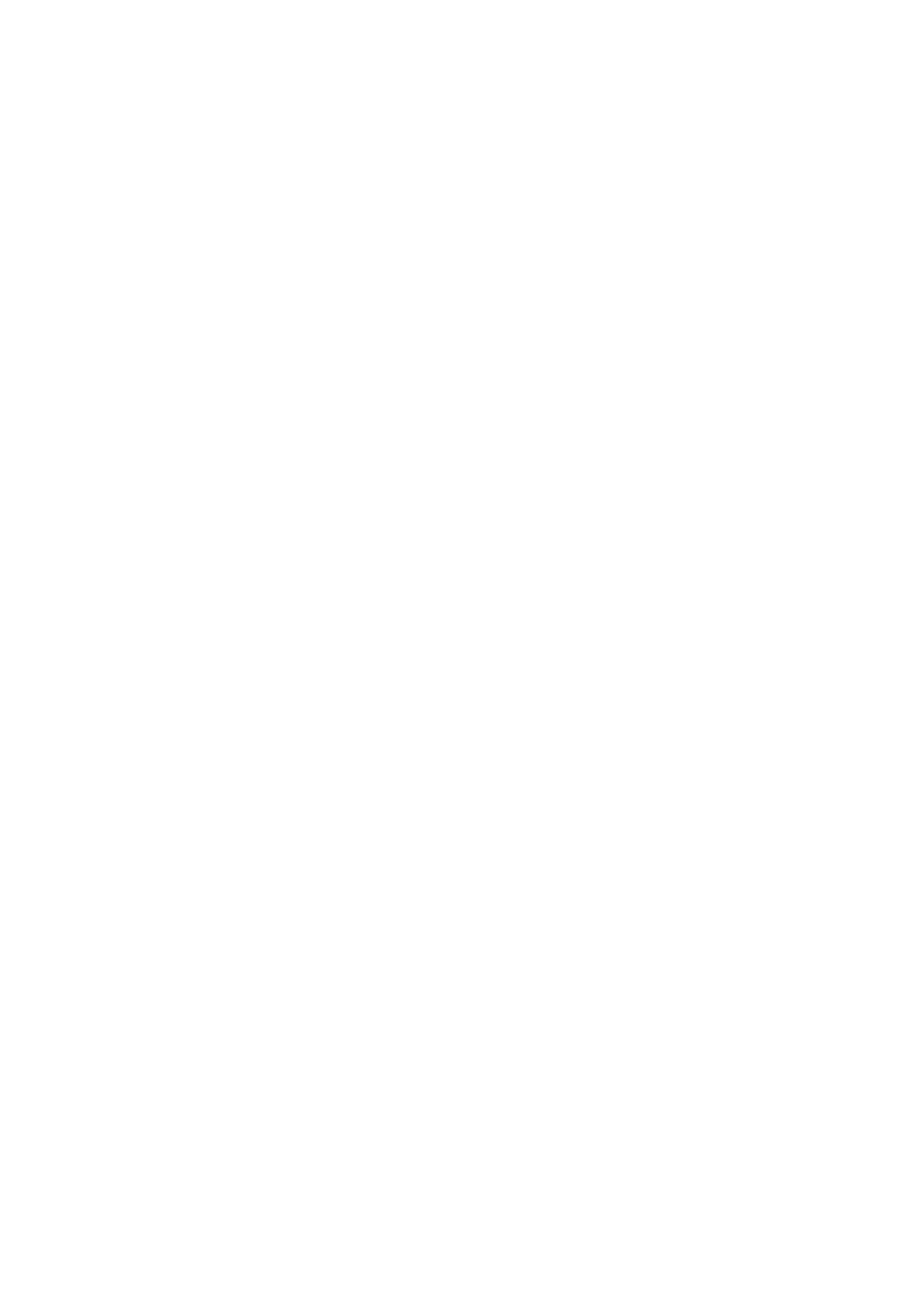
185
структуре подслоя, но делает, как это можно полагать, более стабильным из-за повышенного
растворения в нем углерода и хрома. На основании проведенных исследований были разработаны
способы повышения износостойкости деталей, работающих в условиях ударного нагружения и больших
контактных давлений за счет диффузионного хромирования и последующего "рассасывания" карбидного
слоя [303, 304]. Вопрос о необходимости иметь остаточный аустенит должен решаться с учетом
конкретных условий испытаний на износ или эксплуатации. Если при изнашивании может происходить
γ → α″ превращение определенной интенсивности, то остаточный аустенит полезен, и режимы
обработки должны быть направлены на его получение, оптимизацию количества и степени стабильности
применительно к конкретной стали и чугуну, а также условиям их изнашивания. Напротив, когда
изнашивание не вызывает протекания мартенситного превращения или количество и стабильность
аустенита существенно отличаются от оптимальных, он снижает износостойкость. Дифференцированный
подход к роли остаточного аустенита с учетом химического состава стали и конкретных условий
нагружения позволяют за счет обработок управлять его количеством, а также степенью стабильности и
соответственно повышать износостойкость.
