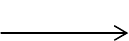
246
Окси
Mo
Этиленциангидрин из емкостей 1 подается насосом в напорный мерник 2
и далее на дегидратацию в дегидрататор, состоящий из куба 3 и насадочной ко-
лонны 4. Куб дегидрататора представляет собой стальной цилиндрический ап-
парат со свинцовой футеровкой. Рабочая температура в кубе поддерживается в
пределах 443-483 К за счет циркуляции в змеевиках и рубашке аппарата горя-
чего масла
, нагреваемого в печном отделении. Колонна дегидрататора заполне-
на алюминиевыми кольцами. Образующиеся в процессе термической дегидра-
тации этиленциангидрина пары легколетучих продуктов - акрилонитрила, воды,
аммиака и других - поступают в колонну 4 дегидрататора, а смола из куба по
сифону отводится в смеситель 8, в который насосом подается вода из нейтрали-
затора, содержащая до 15% (мас.) солей (
бисульфат аммония, сульфат натрия и
др.), аммиак и незначительные примеси акрилонитрила и этиленциангидрина.
Раствор смолы собирается в емкость 9. Для полного растворения смолы осуще-
ствляют непрерывную циркуляцию раствора в системе: емкость 9 - насос -
смеситель 8 - емкость 9. Избыток раствора смолы насосом закачивается в же-
лезнодорожные цистерны и направляется потребителям. В колонне дегидрата-
тора происходит отделение
капель жидкого этиленциангидрина от паровой фа-
зы. Жидкий зтиленциангидрин возвращается в куб 3, а его пары поступают в
дефлегматор 5, в котором пары этиленциангидрина и высококипящие примеси
конденсируются и в виде флегмы возвращаются на орошение колонны 4 дегид-
рататора.
Пары акрилонитрила, воды и других легколетучих веществ конденсиру-
ются в охлаждаемом рассолом конденсаторе 6 и
поступают на разделение во
флорентийский сосуд 7, в котором происходит расслоение жидкости на два не-
смешивающихся слоя. Верхний слой акрилонитрила-сырца направляется на
промывку, а нижний водный слой, содержащий до 6% аммиака и других при-
месей основного характера, отводится в нейтрализатор.
Процесс дегидратации проводят при 443-483 К. Повышение температуры
приводит к увеличению количества образовавшейся
смолы в кубе.
7.1.2.Окислительный аммонолиз пропилена
В 1949 г. фирма "Эллайд Кемикл" (США) сообщила о получении акрило-
нитрила прямым взаимодействием пропилена, аммиака и кислорода:
CH
2
=CHCH
3
+ NH
3
+ 1,5O
2
CH
2
=CHCN + 3H
2
O
Спустя несколько лет фирма "Дистиллерс" (Великобритания) опублико-
вала данные о возможности превращения акролеина, аммиака и кислорода в ак-
рилонитрил. Оба этих процесса характеризовались низким выходом целевого
продукта и поэтому не нашли практического применения.
Получение акрилонитрила методом окислительного аммонолиза пропи-
лена было впервые реализовано в промышленном масштабе фирмой "Сохио"
(США) в
1960 г. В настоящее время – это основной промышленный метод по-
лучения акрилонитрила. Сырьевую смесь, содержащую пропилен, аммиак, воз-
дух и водяной пар, пропускают через подвижный или "кипящий" слой твердого