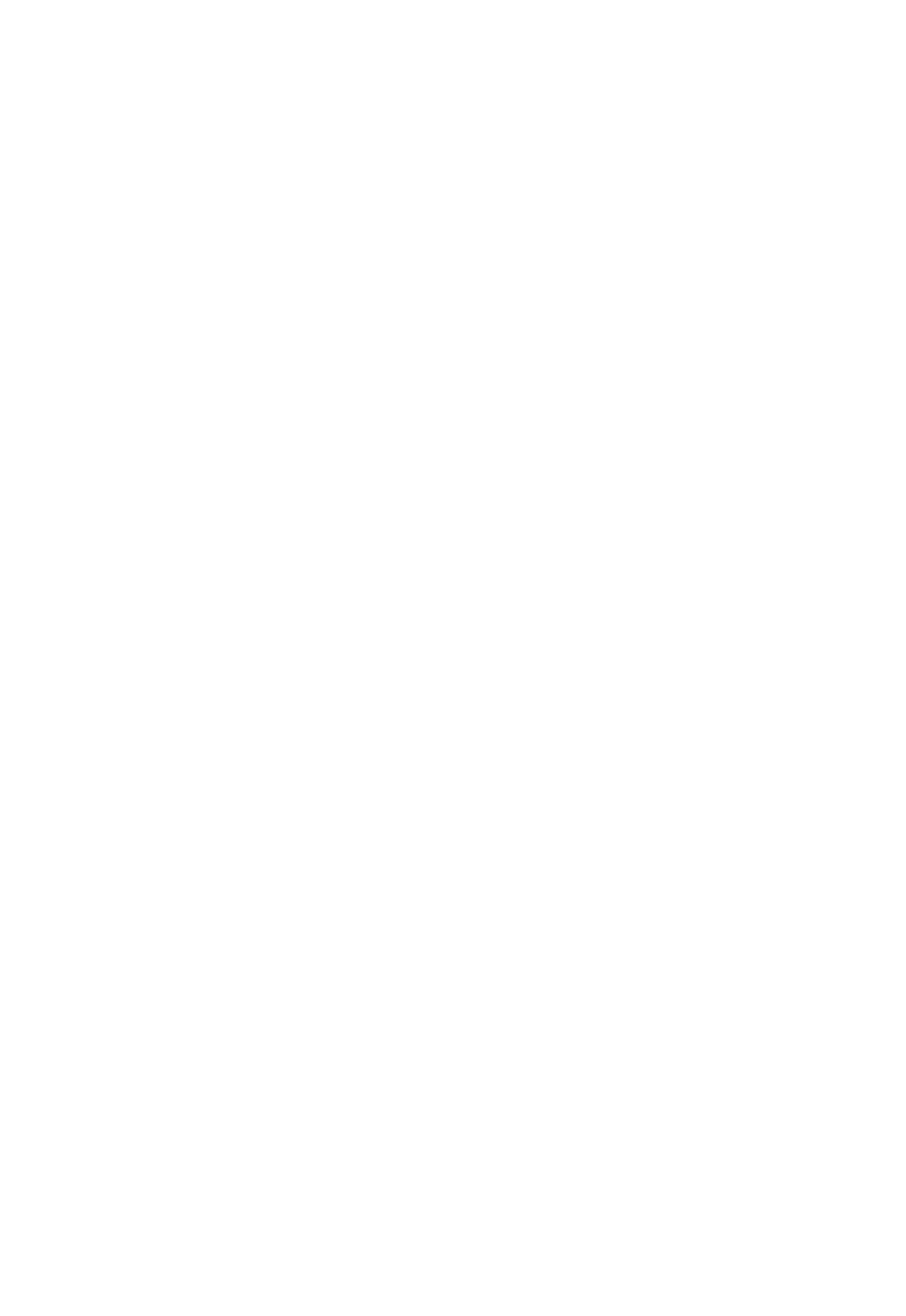
18
много ε-фазы или ее количество сильно возросло уже при относительно малых деформациях, а в ходе
дальнейших испытаний γ → ε превращение не реализуется, обнаруживается снижение пластических
характеристик и ударной вязкости. Последнее объясняется тем, что релаксация микронапряжений
становится затруднительной. Получение ε-мартенсита, как при термообработке, так и в процессе
нагружения, целесообразно во многих Fе-Мn и Fе-Сr-Мn сталях.
Анализ результатов исследований механических свойств сталей с аустенитной структурой, а также
их сопротивления разрушению в различных условиях изнашивания свидетельствует о том, что аустенит
обладает наиболее высокой из всех рассмотренных структур способностью к упрочнению,
пластичностью и ударной вязкостью. Для повышения предела текучести аустенита необходимо
использовать твердорастворный механизм, увеличение плотности дислокаций, измельчение зерна,
создание субструктуры, выделение дисперсных частиц. Расчет проведен по уравнению (1.1). Для
аустенита σ
0
выбрано согласно данным работы [3] равным 70 МПа. Ф.Б. Пиккерингом отмечается, что
наиболее сильное влияние при твердорастворном упрочнении аустенита оказывают углерод и азот [1].
