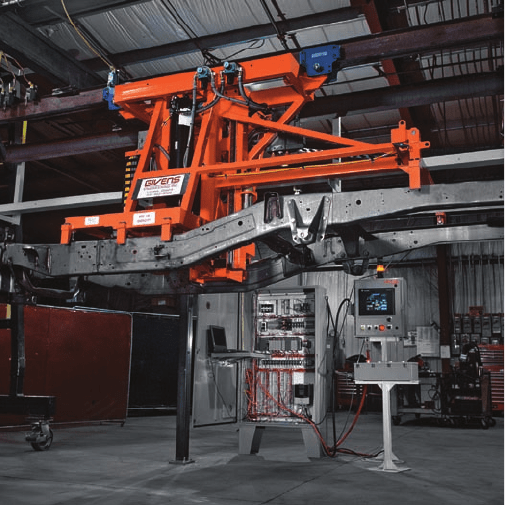
190 Chapter 9 Program Control Instructions
example, if maintenance personnel are performing rou-
tine maintenance on a de-energized motor, the machine
may suddenly become energized by someone forcing the
motor to turn on. This is why a hardwired master control
circuit is required for the I/O rack. The hardwired circuit
will provide a method of physically removing power to
the I/O system, thereby ensuring that it is impossible to
energize any inputs or outputs when the master control
is off.
9.6 Safety Circuitry
Suf cient emergency circuits must be provided to stop ei-
ther partially or totally the operation of the controller or
the controlled machine or process. These circuits should
be hardwired outside the controller so that in the event of
total controller failure, independent and rapid shutdown
is available.
Figure9-23 shows typical safety wiring requirements
for a PLC installation. The safety requirements of this in-
stallation can be summarized as follows:
• A main disconnect switch is installed on the
incoming power lines as a means of removing
power from the entire programmable controller
system.
• The main power disconnect switch should be lo-
cated where operators and maintenance personnel
have quick and easy access to it. Ideally, the discon-
nect switch is mounted on the outside of the PLC
enclosure so that it can be accessed without opening
the enclosure.
• In addition to disconnecting electrical power, you
should de-energize, lock out, and tag all other
sources of power (pneumatic and hydraulic) before
you work on a machine or process controlled by the
controller.
• An isolation transformer is used to isolate the con-
troller from the main power distribution system and
step the voltage down to 120 VAC.
• A hardwired master control relay is included to pro-
vide a convenient means for emergency controller
shutdown. Because the master control relay allows
the placement of several emergency-stop switches
in different locations, its installation is important
from a safety standpoint.
• Overtravel limit switches or mushroom head emer-
gency stop pushbuttons are wired in series so that
when one of them opens, the master control is
de-energized.
• This removes power to input and output device
circuits. Power continues to be supplied to the
2. With the right mouse button, click the I/O bit you
want to force.
3. From the menu that appears, select Go to Data Table
or select Force On or Force Off.
4. From the associated data table that appears, click on
the Forces button.
5. The Forces version of the data table appears with
the selected bit highlighted. Click on this bit with
the right mouse button.
6. From the menu that appears, you can force the se-
lected bit on or off.
Exercise care when you use forcing functions. If
used incorrectly, force functions can cause injuries
to persons working around a system, and/or equip-
ment damage. For this reason, forcing functions should
be used only by personnel who completely understand
the circuit and the process machinery or driven equip-
ment ( Figure9-22 ). You must understand the potential
effect that forcing given inputs or outputs will have on
machine operation in order to avoid possible personal
injury and equipment damage. Before using a force
function, check whether the force acts on the I/O point
only or whether it acts on the user logic as well as on the
I/O point. Most programming terminals and PLC CPUs
provide some visible means of alerting the user that a
force is in effect.
In situations in which rotating equipment is involved,
the force instruction can be extremely dangerous. For
Figure 9-22 Exercise care when you use forcing functions.
Source: Courtesy Givens Engineering Inc.
pet10882_ch09_176-199.indd 190pet10882_ch09_176-199.indd 190 7/23/10 10:05 PM7/23/10 10:05 PM