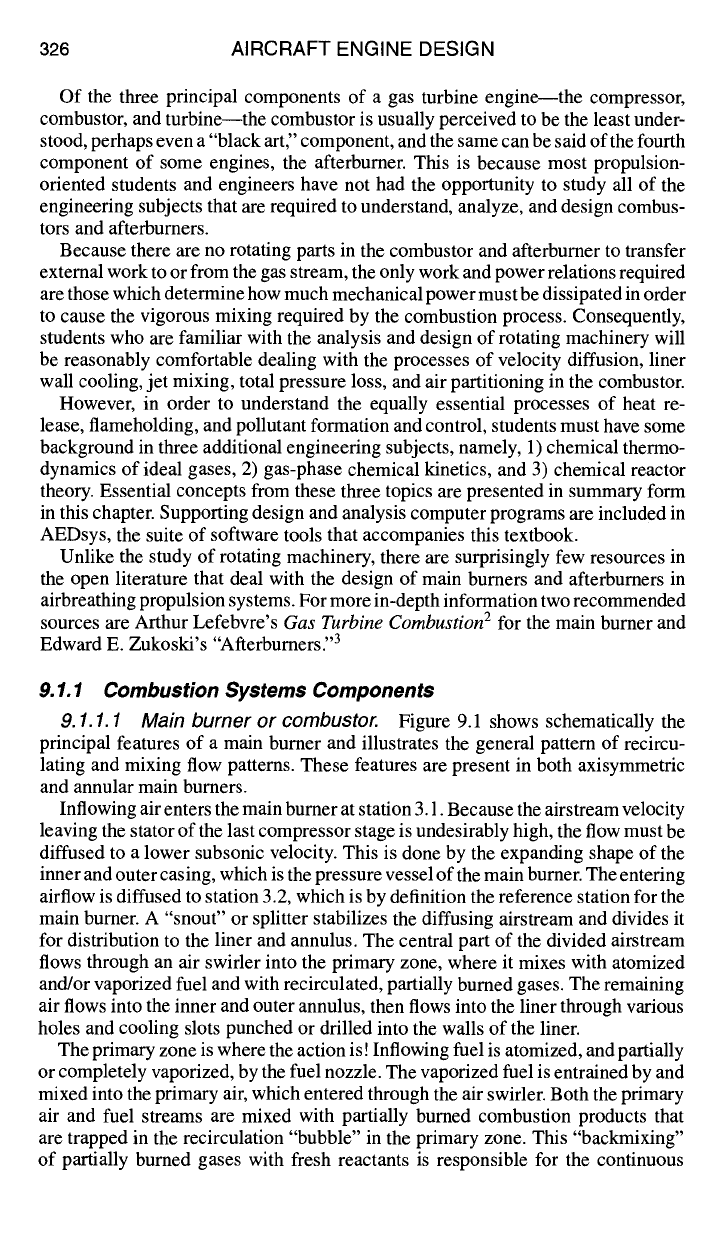
326 AIRCRAFT ENGINE DESIGN
Of the three principal components of a gas turbine engine--the compressor,
combustor, and turbine--the combustor is usually perceived to be the least under-
stood, perhaps even a "black art," component, and the same can be said of the fourth
component of some engines, the afterburner. This is because most propulsion-
oriented students and engineers have not had the opportunity to study all of the
engineering subjects that are required to understand, analyze, and design combus-
tors and afterburners.
Because there are no rotating parts in the combustor and afterburner to transfer
external work to or from the gas stream, the only work and power relations required
are those which determine how much mechanical power must be dissipated in order
to cause the vigorous mixing required by the combustion process. Consequently,
students who are familiar with the analysis and design of rotating machinery will
be reasonably comfortable dealing with the processes of velocity diffusion, liner
wall cooling, jet mixing, total pressure loss, and air partitioning in the combustor.
However, in order to understand the equally essential processes of heat re-
lease, flameholding, and pollutant formation and control, students must have some
background in three additional engineering subjects, namely, 1) chemical thermo-
dynamics of ideal gases, 2) gas-phase chemical kinetics, and 3) chemical reactor
theory. Essential concepts from these three topics are presented in summary form
in this chapter. Supporting design and analysis computer programs are included in
AEDsys, the suite of software tools that accompanies this textbook.
Unlike the study of rotating machinery, there are surprisingly few resources in
the open literature that deal with the design of main burners and afterburners in
airbreathing propulsion systems. For more in-depth information two recommended
sources are Arthur Lefebvre's
Gas Turbine Combustion 2
for the main burner and
Edward E. Zukoski's "Afterburners. ''3
9.1.1 Combustion Systems Components
9.1.1.1 Main burner or combustor. Figure 9.1 shows schematically the
principal features of a main burner and illustrates the general pattern of recircu-
lating and mixing flow patterns. These features are present in both axisymmetric
and annular main burners.
Inflowing air enters the main burner at station 3.1. Because the airstream velocity
leaving the stator of the last compressor stage is undesirably high, the flow must be
diffused to a lower subsonic velocity. This is done by the expanding shape of the
inner and outer casing, which is the pressure vessel of the main burner. The entering
airflow is diffused to station 3.2, which is by definition the reference station for the
main burner. A "snout" or splitter stabilizes the diffusing airstream and divides it
for distribution to the liner and annulus. The central part of the divided airstream
flows through an air swirler into the primary zone, where it mixes with atomized
and/or vaporized fuel and with recirculated, partially burned gases. The remaining
air flows into the inner and outer annulus, then flows into the liner through various
holes and cooling slots punched or drilled into the walls of the liner.
The primary zone is where the action is! Inflowing fuel is atomized, and partially
or completely vaporized, by the fuel nozzle. The vaporized fuel is entrained by and
mixed into the primary air, which entered through the air swirler. Both the primary
air and fuel streams are mixed with partially burned combustion products that
are trapped in the recirculation "bubble" in the primary zone. This "backmixing"
of partially burned gases with fresh reactants is responsible for the continuous