Коэффициент упрочнения аустенита под влиянием этих элементов можно определить, если принять, что
существует прямолинейная зависимость предела текучести от концентрации углерода и азота. Для
углерода среднее значение K
i
в формуле (1.2) может быть принято ~ 775 МПа/%, исходя из того, что в
исследованных хромомарганцевых сталях, содержащих 10-12 % Мn и ~ I3 % Сr, имеющих чисто
аустенитную структуру, повышение концентрации этого элемента на 0,1 % вызывает прирост предела
текучести на 75-80 МПа. Коэффициент упрочнения К
i
для азота в исследованных хромомарганцевых
сталях равен ~ 1600 МПа/%. Максимальное содержание углерода и азота, которое можно допустить в
этих сталях с учетом хорошей технологичности, не должно превышать 0,3 %. Прирост предела текучести
при легировании углеродом и азотом в количестве 0,1 % каждого составляет
TP
∼ 230 и ∼ 160 МПа
соответственно.
Влияние марганца, вводимого в аустенитные стали даже в значительных количествах, в сравнении с
углеродом и азотом на упрочнение аустенита невелико [1] и его можно не учитывать. Аналогичное
заключение сделано и в отношении хрома, поскольку хромомарганцевые аустенитные стали,
содержащие 0,2-0,3 % С, имеют примерно такой же предел текучести, как марганцевые при том же
количестве углерода (σ
Т
~ 300 МПа). При плотности дислокации ρ = 10
8
см
−2
, что соответствует
недеформированному аустениту, ∆σ
Д
составляет ~ 10 МПа. Эту величину дает расчет по формуле (1.5),
если принять характерные для аустенита G = 8≅10
4
МПа, b = 0,25 нм [16]. Существенный вклад в
величину предела текучести может внести повышение плотности дислокаций. Так, если в результате
деформации она увеличивается до 10
10
-10
11
cм
−2
, то прирост предела текучести возрастает на 100-
316 МПа. В исследованных аустенитных сталях в зависимости от химического состава и режима
термообработки размер зерна (d) находится в широких пределах (1⋅10
−2
- 2⋅10
−3
см). Коэффициент К
У
в
формуле (1.3), определенный для ряда хромомарганцевых сталей, составляет ~ 0,23 МПа⋅м
1/2
, что
значительно меньше, чем для феррита. Это согласуется с данными работ [1, 16].
Прирост предела текучести за счет зернограничного упрочнения, рассчитанный по формуле (1.3),
составляет от 16 до 51 МПа. Заметный вклад в упрочнение аустенитных сталей может вносить получение
в результате деформации ячеистой дислокационной субструктуры. В зависимости от режима
деформирования, как показывают полученные данные, размер ячеек составляет 0,2-1,2 мкм.
Соответственно ∆σ
С
= 25-150 MПa (коэффициент К
С
принят равным 0,03 Н/мм) [16]. Предел текучести
недеформированного аустенита в хромомарганцевых сталях, содержащих 0,1-0,3 % С и 0,1 % N,
согласно расчетам может составлять от 330 до 523 МПа, а сильно деформированного - от 720 до
970 МПа. Для закаленного состояния расчетные и экспериментальные данные мало отличаются. Для
деформированного - расчетные значения предела текучести ниже в ~ 1,5 раза экспериментальных,
полученных после больших обжатий (~ 80 %) при температурах 450-650
о
С. Последнее может быть
объяснено тем, что фактическая плотность дислокаций после него выше, чем максимально принятая в
расчетах (ρ = 10
11
cм
−2
). Пользуясь формулой (1.5), можно определить, что плотность дислокаций должна
составлять ρ = 5,5-10
11
cм
−2
. В этом случае расчетные и экспериментальные значения предела текучести
аустенита близки. Вклад различных компонентов упрочнения недеформированного аустенита таков:
σ
0
∼ 21-13,5 %; ∆σ
ТР
- 71-75 %; ∆σ
Д
~ 3-2 %; ∆σ
З
~ 5-9,5 %. Из полученных данных следует, что наиболее
значительный вклад в приращение предела текучести вносит твердорастворное упрочнение за счет
углерода и азота. В сильно деформированном аустените хромомарганцевых сталей вклад различных
факторов в предел текучести несколько иной: σ
0
~ 6-5 %; ∆σ
Т.Р.
~ 19-28 %; ∆σ
Д
~ 53-59 %; ∆σ
З
∼ 4 %; ∆σ
С
~ 10-12 %. Предел текучести метастабильного аустенита может быть существенно повышен за счет
относительно небольших степеней деформации (10-20 %) при температурах ниже М
Д
. Это обусловлено