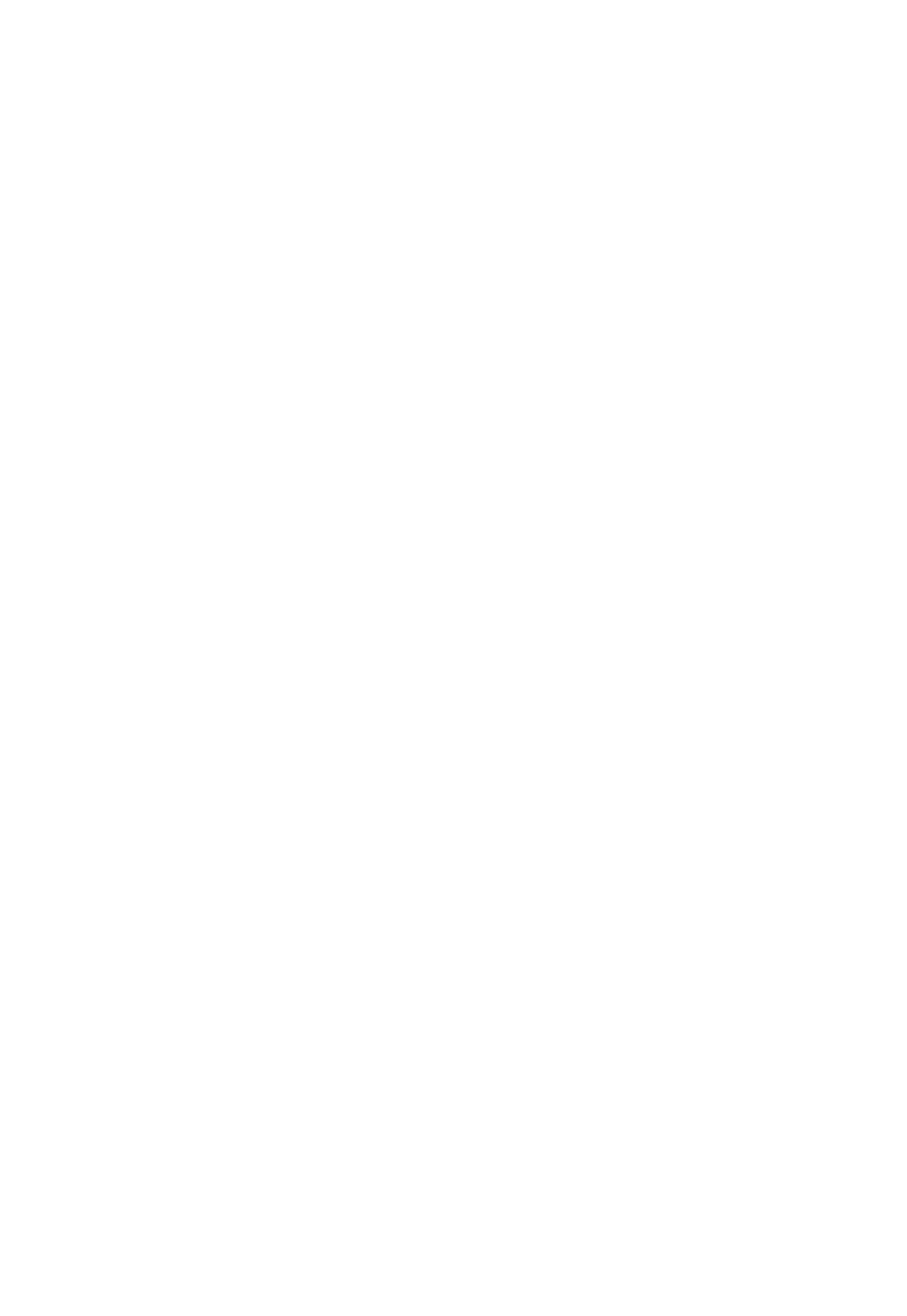
176
В работе [280] исследовалась износостойкость при сухом трении скольжении литых сталей 70Г6ФЛ
и 130Г6ФЛ. Контртелом служила сталь 40Х твердостью HRC 55-67. Эталоном являлась 110Г13Л.
Наиболее высокую износостойкость имела 130Г6ФЛ после закалки с 900
о
С и отпуска при 650
о
С 1 ч.
Этому соответствовал наибольший прирост микротвердости на поверхности после изнашивания (∆Н
◊0,980
∼ 2000 МПа). Согласно рентгеновским данным при этом образовалось 40 % мартенсита деформации, что
подтверждается металлографическими исследованиями. В 70Г6ФЛ после закалки с 900
о
С и отпуска
200
о
С 1 ч износостойкость существенно ниже, чем в предыдущем случае, хотя по исходной твердости
она мало отличалась от 130Г6ФЛ. Это объясняется тем, что в этой стали прирост микротвердости не
превышал ∆Н
◊0,980
∼ 300 МПа, поскольку в ней образование мартенсита деформации составляет 10 %.
