protection.
g.
Pressure gauges
and
appropriate water-sampling taps.
h.
Size, material, pressure class, joint type,
flanges,
gaskets, taps,
fittings and
couplings, wall sleeves,
flexi-
ble
joints
at
walls, vibration sources.
i.
Thrust restraint.
j.
Spacing
of
pipe supports adequate; supports cushioned.
k.
Water hammer analyzed
for
normal operation
and
power loss conditions.
1.
Air and gas
traps: positive means
to
remove trapped
air (or
other gases)
at
high
points—manual
for
start-
up
and
automatic where
gas may
accumulate; cross-connection control required
with
automatic
air
release
valves
on
potable water systems; avoid high
points
entirely (especially
in
sewage systems)
if
practical.
m.
Adequate Victaulic®
or
Dresser® couplings
for
dismantling
and flexibility.
63.
Pumps.
a.
Anchorage
and
grouting.
b.
Bearing type,
life,
prelubrication,
lubrication.
c.
Clearance
from
walls, need
for
vortex breaker.
d.
Materials choices.
e.
NPSH adequate
for
pumps.
f.
Provisions
for field and
factory
tests.
g.
Pump curves, system curves, capacity, impeller size
and
ability
to
pass solids, capacity
for
start-up, nor-
mal
and
emergency
(flooded
suction) operating conditions.
h.
Facilities
for
removal
for
maintenance.
i.
Guards
for and
accessibility
of
bearings
and
supports
for
extended
shafting.
j.
Isolation
from
or
designed
to
withstand water hammer
and
surge pressures.
64.
Valves.
a. Air and
vacuum
valve sizing, type, location, closing characteristics, method
of
isolating
and
draining.
b.
Check valve size, type, location,
and
closing characteristics.
c.
Isolation valves adequate
in
number, location, type,
and
size.
d.
Globe, plug, ball, cone
or
butterfly
valve location, size, type,
and
suitability
for
throttling use.
e.
Pressure relief valve size, type, drainage.
f.
Pump-control valve sizing, sequencing,
failsafe
on
power
failure.
g.
All
installations allow exercising valves.
65.
Wells.
a.
Well vent
and
drawdown gauge provided.
b.
Proper sealing.
66.
Safety
considerations.
a.
Showers
and
eyewashes
if
chemicals
are
used.
b.
Gas
masks
or
self-contained breathing apparatus
if
required.
c.
Clearances around machinery, piping,
and
cabinets.
d.
Labeling
and
color coding
for
piping.
e.
Adequate signs.
f.
Ventilation.