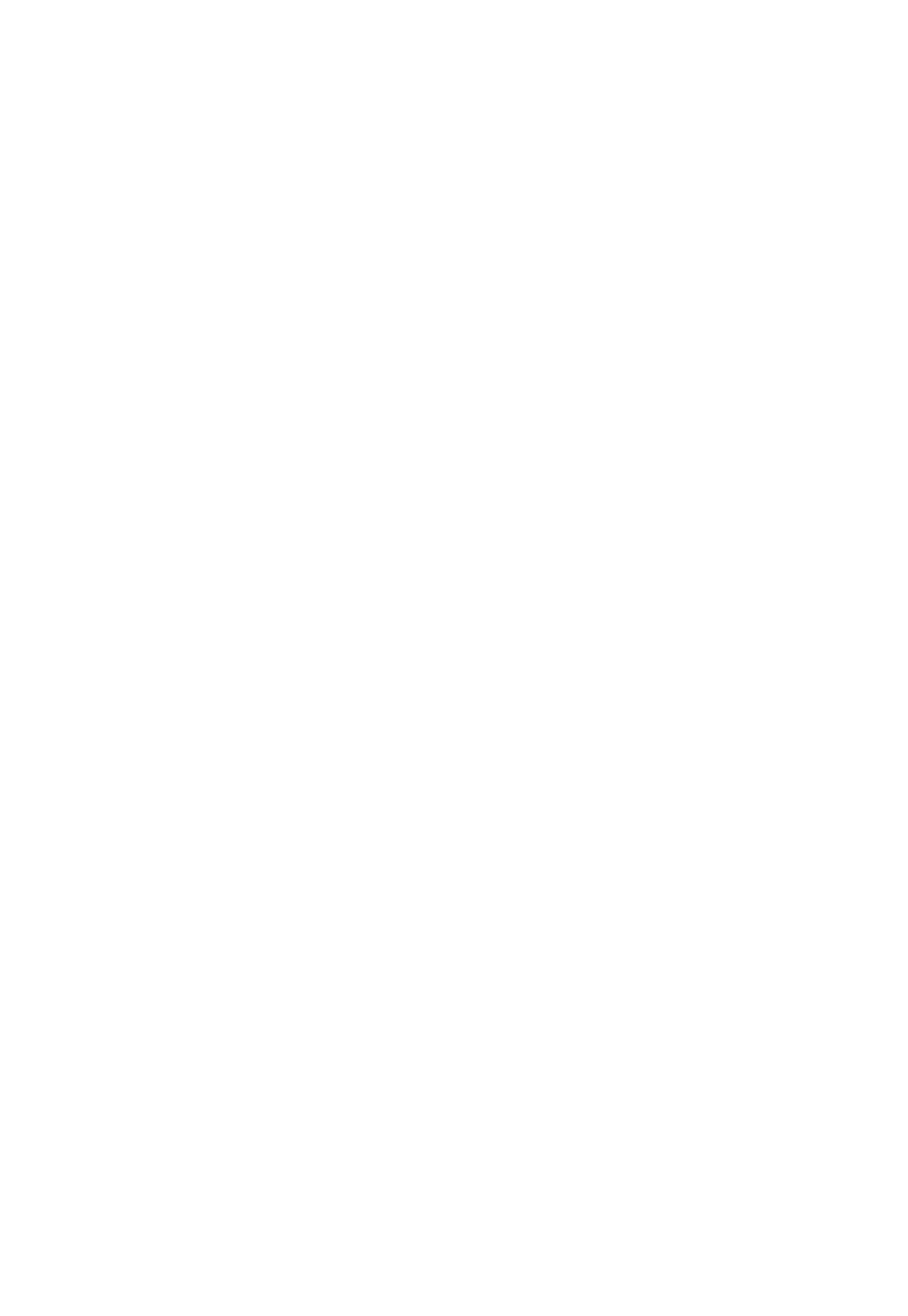
212
Наилучший комплекс свойств, достигаемый в рассматриваемой стали после закалки с 1060
о
С и
отпуска при 200
о
С, обусловлен не только определенным соотношением количества мартенсита,
карбидов и аустенита в структуре, но и оптимальной степенью стабильности последнего. Отпуск стали
XI2М при 200-300
о
С 1 ч вызывает частичный распад мартенсита и стабилизирует аустенит, уменьшая
интенсивность развития мартенситного превращения при кручении. Это приводит к снижению
прочностных свойств и повышению пластичности. Отпуск при 400-600
о
С 1 ч вызывает более полный
распад мартенсита и дестабилизирует аустенит за счет выделения из него карбидов. Только
определенный режим отпуска, обеспечивающий оптимальные фазовый состав и развитие мартенситного
превращения при испытаниях механических свойств, позволяет получить наиболее высокий их уровень.
