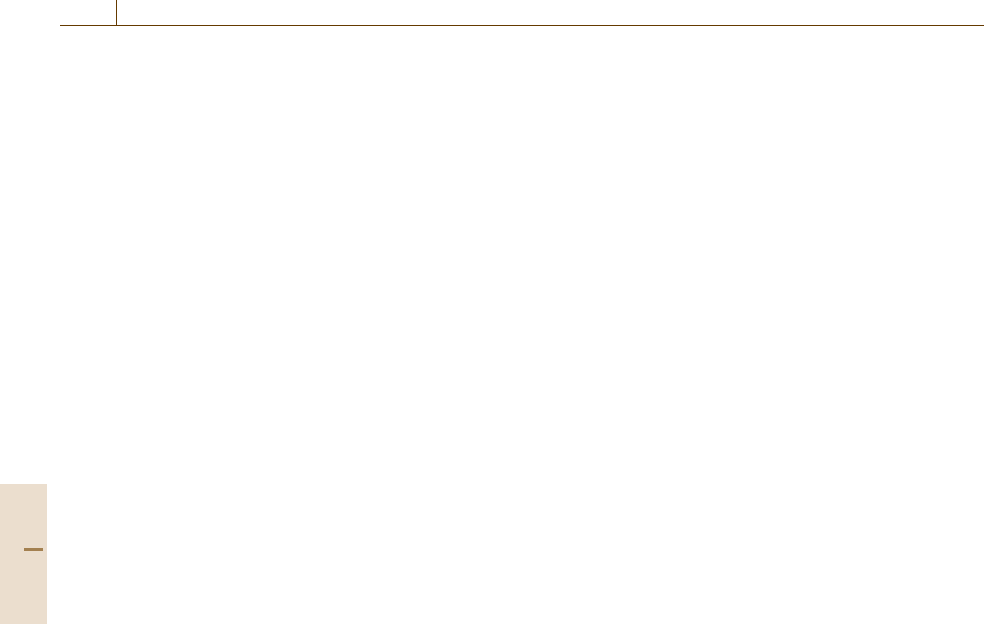
750 Part E Automation Management
aims to derivethe advantagesof horizontallyconnecting
functional silos in organizations, enhancing informa-
tion sharing, efficient change management, use of past
knowledge, and so on [43.2]. To meet this end, a PLM
system should be able to monitorthe progress of a prod-
uct at any stage in its lifecycle, to analyze issues that
might arise at any product lifecycle phase, to make
suitable decisions to address problems, and to exe-
cute and enforce these decisions. In spite of its vision,
PLM as defined above has not received much atten-
tion so far from industry because there are no efficient
tools to gather product data over the entire product
lifecycle. However, recent applications of product iden-
tification technologies in various PLM aspects [43.3–9]
demonstrate that a sound technological framework is
now available for PLM to implement its vision. Prod-
uct identification technologies enable products to have
embedded information devices (e.g., RFID tags and on-
board computers), which makes it possible to gather
the whole lifecycle data of products at any time and
at any place. A new generation of PLM systems based
on product identification technologies will make the
whole product lifecycle totally visible and will allow
all actors involved in the product lifecycle to access,
manage, and control product-related information, espe-
cially information after product delivery to customers
and up to its final destiny, without temporal or spatial
constraints. During the whole product lifecycle, we can
now have visibility of not only forward but also back-
ward information flow; for example, beginning of life
(BOL) information related to product design and pro-
duction can be used to streamline operations of middle
of life (MOL)and endof life(EOL). Furthermore,MOL
and EOL information can also go back to designers
and production engineers for the improvement of BOL
decisions. This indicates that information flow is hor-
izontally closed over the whole product lifecycle. In
addition, based on data gathered by product embedded
information devices (PEID), we can analyze product-
related information and take some decisions on the
behavior of products, which will affect data gathering
again [43.10]. This means that information flow is also
vertically closed. We call this concept and relevant sys-
tems the closed-loop PLM. The concept of closed-loop
PLM can be defined as follows: a strategic business ap-
proachfor the effective management of product lifecycle
activities by using product data/information/knowledge
which can compensate PLM to realize product lifecy-
cle optimization dynamically in closed loops with the
support of PEIDs and product data and knowledge
management (PDKM) system.
The objective of closed-loop PLM is to optimize
the performance of product lifecycle operations over
the whole product lifecycle, based on seamless prod-
uct information flow through a local wireless network
of PEIDs and associated devices and through remote
Internet connection [43.11] to knowledge repositories
in PDKM. In addition to PEIDs, sensors can be built
in products and linked to PEIDs for gathering status
data [43.12]. During product lifecycle, each lifecycle
actor can have access to PEIDs locally with PEID
controllers (e.g., RFID readers) or to a remote PLM sys-
tem for getting necessary information. Furthermore, in
closed-loop PLM, decision support systems (DSS)inte-
grated to PDKM systems may provide lifecycle actors
with suitable advice or decision support at any time.
In the closed-loop PLM, all business activities per-
formed along the product lifecycle must be coordinated
and efficiently managed. Although there are a lot of in-
formation flows and interorganizational workflows, the
business operations in closed-loop PLM are based on
the interactions among three organizations: the PLM
agent, PLM system,andproduct. The PLM agent can
gather product lifecycle information quickly from each
product with a mobile device such as a personal digital
assistant (PDA) or a fixed reader with built-in antenna.
He sends information gathered at each site (e.g., retail
sites, distribution sites, and disposal plants) to a PLM
system, as illustrated in Fig.43.1.
A PLM system provides lifecycle information or
knowledge generated by PLM agents through product
lifecycle activities realized through the three main prod-
uct lifecycle phases: BOL, MOL,andEOL.
BOL is the phase where the product concept is
generated and subsequently physically realized. In the
closed-loop PLM, designers and production engineers
will receive feedback about detailed product informa-
tion from distributors, maintenance/service engineers,
customers or remanufacturers on product status, prod-
uct usage, product service, conditions of retirement, and
disposal of their products. The feedback information is
extremely valuable for product design and production
because designers and production engineers are able
to exploit expertise and knowhow of other actors in
the product lifecycle. Hence, closed-loop PLM can im-
prove the quality of product design and the efficiency of
production.
MOL is the phase where products are distributed,
used, maintained, and serviced by customers or engi-
neers. In the closed-loop PLM,aPEID can log the
product history related to distributing routes, usage
conditions, failure, maintenance or service events, and
Part E 43.1