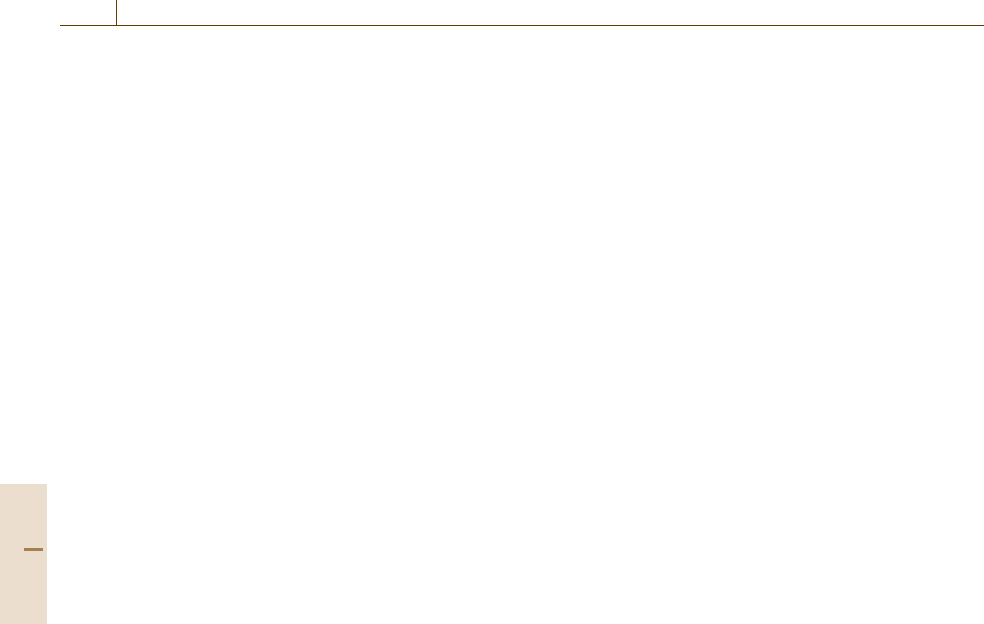
756 Part E Automation Management
using PEID technology, can gather accurate data re-
lated to product lifecycle history at the collecting and
dismantling phase of EOL products, e.g., which com-
ponents they consist of, what materials they contain,
who manufactured them, and other data that facilitate
reuse of materials, components, and parts. Based on
gathered data, EOL product experts in the PLM system
can predict degradation status and remaining lifetime
of parts or components. With this information, at the
inspection phase, the dismantler can implement EOL
product recovery optimization, in other words, decid-
ing on suitable EOL recovery options such as recycle,
reuse, remanufacturing, and disposal, with the objec-
tive of maximizing values of EOL products considering
product status. This decision also provides useful in-
formation to remanufacturers for making an efficient
remanufacturing plan in advance. Furthermore, logis-
tics engineers can improve logistics at EOL (reverse
logistics) from collecting to remanufacturing, reuse or
disposal. They can obtain supply volume data for re-
cycle, reuse, remanufacturing, and disposal products
in advance from the EOL decision. In addition, EOL
product recovery decision data and product status at
EOL dismantling can give useful information to prod-
uct designers for improving product design with several
purposes, e.g., design for reliability, reuse, recycle, and
so on.
The next step of modeling concerns the process
and events of the solution. This is well achieved with
a swim-lane chart. Figure 43.8 below shows the swim-
lane chart of closed-loop application at EOL,mainly
focusing on EOL product recovery optimization.
In this application, at first, the EOL collector gath-
ers products that have lost their values. Then, the EOL
dismantler inspects collected products visually. As a re-
sult, products can be simply classified into two parts:
disposal, and disassemblyfor moredetailed inspections.
In disassembly, the concerned components or parts will
be inspected in detail and sorted into several EOL op-
tions based on some criteria. During the inspection
and sorting process, if necessary, the dismantler ac-
cesses PEIDs of the parts or components concerned
to gather necessary data for inspecting and sorting the
EOL products. To sort EOL products in a systematic
way, the EOL dismantler asks for EOL decision sup-
port from the PLM system. EOL product experts in
the PLM system estimate the remaining value of the
parts or components concerned, based on accumulated
data, information, andknowledgeat PDKMin the PLM.
Based on the estimated remaining values and other in-
formation such as costs and benefits of recycle, reuse,
remanufacture, disposal, and so on, EOL product ex-
perts decide on an adequate EOL option for each part
or component, i.e., which parts or components should
be recycled, reused, remanufactured or disposed, un-
der some constraints related toenvironmental regulation
and product quality. This information will be stored
in the PDKM and transmitted to dismantlers. If nec-
essary, product designer and logistics engineer receive
this information from the PLM system to improve their
operations.
Based on the proposed EOL decision, dismantlers
sort the parts or components. When the EOL disman-
tler sorts products, depending on the sorting results of
EOL products, operations related to PEIDs may be dif-
ferent. They may be removed and replaced with new
ones; orits datacontents canbe reset or updated without
replacement for the second life of parts or components;
for example, in the recycle case, PEIDs will usually be
detached from products. Then, recyclable products will
be sent to specific lots that have similar materials fea-
tures. For each lot, a new PEID will be used for its
management. Each lot will be sent to recycling com-
panies. In the reuse case, after quality data of parts
or components are updated to an existing PEID, prod-
ucts will be sent to a remanufacturing site or second
market. In the remanufacturing case, after required in-
formation for remanufacturing such as current quality
data, required quality data, product specification, and
production instruction areupdated, productswill besent
to remanufacturing sites. In the case of disposal, af-
ter updating disposal-relevant data to each PEID and
PLM system by disposal engineers, products are sent
to disposal companies.
43.3.2 Selection of PEID System
Table 43.1 shows the basic functions and their corre-
sponding components of a PEID with its specifications.
Here, PEIDs can be classified into four types by their
functions and specifications.
Type A isfor simple applications.It containsonly its
ownidentification function. For this, it has a small-sized
read-only microchip that includes its own ID, config-
uration parameters, and simple logics programmed for
a specific application. A 1 bit transponder orsimple pas-
sive RFID tag is included in this type. It does not need
any power to transmit data to a PEID controller. It can
be detected by a PEID controller automatically when
it goes into the interrogation zone. Hence, it does not
need any battery. When lifecycleactors justwant toread
a small amount of product identification data without
Part E 43.3