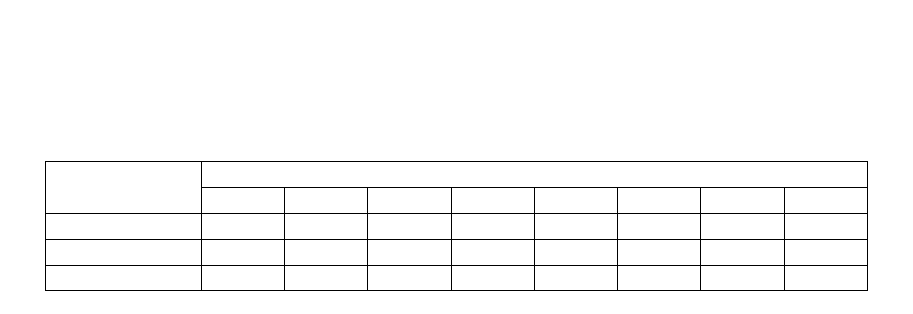
195
удаленном от поверхности на 15 мм, значения ударной вязкости существенно выше: KCU = 1,25 и
KCU
−40
= 0,79 МДж/м
2
. Это обусловлено более высокой скоростью охлаждения поверхности по
сравнению с центральной частью отливки, в которой происходит выделение карбидов по границам зерен.
Определение износостойкости под влиянием дробеструйного воздействия под углом атаки 45
о
свидетельствует о том, что в образцах, вырезанных из поверхностного слоя, она ниже (ε = 1,28), чем из
сердцевины (ε = 1,8). Это также обусловлено более высокой стабильностью аустенита по отношению к
образованию мартенсита деформации в поверхностном слое.
Важно подчеркнуть, что в сталях, содержащих 4-10 % Mn, можно получать в структуре различное
соотношение мартенсита, аустенита, карбидов и использовать их в условиях абразивного воздействия
[278, 317, 319]. Высокая абразивная износостойкость достигается закалкой с 750-850
о
С после
предварительного получения ферритокарбидной смеси в результате высокого отпуска. При этом
обеспечивается структура метастабильно аустенита, армированного частицами твердых фаз, интенсивно
превращающегося в мартенсит деформации. Факторы, обеспечивающие стабилизацию аустенита
(повышение температуры нагрева под закалку, низкий отпуск и др.) должны использоваться для
повышения износостойкости, при высокой интенсивности ударно-абразивного воздействия.
Разработанные с использованием указанных положений стали и режимы их термической обработки
могут быть широко применены для рабочих органов дробильного оборудования и других
быстроизнашивающихся деталей. Стали, содержащие 1,1-1,3 % С, 6,5-10,0 % Mn, дополнительно
легированные сильными карбидообразующими элементами, внедрены на комбинатах: Макеевском
им. С.М. Кирова, ММК им. Ильича и МК «Азовсталь».
Учитывая, что на многих предприятиях широко применяется сталь 110Г13Л, подвергающаяся
закалке с 1050-1100
о
С в воде, что обеспечивает ей высокую ударно-абразивную, но низкую абразивную
износостойкость, была изучена возможность ее повышения. Для этого исследовалось влияние
температуры нагрева под закалку, продолжительности отпуска при 600
о
С (от 1 до 10 ч), а также
комбинированной обработки, предусматривающей предварительный высокий отпуск и последующую
закалку в интервале температур от 850 до 1050
о
С на абразивную и ударно-абразивную износостойкость
[324. 325]. Установлено, что при повышении в исследованном интервале температуры нагрева под
закалку, ударно-абразивная износостойкость возрастает в 1,5 раза, а абразивная - снижается на ∼ 40 %.
Это обусловлено уменьшением количества карбидов в структуре за счет их растворения в аустените и
его стабилизацией по отношению к деформационному мартенситному превращению. Увеличение
продолжительности отпуска при 600
о
С действует в противоположном направлении, увеличивая
абразивную и снижая ударно-абразивную износостойкость. Последнее вызвано выделением карбидов,
количество которых возрастает с увеличением продолжительности выдержки. В результате аустенит
дестабилизируется и активизируется γ → α″ превращение. Кроме того, армирование аустенитной
матрицы карбидами является важным дополнительным фактором, усиливающим этот эффект.
Комбинированная обработка позволяет после рационального режима ее проведения повысить
абразивную и ударно-абразивную износостойкость по сравнению с уровнем, достигаемым после
обычной закалки с 1050-1100
о
С. Однако необходимо дифференцированно выбирать продолжительность
отпуска и температуру нагрева. С целью повышения абразивной износостойкости следует иметь
температуру аустенитизации после отпуска при 600
о
С 750-850
о
С, а при необходимости увеличить
ударно-абразивную - 1000-1050
о
С. Положительный эффект такой обработки обусловлен получением
более мелкого зерна в результате фазовой перекристаллизации, а также присутствием не растворившихся
карбидов. В случае абразивного воздействия в аустенитной матрице их должно быть существенно
больше, чем при ударно-абразивном.
В работах [140-142] показаны преимущества цементуемых низкоуглеродистых марганцевых сталей
по сравнению с 110Г13Л в уровне механических свойств и обрабатываемости резанием. Абразивная и
ударно-абразивная износостойкость после цементации и последующей термообработки изучалась на
сталях 08Г4АТФ, 08Г7АФ и 08Г10Х2АФ (табл. 5.33) [141].
Таблица 5.33
Химический состав исследованных цементуемых марганцевых сталей
Содержание элементов, мас. %
Сталь
С Mn Сг Si V Аl Ti N
08Г4АТФ 0.08 4,1 - 0,41 0,17 0,03 0,05 0,03
08Г7АФ 0,08 7.4 - 0,45 0,21 0,03 - 0,04
08Г10Х2АФ 0,08 10.2
1.8
0,50 0,25 0.04
-
0,05