5.3. Износостойкость марганцевых и хромомарганцевых сталей при абразивном воздействии
В данном разделе приведены результаты исследований гидро-, газо-, абразивной и ударно-
абразивной износостойкости сталей, чугунов и наплавочных материалов на Fе-Мn и Fе-Сr-Мn основах в
сопоставлении с применяемыми в промышленности материалами.
5.3.1. Сопротивление гидроабразивному износу
Гидроземлесосы, гидротурбины, флотационные машины и др., а также различные
гидротранспортные системы рудообогатительных комбинатов работают в потоке воды, содержащей
твердые абразивные частицы. Гидроабразивный износ деталей наносит значительный материальный
ущерб [305]. В связи с этим повышение сопротивления ему материалов является важной задачей.
Спецификой гидроабразивного воздействия являются: кратковременность нагружения отдельных
участков рабочих поверхностей, значительные локальные нагрузки и многократность их повторения.
Температурные вспышки, вызванные переходом в тепло значительной части кинетической энергии
абразивных частиц и быстрым охлаждением поверхности жидкой средой, способствуют возникновению
сложного напряженного состояния на поверхности детали. При этом следует учитывать кавитационное и
коррозионное воздействия жидкости. Все это приводит к разрушению отдельных микрообъемов
поверхностного слоя металла. Следовательно, при изыскании износоустойчивых материалов большое
внимание должно быть уделено изучению сопротивления такому специфическому микровоздействию
различных структурных составляющих, роли легирования и фазовых превращений, протекающих при
нагружении. Однако этому уделяется мало внимания, чем можно объяснить применение для деталей,
работающих в условиях гидроабразивного износа, сталей: Ст3, 25Л, 09Х12НДЛ, 12X18H10T и
10Х18Н3Г3Д2 [306], не обеспечивающих длительного срока эксплуатации гидроагрегатов. В работе
[307] впервые изучена гидроабразивная стойкость некоторых однофазных (феррит, аустенит, мартенсит)
и двухфазных (аустенит + феррит, аустенит + α′-мартенсит, аустенит + ε-мартенсит, аустенит + карбиды)
структур (табл. 5.26).
Испытания на гидроабразивный износ проводились на установке, аналогичной приведенной в [308].
В ней были изменены лишь способ крепления, форма, размеры образцов и конструкция уплотнений вала.
Абразивом служил мытый речной песок с размером частиц 0,1-0,2; 0,1-0,2 и 0,3-0,4 мм (поровну каждой
фракции); 1,0-1,2 мм при концентрации 200 г/л. Время гидроабразивного воздействия составляло 30 мин.
Принятая длительность испытаний находилась в пределах линейной зависимости весового износа от
времени. Фазовый состав определялся рентгеновским методом. Полученные данные свидетельствуют о
том, что наименьшее сопротивление гидроабразивному износу оказывает феррит (рис. 5.24).
Присутствие этой составляющей в сталях должно снижать их эрозионную стойкость. Аустенит (сплавы
05Н36 и 03Г38) превосходит феррит (армко-железо) по сопротивлению изнашиванию. Марганцевый
аустенит (03Г38) более износостоек, чем никелевый (05Н36). Последнее обусловлено более низкой ЭДУ
марганцевого аустенита и соответственно большей способностью к упрочнению при пластической
деформации [238]. Это одна из причин более высокой гидроабразивной износостойкости