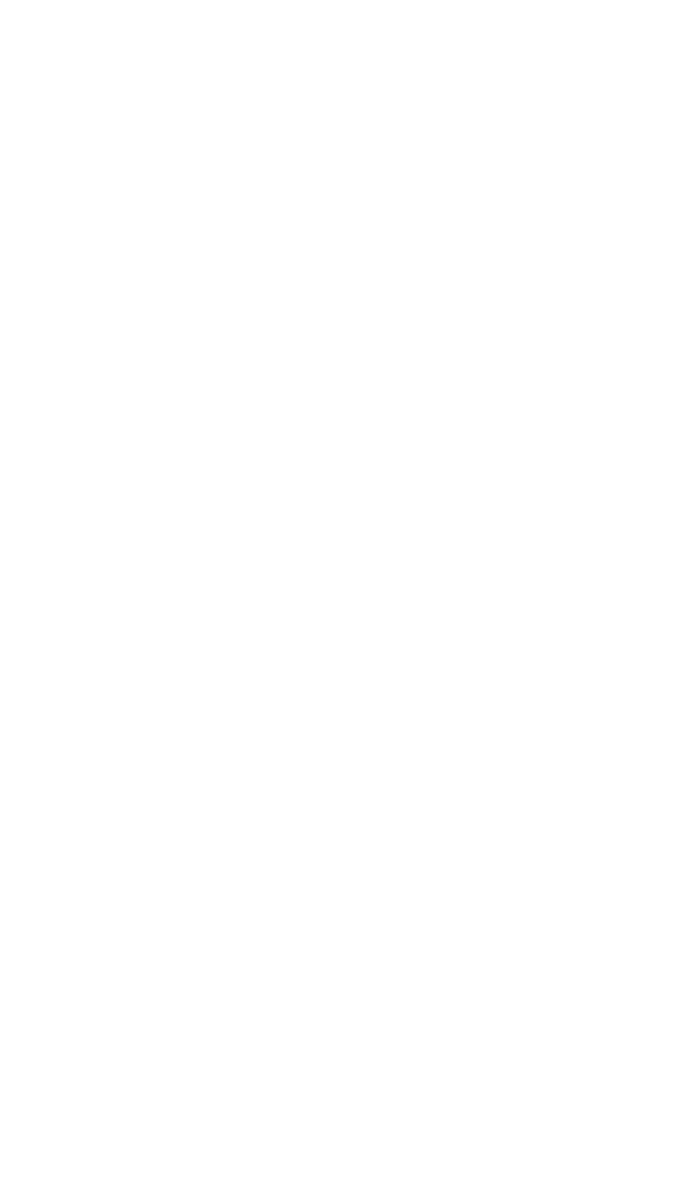
690 NONDESTRUCTIVE INSPECTION
1. Access. Access to perform an inspection is essential and must be
considered as a primary engineering design parameter. An inspection can-
not be performed unless key areas of the component are accessible. This
may require disassembly in some cases and must be considered as a part
of the life-cycle maintenance procedures.
2. Capability. The inspection method must be capable of detecting the re-
quired flaw sizes to a defined reliability and confidence levels. Selection
of the applicable inspection method is primarily the responsibility of the
NDI engineer. A design cannot be supported if the critical flaw size is
below the detection capability level.
3. Reliable. The reliability of an inspection method is dependent, in part,
on the reproducibility of the measurements being made by the NDI pro-
cedure. The reproducibility of a procedure is, in turn, largely dependent
on the ‘‘calibration’’/setup used for the NDI procedure. Additionally, the
process must be repeatable, i.e., the NDI procedure is dependent on pro-
cess control rigor in application of the NDI method/process.
4. Human Factors. Since the reproducibility and repeatability of an NDI
procedure are dependent on rigor in process control, the skill of the hu-
man operator is an important factor in NDI application. Most NDI
methods/procedures require dexterity in application and detection/pattern
recognition skills for ‘‘interpretation’’ and decision processing. Most NDI
methods produce indirect measurements of a property or configuration
and relates those measurement to a desired property or behavior. Profi-
ciency in such relationships are a product of the knowledge and skill of
the NDI engineer and the knowledge and skill of the inspector/operator.
8.4 Quantification of NDE Capabilities
Nondestructive inspection methods have a long history of application that range
from simple visual inspections to complex ultrasonic and eddy current inspec-
tions. Since most inspections were originally practiced as an art, the craft was
subject to a wide range of assumptions, exaggerations, misinformation, and mis-
applications. The requirement to quantify the detection capability has reduced
many of those deficiencies but has generated new barriers from practitioners
who resist change. Without discipline and quantification, many of inspection
procedures must be regarded as ‘‘inspection ceremonies.’’ This applies to many
established procedures that were generated and perpetuated by ‘‘specification.’’
The issue at hand is not ‘‘the smallest flaw that has been detected, but the largest
flaw that has been missed’’ by an inspection procedure or operator.
The methodology that is applied to quantification of nondestructive
inspection/evaluation capability is known as a ‘‘probability of detection (POD)’’
assessment. The single-valued inspection capability parameter that is provided
by the POD method is a crack size that can be detected (reliably) by application
of an inspection procedure. That value is often quoted as the 90/95 or the a
NDE
(nondestructive evaluation) capability/parameter and is the value that is used in
engineering design for use of nondestructive inspection as an element of vali-
dating component structural integrity.