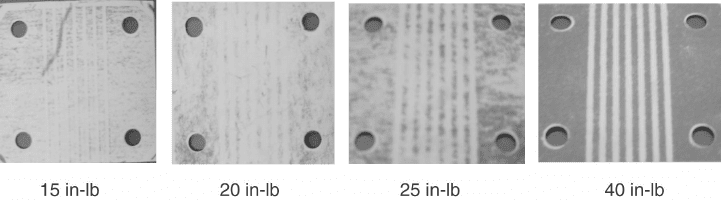
c04 JWPR067-Mench January 28, 2008 17:28 Char Count=
4.3 Region II: Ohmic Polarization 165
in performance that is not recoverable. In a brittle fuel cell or one with significant thermal
expansion of the materials such as the SOFC, thermal and compressive stresses can result
in catastrophic failure of components. Different types of fuel cells obviously have different
material limits for plastic deformation, but the qualitative shape is the same as Figure 4.31.
For low-temperature fuel cells, the presence of liquid water does not influence the contact
resistance since pure water is nonconductive.
Over time, various components may deform to relax the compression stress in the ma-
terials, loosening contacts. Some stacks are designed to be spring loaded at the endplates to
provide consistent compression. Also, since each channel design is different, with different
channel-to-land ratios, it is impossible to state an optimal compression pressure for a fuel
cell. For PEFCs, the compression pressure of 1–2 MPa is generally appropriate, but the
optimal compression pressure must be determined experimentally for a given fuel cell and
components. In general, several criteria can be used to determine the best compression on
a cell or stack:
1. Prescribed Torque or Spring Loading Imposed on All Compression Bolts or Tie-
Downs This method is common in laboratories with single cells. However, this
method is highly unreliable and can lead to significant variation in compression
pressure and uniformity, since the compression torque is a function of the inter-
facial friction on the bolt threads or between the nut and washer and the back
compression plate. In general, this method should only be used with caution on a
well-characterized fuel cell.
2. Compression Gap Width The materials under compression will have a measurable
gap width decrease under compression, and the compression force on the fuel cell is
increased until a desired elastic deformation is achieved in the stack. For example,
in the PEFC, many diffusion media work best when compressed by 10–20% of
their original thickness. Another advantage is that the gap width can be measured
at locations around the periphery to ensure uniformity of compression.
3. Compression Pressure Specification The compression pressure of the flow field on
the fuel cell is prescribed. The compression pressure can be determined experimen-
tally with a load cell inserted in the fuel cell or with pressure-sensing contact paper
as shown in Figure 4.32. The proper compression pressure can then be correlated
with the measured gap width or bolt torque.
Figure 4.32 Pictures of Pressurex pressure-sensing paper used to measure contact pressure distri-
butionin5-cm
2
fuel cell with different torque on fuel cell bolts. The higher the compression, the
better the electrical contact. At some point, however, the cell will become overcompressed.