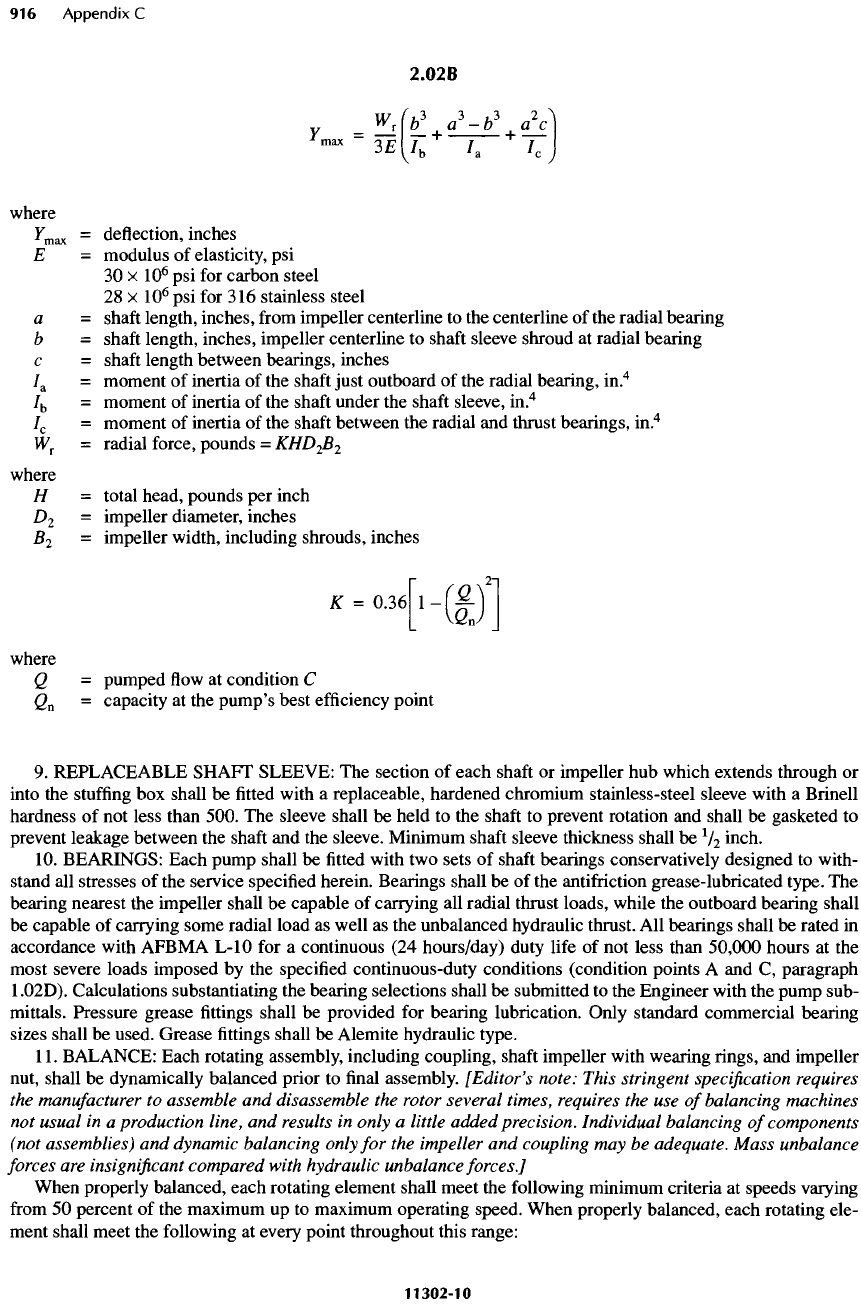
2.02B
Y
-
y
r(V,a
3
-frVV|
A
max
^F
\
J
J
7
3&^l
b
y
a
1
Cj
where
7
max
=
deflection, inches
E
=
modulus
of
elasticity,
psi
30 x
10
6
psi for
carbon steel
28
x
10
6
psi for 316
stainless steel
a
=
shaft
length,
inches,
from
impeller
centerline
to the
centerline
of the
radial bearing
b
-
shaft
length, inches, impeller centerline
to
shaft
sleeve shroud
at
radial bearing
c =
shaft
length between bearings, inches
/
a
=
moment
of
inertia
of the
shaft
just outboard
of the
radial bearing,
in.
4
/
b
=
moment
of
inertia
of the
shaft
under
the
shaft
sleeve,
in.
4
/
c
=
moment
of
inertia
of the
shaft
between
the
radial
and
thrust bearings,
in.
4
W
r
=
radial force, pounds
=
KHD
2
B
2
where
H
=
total head, pounds
per
inch
D
2
-
impeller diameter, inches
B
2
=
impeller width, including shrouds, inches
-°4-©l
where
Q
=
pumped
flow at
condition
C
Q
n
=
capacity
at the
pump's best
efficiency
point
9.
REPLACEABLE SHAFT SLEEVE:
The
section
of
each
shaft
or
impeller
hub
which extends through
or
into
the
stuffing
box
shall
be fitted
with
a
replaceable, hardened chromium stainless-steel sleeve with
a
Brinell
hardness
of not
less than 500.
The
sleeve shall
be
held
to the
shaft
to
prevent rotation
and
shall
be
gasketed
to
prevent leakage between
the
shaft
and the
sleeve. Minimum
shaft
sleeve thickness shall
be
1
I
2
inch.
10.
BEARINGS: Each pump shall
be fitted
with
two
sets
of
shaft
bearings conservatively designed
to
with-
stand
all
stresses
of the
service specified herein. Bearings shall
be of the
antifriction grease-lubricated type.
The
bearing nearest
the
impeller shall
be
capable
of
carrying
all
radial thrust loads, while
the
outboard bearing shall
be
capable
of
carrying some radial load
as
well
as the
unbalanced hydraulic thrust.
All
bearings shall
be
rated
in
accordance
with
AFBMA
L-IO
for a
continuous
(24
hours/day) duty
life
of not
less than
50,000
hours
at the
most
severe loads imposed
by the
specified continuous-duty conditions (condition points
A and C,
paragraph
1.02D).
Calculations substantiating
the
bearing selections shall
be
submitted
to the
Engineer with
the
pump sub-
mittals. Pressure grease
fittings
shall
be
provided
for
bearing lubrication. Only standard commercial bearing
sizes shall
be
used. Grease
fittings
shall
be
Alemite hydraulic type.
11.
BALANCE: Each rotating assembly, including coupling,
shaft
impeller with wearing rings,
and
impeller
nut,
shall
be
dynamically balanced prior
to final
assembly.
[Editor's
note:
This
stringent
specification
requires
the
manufacturer
to
assemble
and
disassemble
the
rotor several times, requires
the use
of
balancing machines
not
usual
in a
production
line,
and
results
in
only
a
little
added
precision. Individual balancing
of
components
(not
assemblies)
and
dynamic
balancing
only
for the
impeller
and
coupling
may be
adequate.
Mass
unbalance
forces
are
insignificant
compared
with
hydraulic unbalance
forces.]
When
properly balanced, each rotating element shall meet
the
following minimum criteria
at
speeds varying
from
50
percent
of the
maximum
up to
maximum operating
speed.
When properly balanced, each rotating ele-
ment
shall meet
the
following
at
every point throughout this range: