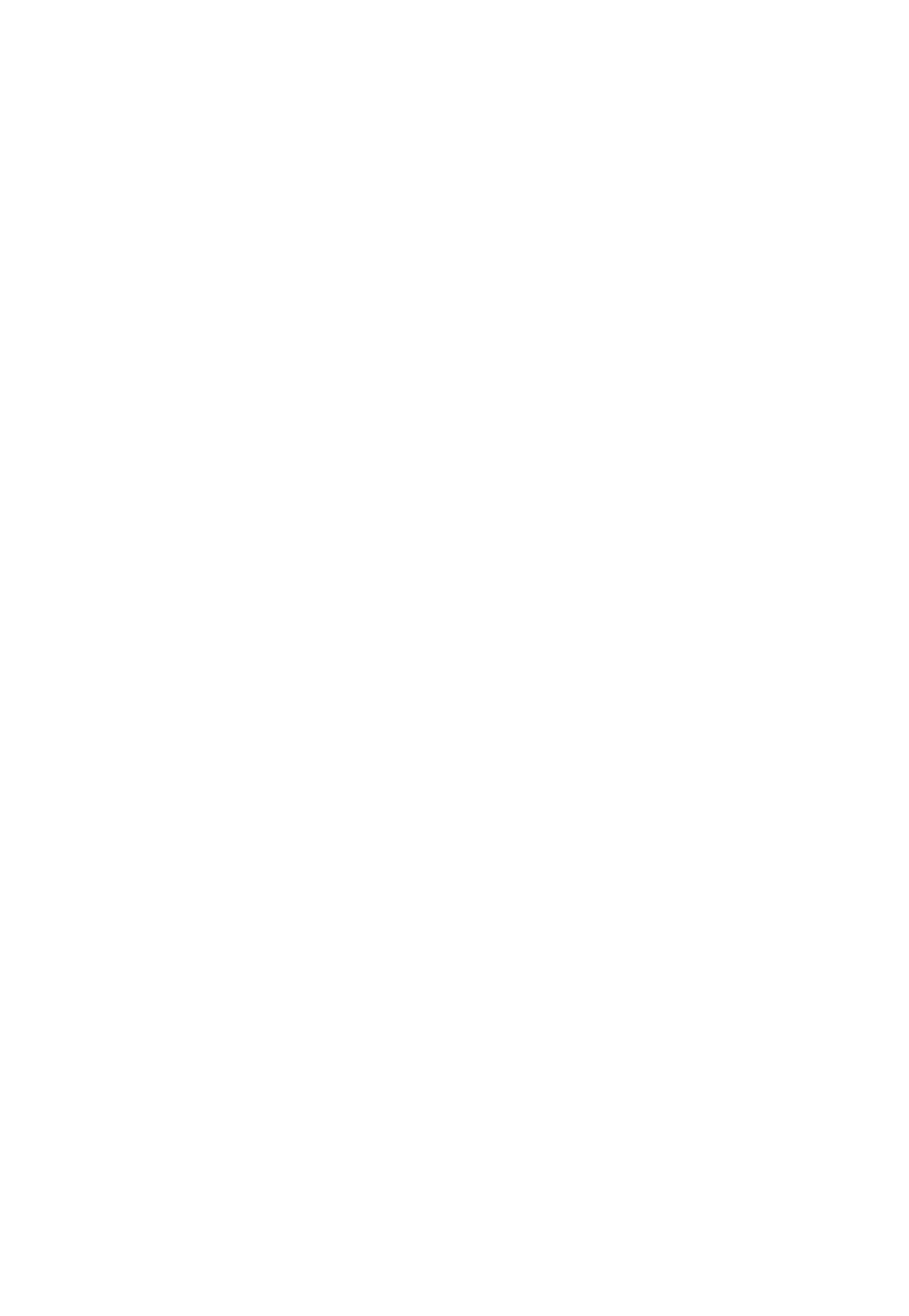
23
служебными свойствами не только при отрицательных температурах, что широко начинает
использоваться в криогенной технике [31], но и при повышенных. Сопротивление изнашиванию у
хромомарганцевого аустенита при 700-800
о
С значительно выше, чем у сталей с исходной мартенситной
структурой, что следует учитывать для инструментальных материалов.
Получение аустенита в сталях наряду с такими структурами как мартенсит, бейнит, ε-мартенсит,
феррит, карбиды, карбонитриды и интерметаллиды позволяет существенно повысить сопротивление
хрупкому разрушению и изнашиванию. В тех случаях, когда стали работают при температурах ниже М
Д
,
аустенит должен быть метастабилен и претерпевать при нагружении в процессе испытаний свойств или
эксплуатации мартенситные превращения определенной для каждого конкретного случая интенсивности
[32, 33]. С точки зрения повышенной способности к упрочнению и возможности реализовать
мартенситные превращения, а также двойникование предпочтение следует отдавать марганцевому и
хромомарганцевому аустениту с относительно низкой ЭДУ (≤ 40⋅10
−3
Дж/м
2
).