Приведенные данные позволили заключить, что сопротивление изнашиванию существенно зависит от
количества и степени стабильности аустенита по отношению к деформационному мартенситному
превращению. Сталь 110Г13Л имела более низкую износостойкость, чем исследованные с более низким
содержанием марганца и дополнительно легированные ванадием. Из стали 130Г6ФЛ были выплавлены
опытные ролики для чугуноразливочной машины Макеевского металлургического комбината. Однако в
некоторых из них появились трещины, явившиеся следствием распада аустенита с образованием
троостита при замедленном охлаждении отливок. В связи с этим содержание марганца было увеличено
до 8 %, а углерода снижено до 1,2 %, что повысило сопротивление аустенита к распаду. Сталь 120Г8ФЛ
была внедрена вместо 110Г13Л для изготовления роликов, что повысило их долговечность в 1,5 раза
[280]. В тех случаях, когда нежелательно проводить после закалки отпуск при 650
о
С, снижающий
ударную вязкость исследованных сталей, его следует осуществлять лишь для поверхностного слоя,
сохраняя в сердцевине преимущественно аустенитную структуру. Другим направлением, позволяющим
получать различные свойства поверхности и сердцевины, является использование низкоуглеродистых
цементуемых Fе-Мn сталей, содержащих ≤ 0,12 % С, 6-12 % Мn. Они могут быть дополнительно
легированы другими элементами, в частности, 0,5-2 % V. В этом случае удается получить высокий
уровень прочностных свойств (σ
0.2
≥ 900 МПа, σ
B
≥ 1200 МПа) при достаточной пластичности (δ ≥ 10 %,
ψ ≥ 30 %), ударной вязкости сердцевины (KCU ≥ 0,9 МДж/м
2
) и износостойкость высокоуглеродистого
поверхностного слоя, имеющего метастабильный аустенит, армированный карбидами или
карбонитридами [281-286].
5.2.4. Малоуглеродистые хромомарганцевые стали переходного и аустенитного классов
В работе [269] исследовалась относительная износостойкость (ε
И
) при сухом трении
хромомарганцевых сталей с метастабильным аустенитом 07Х9АГ8МД2ФС, 10Х10АГ8МД2ФС,
20Х13АГ10МД2ФС, в которых варьировалось содержание углерода и соответственно стабильность
аустенита для выяснения роли развития γ → α″ превращения в процессе изнашивания трущихся
поверхностей. Их износостойкость сравнивалась с таковой у 30Х10Г10, 17ГС, Ст3, 45, применяемых для
различных деталей, а также наплавленный металл, полученный с использованием электродов УОНИ 13-
45. Испытания проводились на машине МИ-1M по схемам колодка - ролик и ролик – ролик. Их режимы:
давление (Р), скорость скольжения (V), путь трения (l) приведены в табл. 5.19. Контртелом при
испытаниях образцов служила сталь М76 (HB 240). Температура нагрева контролировалась термопарой,
приваренной к образцу. Фазовый состав определялся на феррометре ФА-1.
Испытания по режиму 1 показали, что наибольшую износостойкость имеет аустенитная сталь
20Х10АГ8МД2ФС, а наименьшую - 07Х9АГ8МД2ФС с преимущественно мартенситной структурой.
Определение фазового состава в поверхностных слоях образцов, испытанных по режиму 1 (температура
нагрева образцов не превышала 50
о
С), позволило заключить, что прирост мартенсита в
07Х9АГ8МД2ФС самый небольшой, поскольку в ней очень мало остаточного аустенита (∼ 20 %). В
аустенитных метастабильных сталях 10Х10АГ8МД2ФС и 20Х10АГ8МД2ФС он значительно выше (рис.
5.21, а). Это позволяет сделать вывод о важной роли деформационного мартенситного превращения при
изнашивании в отсутствие значительного нагрева металла на поверхности трения. Положительное
влияние углерода на повышение износостойкости второй стали по сравнению с первой обусловлено тем,
что он, несмотря на некоторую стабилизацию аустенита, усиливает способность его к наклепу в процессе
трения, увеличивает твердость мартенсита деформации и активизирует динамическое старение. Важно
подчеркнуть, что все исследованные хромомарганцевые стали по уровню износостойкости значительно
превосходят 17ГС, Ст3, 45, а 20Х13АГ10МД2ФС - 30Х10Г10 (табл. 5.19).