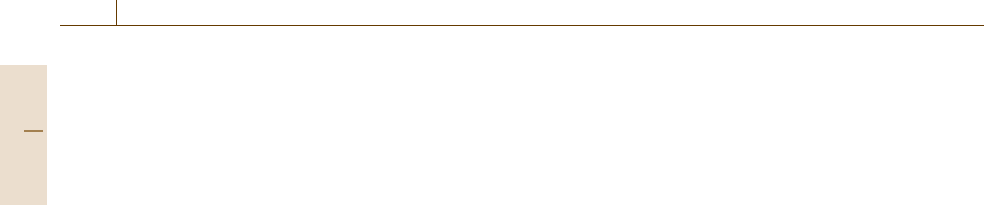
700 Part E Automation Management
their operations. This reengineering process creates
major economic benefits.
•
Modern automation solutions are reprogrammable
and reusable, with components often having lifecy-
cles longer than the planned production facility.
•
Using automation significantly reduces require-
ments for services and related facilities.
These differences lead to operational benefits that in-
clude:
•
Increased flexibility
•
Increased productivity
•
Reduced operating costs
•
Increased product quality
•
Elimination of health and safety hazards
•
Higher precision
•
Ability to run longer shifts
•
Reduced floor space.
Time-based competition and mass customization of
global markets arekeycompetitive strategies of present-
day manufacturing companies [40.7]. Average product
lifecycle in marketplaces has changed from years
to months for products based on rapidly evolving
technologies. This demands agile automated systems,
created through the concept of common manufac-
turing processes organized modularly to allow rapid
deployment in alternative configurations. These recon-
figurable automated systems represent the cornerstone
in dealing with time-based competition and mass cus-
tomization.
Justification of reconfigurable automation systems
must necessarily include strategic aspects when com-
paring them with traditional manufacturing systems
developed underthe product-centricparadigm. Product-
specific systems generally lack the economical recon-
figuration ability that would allow them to meet the
needs of additional products. Consequently traditional
systems are typically decommissioned well before their
capital cost can be recovered, and are then held in
storage until fully depreciated for tax purposes before
being sold at salvage value. However, it must be kept
in mind that reconfigurability claims for additional in-
vestment in design, implementation, and operation of
the system. Quick-change tooling are an example of re-
configurability equipment which allows rapid product
changeover. It is estimated that generic system capa-
bilities can increase the cost of reconfigurable system
hardware by as much as 25% over that of a comparable
dedicated system. On the other hand, software required
to configure and run reconfigurable automation systems
is often much more expensive to develop than simple
part-specific programs. Traditional economic evaluation
methods fail to consider benefits from capital reutiliza-
tion over multiple projects and also disregard strategic
benefits of technology. Upgrade of traditional eco-
nomic evaluation methods is required to account for the
short-term economic and long-term strategic value of
investing in reconfigurable automation technologies to
support the evolving production requirements of a fam-
ily of products. In this chapter the traditional economic
justification approach to automationsystem justification
is first addressed. A related discussion on economic as-
pects of automation not discussed in this chapter can
be found in Chap.7. New approaches to automated sys-
tem justification based on strategic considerations are
presented next. Finally, a discussion on justification ap-
proaches currently being researched for reconfigurable
systems is presented.
40.1 General Economic Rationalization Procedure
In generalterms, an economic rationalization enablesus
to compare the financial benefits expected from a given
investment project with alternative use of investment
capital. Economic evaluation measures capital cost plus
operating expenses against cash-flow benefits estimated
for the project. This section describes a general ap-
proach to economic rationalization and justification of
automation system projects.
40.1.1 General Procedure for Automation
Systems Project Rationalization
The general procedure for rationalization and analysis
of automation projects presented here consists of a pre-
cost-analysis phase, followed by a cost-analysis phase.
Figure 40.1 presents the procedure steps and their se-
quence. The sequence of steps in Fig.40.1 is reviewed
Part E 40.1