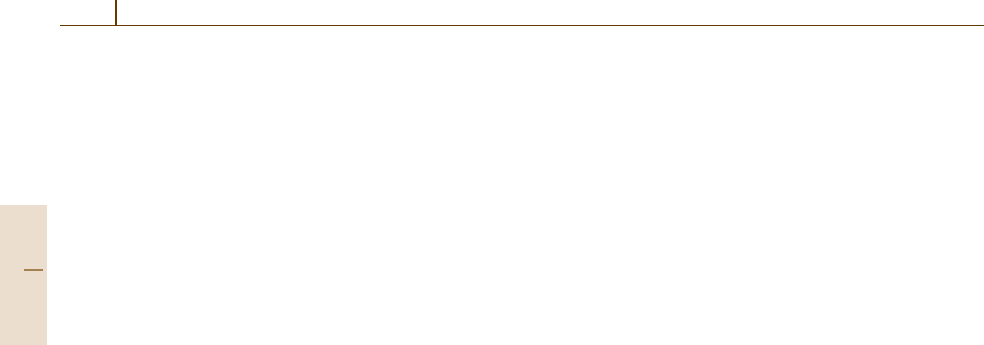
864 Part F Industrial Automation
49.3 Digital Manufacturing by RFID-Based Automation
Another major application of digital manufacturing
deals with the automatic acquisition and processing of
manufacturing data in the supply chain. This is due
to the fact that the keen competition in global manu-
facturing has rekindled interest in lean manufacturing,
reducing inventory, and efficiency in production con-
trol. There has been growing interest worldwide in the
use of RFID to digitalize the manufacturing information
so as to automate the manufacturing process. As techni-
cal problems are slowly being overcome and the cost of
using RFID is decreasing, RFID is becoming popular in
manufacturing industries. According to industrial statis-
tics, the worldwide market for RFID technology was
US$1.49billion in 2004. In the first 6 months of 2008,
6.8billion tags were sold for these applications as well
as 15.3billion tags for pallets and cases. There is great
market demand, which is ever increasing, for various
RFID applications. It is predicted that RFID industry
figures will increase from US$ 1.95 billion in 2005 to
US$26.9billion in 2015 [49.18].
The rapid increase in use of RFID technology in the
retail industry has been driven by major players such as
Gillette, Tesco, Wal-Mart, and Metro AG in Germany.
Wal-Mart, the world’s largest retailer, has started
deploying RFID applications and implementing new
procedures in some ofits distribution centers and stores.
By January 1st, 2005, Wal-Mart required its top 100
suppliers to put RFID tags on shipping crates and pal-
lets, and by January 1st, 2006, this was expanded to
its next 200 largest suppliers. The aim of the applica-
tions is to reduce out-of-stock occurrences by providing
visibility of the location of goods by using RFID tags.
Out-of-stock items that are RFID-tagged have been
found to be replenished three times faster than before,
and the amount of out-of-stock items that have to be
manually filled has been cut by 10%.
Gillette and Tesco implemented an item-level RFID
project in the UK. Gillette razor blade cartridges were
tagged with RFID tags and Tesco, the retailer, used an
RFID reader embedded smart shelf system to search for
items in the field, in order to take on-shelf inventories.
Metro AG has implemented an item-level RFID trial
for use in its future stores. RFID tags are attached to
each pack of Gillette razor blades, Proctor and Gamble
(P&G) shampoos, Kraft cream cheese, and digital ver-
satile disks (DVDs). In addition to enhancing stock re-
plenishment operations, consumers also benefit. Shop-
ping trolleys which automatically update shopping lists
and self-check-out systems have also been implemented
using this technology. This demonstrates how RFID can
revamp the retail industry and provide new customer
experiences. With better tag and reader technology, de-
clines in the cost of RFID tagging, and the release of
information-sharing platforms, it is likely that RFID
will be widely adopted across the entire supply chain.
In recent years, the use of RFID has enabled real-
time visibility and increased the processing efficiency
of shop-floor manufacturing data. RFID also supports
information flow in process-linked applications. More-
over, it can help to minimize the need for reworking,
improve efficiency, reduce line stoppages, and replenish
just-in-time materials on the production line. RFID can
assist in automating assembly-line processes and thus
reduce labor and cost, and minimize errors on the plant
floor. The integration of RFID with various manufac-
turing systems is still a challenge to many corporations.
As most large retailers will gradually demand the use
of RFID in the goods from their suppliers, this cre-
ates both pressure and the opportunity for small and
medium sized enterprises (SMEs) to adopt this tech-
nology in their logistics operations and extend it to the
control of their manufacturing processes. Some previ-
ous work [49.19] has discussed the point that RFID
can be more cost effective in bridging the gap between
automation and information flow by providing better
traceability and reliability on the shop floor.
Traditional shop-floor control in a production envi-
ronment, although computerized, still requires manual
input of shop-floor data to various systems such as
the enterprise resources planning (ERP) for production
planning and scheduling. Such data includes product
characteristics, labor, machinery, equipment utilization,
and inspection records. Companies such as Lockheed
Martin, Raytheon, Boeing [49.20], and Bell Helicopter
have installed lean data-capture software and technolo-
gies and are in the process of converting barcodes to
RFID. Honeywell was using barcodes to collect data
related to part histories, inventories, and billing, and
sharing data with its clients, and is accelerating its plan
to switch from barcodes to RFID. The use of RFID has
several advantages over barcodes, as tags that contain
microchips that can store as well as transmit dynamic
data have a fast response, do not require line of sight,
and possess high security. RFID offers greater scope
for the automation of data capture for manufacturing
process control. In recent years, the cost of RFID tags
has continuously decreased [49.21,22] while their data
capability hasincreased, whichmakes practicalapplica-
Part F 49.3