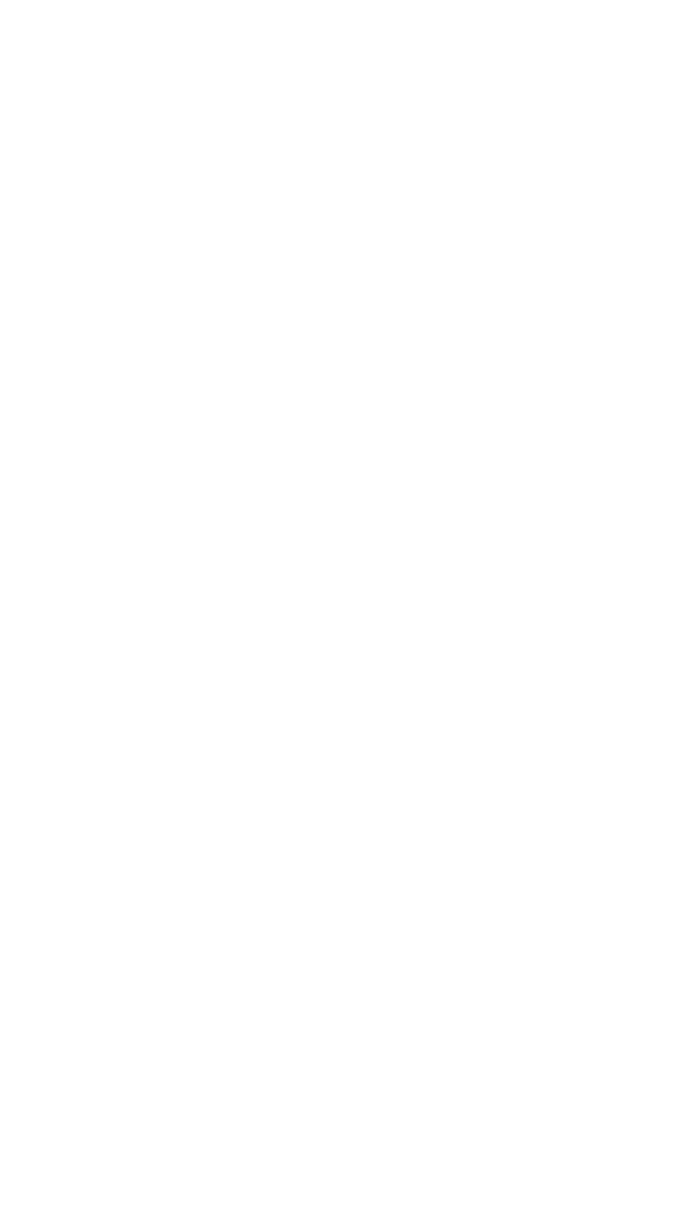
662 NONDESTRUCTIVE INSPECTION
inspection is often chosen for inspection of thin metallic structures such as those
in aircraft.
Using the relationships for the reflection and transmission coefficients, a great
deal of information can be deduced about any ultrasonic inspection situation
with the acoustic wave incident at 90
⬚ to the surface. For other angles of inci-
dence, computer software is often used to analyze the acoustic interactions. For
more complicated materials or structures such as fiber-reinforced composites
analytical predictions require the use of a rather complex analysis. In some cases,
more complicated modes of wave propagation can occur. Examples of these
include Lamb waves (plate waves), Stoneley waves (interface waves), Love
waves (guided waves in the layer on a coated material), and others.
3.4 Inspection Process
Once the type of ultrasonic inspection has been chosen and the optimum ex-
perimental parameters determined, then one must choose the mode of presen-
tation of the data. If the principle dimension of the flaw is less than the diameter
of the transducer, then the A-scan method may be chosen, as shown in Fig. 6.
The acquisition of a series of A-scans obtained by scanning the transducer in
one direction across the specimen and displaying the data as distance versus
depth is referred to as B-scan. This is the mode most often used by medial
ultrasound instrumentation. In the A-scan mode, the size of the flaw may be
inferred by comparing the amplitude of the defect signal to a set of standard
calibration blocks. Each block has a flat bottom hole (FBH) drilled from one
end. Calibration blocks have FBH diameters that vary in -in. increments.
1
––
64
Therefore, a number 5 block has a -in. FBH. By comparing the amplitude of
5
––
64
the signal from a calibration block with one from a defect, the inspector may
specify a defect size as equivalent to a certain size FBH. The equivalent size is
meaningful only for approximately smooth flaws that are nearly perpendicular
to the path of the ultrasonic beam.
If the flaw size is larger than the transducer diameter, then the C-scan mode
is usually selected. In this mode, shown in Fig. 10, the transducer is rastered
back and forth in two directions across the part. In normal operation a line is
traced on a monitor or piece of paper. When a flaw signal is detected between
the front and back surface, a line with much increased darkness appears on the
paper or monitor. Using this mode of presentation, a planar projection of each
flaw is presented to the viewer and its positional relationship to other flaws and
to the component boundaries is easily ascertained. Unfortunately, the C-scan
mode does not show depth information, unless an electronic gate is set to capture
only information from within a specified time window or time gate in the part.
With current computer capability it is a rather simple matter to store all of the
returning A-scan data and display only the data in a C-scan mode for specific
depth. The C-scan mode provides a visual representation of a slice of the ma-
terial at a certain depth and is very useful for inspection purposes.
Depending on the structural complexity and the attenuation of the signal by
the material, flaws as small as 0.015 in. can be reliably detected and quantified
using this inspection method. An example of a typical C-scan printout of an
adhesively bonded test panel is shown in Fig. 11. While the panel was fabricated
with a Teflon void-simulating implant in the center, the numerous additional
white areas indicate the presence of a great deal of porosity in the part.
50,58