Большую роль в повышении свойств сталей играют дисперсные частицы, образующихся при
термообработке различных фаз. При их выборе необходимо руководствоваться следующими
положениями. Фазы должны относительно легко растворяться в аустените при нагреве под закалку и
выделяться при старении в виде дисперсных трудно коагулирующих частиц размером от десятков до
сотен ангстрем [3]. Кристаллические решетки частиц и матрицы должны быть близки по строению [14], а
выделяющиеся фазы обладать большой энергией межатомного взаимодействия и соответственно
высоким сопротивлением разрушению. По убывающей величине энергии, необходимой на разрушение,
карбиды можно расположить в следующий ряд: NbC, TiC, VC, Cr
23
C
6
, WC, Cr
7
C
3
, Mn
3
C, Fe
3
C [14]. Из
трех карбидов VC, NbС и TiC наибольшей прочностью связи с аустенитной и ферритной матрицами
обладает карбид ванадия. Карбиды TiC и NbC плохо растворяются в аустените. Вследствие этого трудно
получить пересыщенный твердый раствор и соответственно дисперсные частицы при старении. Однако
эти карбиды препятствуют росту аустенитного зерна, обладают высокой твердостью и должны быть
использованы в качестве упрочняющих фаз. В никельсодержащих сталях ими могут быть NiTi, Ni
3
Ti,
NiAl, Ni
3
Al, а в медьсодержащих - ε-фаза. Они также отвечают приведенным выше требованиям. В
малоникелевых мартенситностареющих сталях наиболее эффективны, как показали исследования,
частицы NiAl и Ni
3
Al. При комбинированном упрочнении целесообразно реализовать получение наряду
с интерметаллидами карбидов и карбонитридов титана, ванадия и ниобия.
Обобщая данные по энергоемкости различных структур, можно сделать вывод, что при создании
экономнолегированных высокопрочных сталей необходимо ориентироваться на низкоуглеродистый
мартенсит (для немагнитных сталей ε-мартенсит), нижний бейнит и аустенит. Для дополнительного
упрочнения следует использовать карбиды, карбонитриды ΙV и V групп, а в малоникелевых композициях
- интерметаллиды типа NiAl, Ni
3
Al, ε-фазы. В тех случаях, когда при нагружении могут реализовываться
мартенситные превращения, следует выбирать метастабильный аустенит. Наиболее эффективно
сочетание мартенситных, карбидных (интерметаллидных) фаз и метастабильного аустенита. Первые
позволяют получать высокие прочностные свойства, а второй - повышенную пластичность и
сопротивление разрушению. В ряде случаев в структуре наряду с вышеуказанными составляющими
может присутствовать феррит. При создании экономнолегированных сплавов многоцелевого назначения
необходимо ориентироваться на структурные классы: мартенситный, аустенитный, мартенситно-
аустенитный, аустенитно-мартенситный, аустенитно-ферритный, ферритно-аустенитный, бейнитно-
аустенитный, аустенитно-карбидный и аустенитно-интерметаллидный. Могут быть сплавы с
многофазной структурой, включающей мартенсит, бейнит, аустенит, феррит, карбиды и т.д. В сталях
мартенситного класса также следует получать в структуре некоторое количество остаточного аустенита.
При переходе от статических нагрузок к динамическим и возрастанию величины последних доля
аустенита в структуре должна возрастать, а стабильность - увеличиваться. В ряде случаев целесообразно
создавать безникелевые стали аустенитно-ферритного класса с метастабильным аустенитом.
Полученные результаты показывают, что, используя в качестве легирующих такие относительно
недорогие элементы как марганец, хром, кремний, углерод, азот, можно создавать
экономнолегированные сплавы многоцелевого назначения указанных выше структурных классов. При
необходимости целесообразно использовать небольшое количество никеля, молибдена, меди, ванадия, но
в значительно меньших количествах, чем в современных сталях и сплавах. Существенное уменьшение
или полное исключение из состава сплавов никеля, являющегося одним из наиболее дорогих элементов,
стало возможным, благодаря использованию других средств повышения устойчивости
переохлажденного аустенита, уменьшения блокировки дислокаций и соответственно повышения
пластичности и ударной вязкости. Так увеличить устойчивость переохлажденного аустенита и
обеспечить протекание мартенситного γ → α превращения даже при относительно малых скоростях