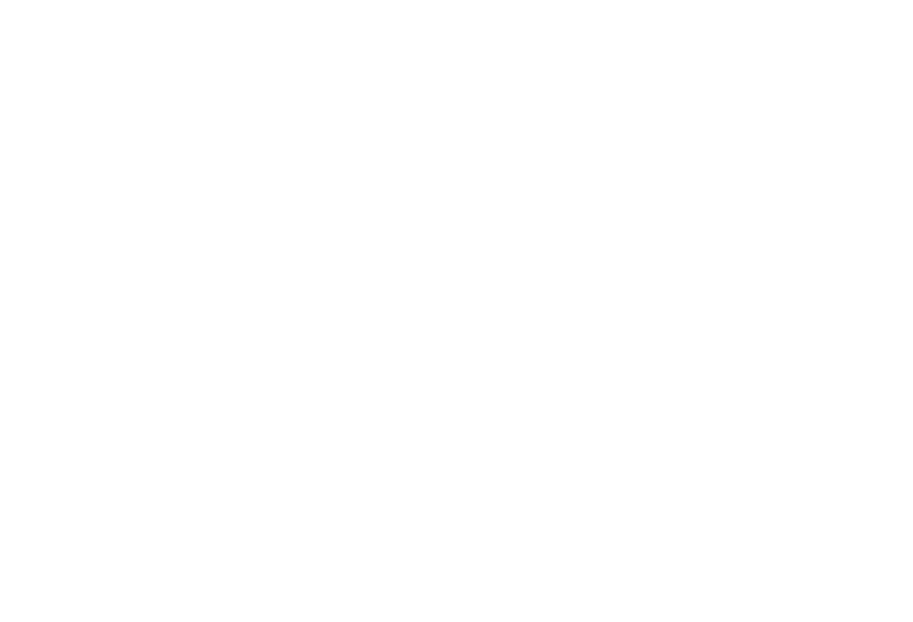
210
- с использованием разработанной программы автоматизированного расчета на ЭВМ [363]
определяется состав шихты порошковой ленты, обеспечивающий требуемый химический состав
наплавленного металла.
Показано, что при малых значениях коэффициента (К
Д
= 1,2-1,4) в наплавленном металле следует
иметь 2,0-2,5 % С, 2-3 % Mn и ∼ 12 % Cr, его структура должна быть преимущественно мартенситно-
карбидной (остаточного аустенита 20-25 %). Для указанных условий целесообразно использовать
порошковые ленты ПЛ-Нп-230Х12Г2 и ПЛ-Нп-250Х10Г4Ф3. С повышением коэффициента
динамичности необходимо уменьшать содержание углерода и увеличивать количество марганца в
наплавленном металле. При К
Д
= 3,5 оптимальным является следующее содержание легирующих
элементов в наплавленном металле: 1,0-1,7 % C, 5-6 % Mn и 12 % Cr. При этом целесообразно применять
порошковую ленту ПЛ-Нп-160X12Г5. С возрастанием К
Д
в cтpyктуре наплавленного металла
необходимо увеличивать количество остаточного аустенита и повышать его стабильность по отношению
к деформационному мартенситному превращению. В том случае, когда после наплавки структура и
фазовый состав наплавленного металла отличаются от оптимальных, то эффективным способом их
регулирования является нормализация. Ее режимы следует выбирать с учетом интенсивности ударно-
абразивного воздействия. При повышении К
Д
следует использовать более высокие температуры нагрева
для нормализации с целью увеличения количества аустенита в структуре и степени его стабильности.
Наплавку разработанными порошковыми лентами следует проводить под флюсом АН-26 по режиму:
I
CB
= 600-650 A; U
Д
= 28-32 В; V
CB
= 35 м/ч. Указанные ленты отличаются хорошими сварочно-
технологическими характеристиками. Анализ приведенных данных показывает эффективность
применения марганецсодержащих наплавочных материалов, обеспечивающих получение в
структуре
наплавленного металла метастабильного аустенита, армированного упрочняющими фазами и
реализацию эффекта самозакалки при нагружении. Деформационным мартенситным превращением
следует управлять за счет изменения химического состава наплавленного металла или режимов
термообработки после наплавки, что позволяет при оптимизации его развития получить наиболее
высокий уровень износостойкости. Примером эффективного использования предлагаемой методики
является разработка порошковой ленты ПЛ-Нп-160X12Г5 для восстановления плит щековой дробилки,
серийно изготавливаемых из 110Г13Л. Наплавленный металл имеет аустенитно-мартенситно-карбидную
структуру и твердость 39-40 HRC. Количество аустенита составляет 60-65 %, мартенсита - 25-30 %,
карбидов - остальное. Использование разработанной порошковой ленты повысило износостойкость
наплавленных деталей в 1,5 раза по сравнению с серийными [363, 365].
5.3.4. Повышение механических свойств применяемых в промышленности сталей
и высокопрочного чугуна за счет получения в их структуре метастабильного аустенита
Ранее была показана важная роль метастабильного аустенита и необходимость управления его
количеством и стабильностью для повышения механических свойств и износостойкости специально
разработанных сплавов. Представлялось важным использовать этот же принцип для повышения
механических свойств применяемых в промышленности сталей различного назначения и
высокопрочного чугуна. Некоторые закономерности по влиянию температуры нагрева под закалку и
отпуска на количество и стабильность аустенита, а также механические свойства, приведенные выше для
марганцевых и хромомарганцевых сталей, проявляются и для высокоуглеродистых типа Х12М [366,
367]. С повышением температуры нагрева под закалку от 1000 до 1200
о
С количество мартенсита и
карбидов в структуре закаленной стали снижается, а остаточного аустенита – увеличивается, что
является следствием растворения карбидов в аустените. Кривые развития мартенситного превращения
при деформации и диаграммы кручения приведены на рис. 5.34, а, б [366].
Наиболее высокий уровень прочностных свойств в сочетании с достаточной пластичностью при
кручении образцов стали Х12М достигается после закалки от 1060
о
С (рис. 5.35), когда в структуре
наряду с мартенситом и карбидами сохраняется 15-20 % остаточного аустенита. В этом случае уровень
механических свойств при кручении таков: τ
0,3
= 1300 МПа, τ
ПЧ
= 1900 МПа, g = 18 %.
После закалки с более низкой или высокой (по сравнению с оптимальной) температуры прочностные
свойства и пластичность снижаются. Это обусловлено формированием менее благоприятной структуры
(малым или, напротив, чрезмерно большим количеством остаточного аустенита) и отклонением от
оптимального развития деформационного мартенситного превращения при нагружении, что приводит к
недостаточной релаксации микронапряжений, возникающих при механических испытаниях. После
закалки с 1200
о
С, когда образуется преимущественно аустенитная структура с равномерно