Так после закалки с 1060
о
С отпуск целесообразно вести при 200-300
о
С, а после закалки с 1200
о
С - при
400
о
С [366]. Положительная роль оптимального количества остаточного аустенита обнаружена и в стали
Х10Ф [367]. При исследовании влияния температуры нагрева под закалку в интервале от 900 до 1150
о
С
на фазовый состав, структуру и свойства этой стали установлено, что по мере повышения температуры
нагрева под закалку количество остаточного аустенита возрастает до 50 %, и снижается доля мартенсита
и карбидов.
Наиболее высокий уровень прочностных свойств, пластичности и ударной вязкости стали Х10Ф
обеспечивает закалка с 1000
о
С (τ
ПЧ
= 1670 МПа, g = 6,1 %, KC = 27 Дж/см
2
), когда количество
остаточного аустенита составляет 12 %. После закалки с 900
о
С в структуре практически отсутствует
остаточный аустенит, в результате чего получены более низкие значения механических свойств (τ
ПЧ
=
1530 МПа, g = 4,4 %, KC = 12 Дж/см
2
). Повышение температуры нагрева под закалку до 1100
о
С также
снижает механические свойства (τ
ПЧ
= 1280 МПа, g = 1,7 %, KC = 16 Дж/см
2
), что объясняется
увеличением в структуре сверх оптимального количества остаточного аустенита (24 %) и существенным
повышением его стабильности, а также увеличением содержания углерода в мартенсите, уменьшающим
его пластичность и ударную вязкость. Исследование влияния отпуска в интервале от 200 до 520
о
С 1 ч на
структуру и свойства Х10Ф позволило заключить, что целесообразно проводить после закалки низкий
отпуск, не превышающий 200
о
С. Он сохраняет в структуре наряду с мартенситом и карбидами
метастабильный остаточный аустенит и обеспечивает при этом хорошее сочетание механических
свойства (τ
ПЧ
= 1565 МПа, g = 8,1 %, KC = 20 Дж/см
2
) [367].
В главе 3 была показана целесообразность термообработки с нагревом в МКИ марганцевых и
хромомарганцевых сталей для получения в их структуре требуемого количества аустенита и его
стабильности. В работе [368] изучены особенности процессов структурообразования в
низколегированных сталях перлитного класса 40ГС и 40Г2С при нагреве и выдержке их в МКИ.
Установлено, что после закалки от температур двухфазной области структура представляет собой
мартенсит, феррит, аустенит (5-7 %) и карбиды. Мартенсит, образующийся в результате закалки из
аустенита, обогащенного углеродом и марганцем, после выдержки в МКИ имеет более высокую
твердость (на 10-20 %), чем в случае обычной закалки. Сталь 40ГС, закаленная из МКИ, затем была
нагрета в γ-область (выше Ас
3
), охлаждена в воде и отпущена при 200°
о
С 1 ч. После повторной закалки
структура состояла из пакетного мартенсита, в котором согласно данным микроспектрального анализа
сохраняется созданная предыдущей обработкой неоднородность в распределении легирующих
элементов. Измерение мартенситных пакетов показало их существенное измельчение. Следствием этого
явилось получение повышенного уровня механических свойств: σ
0,2
= 1770 МПа, σ
В
= 2110 МПа, δ =
10 %, ψ = 42 %, KCU = 0,40 МДж/м
2
, что выше, чем после закалки с рекомендуемой для этой стали
температуры (880
о
С) и низкого отпуска (σ
0,2
= 1630 МПа, σ
В
= 1950 МПа, δ = 7,5 %, ψ = 29 %, KCU =
0,32 МДж/м
2
).
Подобные результаты получены в работе [369] на стали 30ХМА после термообработки с
предварительным нагревом в МКИ. Его проводили при 770
о
С 2 ч, после чего образцы переносили в печь
с температурой 850°
о
С и выдерживали 1 и 5 мин. Затем их охлаждали в масле и отпускали при 200°
о
С
2 ч. Для сравнения определяли свойства после закалки с 850°
о
С (выдержка 20 мин) и отпуска при 200,
560 и 650°
о
С (2 ч). Типовая термообработка 30ХМА предусматривает после закалки с 850°
о
С отпуск при
560°
о
С. После закалки с 850
о
С и низкого отпуска достигается сравнительно высокий уровень
прочностных свойств, но низкие значения пластичности (табл. 5.47, режим 1). После типовой
термической обработки (режим 2) пластичность существенно возрастает, но заметно снижаются
прочностные свойства. После отпуска при 650°
о
С (режим 3) уровень прочности наиболее низок, но при
этом увеличивается способность стали к локализованной деформации и ударная вязкость. Наиболее
высокий уровень прочностных, пластических свойств и ударной вязкости получен после режимов
термообработки, включающих предварительный нагрев и выдержку в МКИ или ПКИ (табл. 5.47,
режимы 4-6). Увеличение продолжительности выдержки при 850°
о
С с 1 до 5 мин после